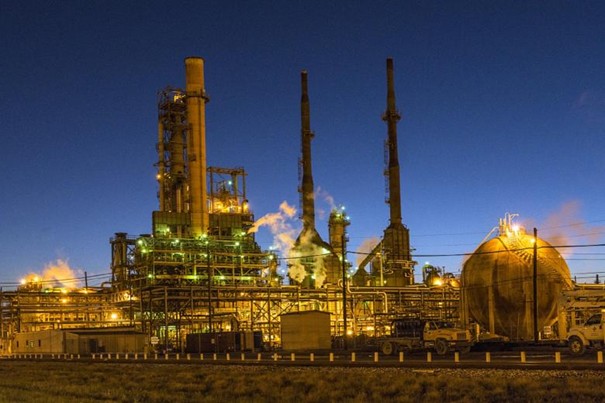
Source: Pixabay
In the area of plant safety and process simulation, BAM pools its research expertise in the safe design and operation of chemical and process engineering of industrial plants as well as facilities for storing hazardous substances such as explosives and pyrotechnics. The energy transition, digitalization, decarbonization, and new geopolitical requirements demand more flexibility, efficiency, and resilience from industry.
Plant safety describes the full set of methods, technical equipment, and operating strategies for operating a plant safely and minimizing its effects in the event of an incident. In order to consider plant safety holistically and to increase it under changing boundary conditions, BAM relies on experiments from laboratory to real scale as well as modern simulation methods. Process simulation combines digital methods, models, and tools to describe and predict the interior of a process and to use them, e.g., to increase efficiency in operation.
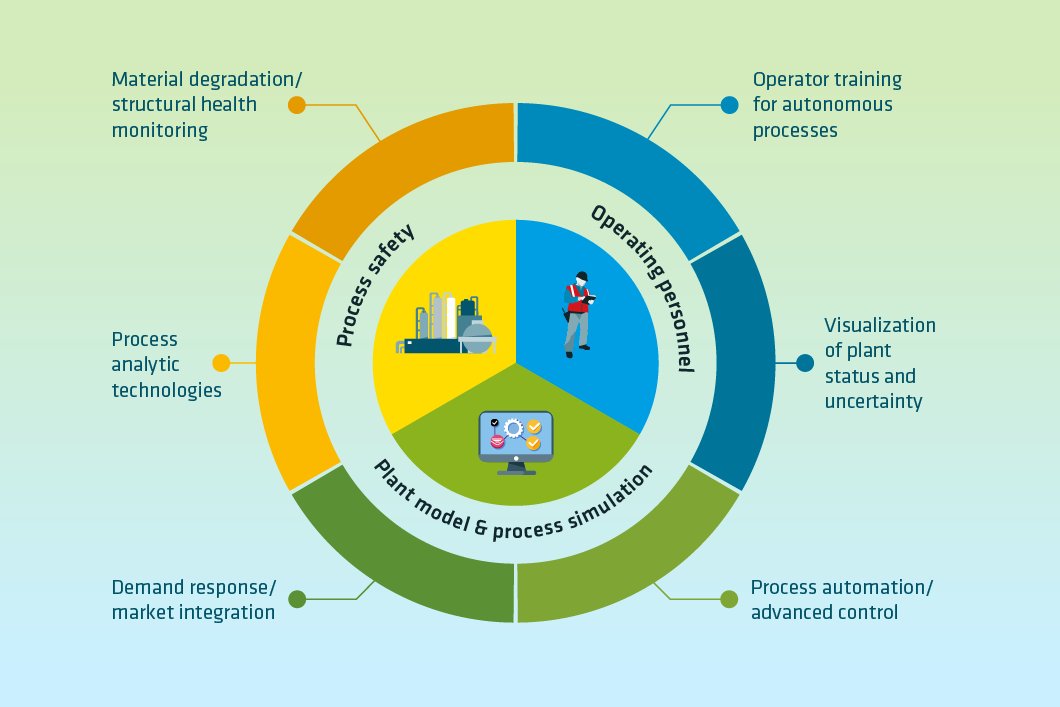
Source: BAM
Three main topics are considered in connection with plant safety and process simulation: In the area of “safe and environmentally acceptable processes”, the researchers are investigating assessment methods for plant safety in operation on the one hand, while on the other hand the focus is on human-machine interaction, for example in semi-autonomous plants. The second focus area brings together materials, manufacturing processes, and models to ensure process and plant safety. BAM develops models for process simulation. These are validated and qualified using real experiments. The focus on real-time plant monitoring looks at autonomous test platforms, methods, and models for experimental design.
BAM also carries out safety assessments to ensure that explosives and pyrotechnics are stored safely in accordance with explosives regulations.
Selected Projects
Increasing the safety of plant operation through mixed reality technology: MR4SafeOperations – MR4B
AR and AI support for complex operating and maintenance tasks: Handbuch2AR – MR4B