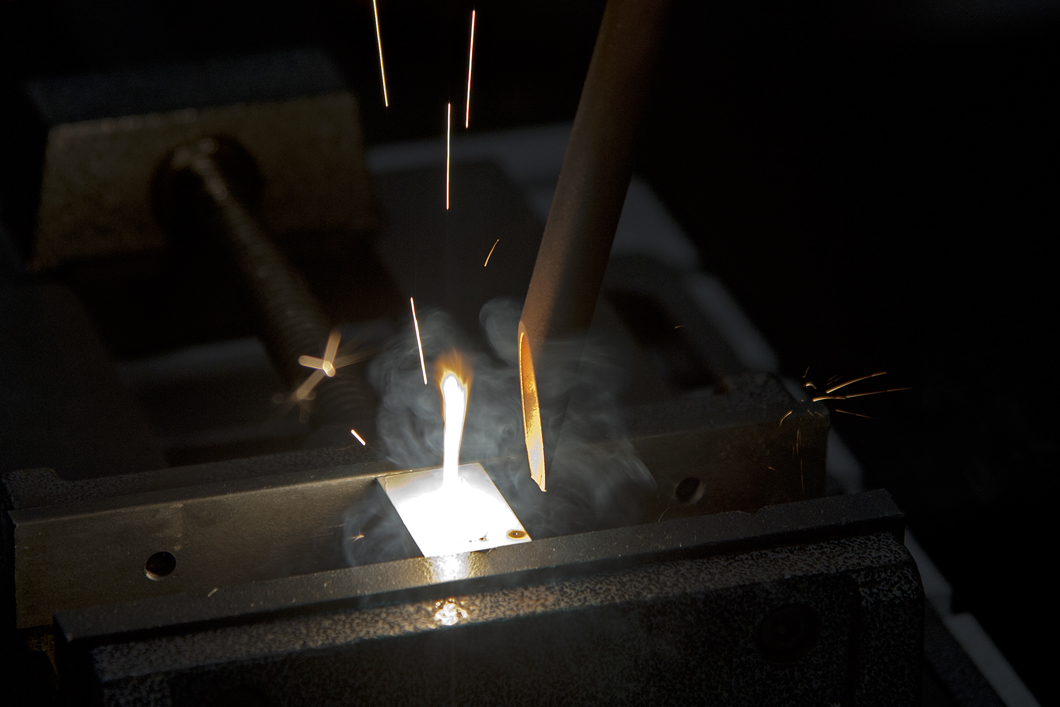
Surface structuring by laser implantation leads to significant increase in hardness and wear resistance e. g. on wear-prone tools
Source: BAM
BAM-developed processes may lead to far-reaching changes in joining and forming technology. An interdisciplinary team developed a precision pulsed laser system for innovative welding and structuring processes that are taking on the challenge of new materials.
The future of welding
What does the future of welding look like? An interdisciplinary working group in the Welding Technology Division called "Processes and technologies for heavy-duty welded joints" headed by Prof. Kai Hilgenberg deals with this issue. Prof. Hilgenberg is a junior professor at the TU Berlin (Berlin Institute of Technology) and also works for BAM’s Welding Technology Division.
"The progressive trend towards composite construction in automotive bodywork and the use of new materials poses a hard test for conventional welding and forming processes. New high- and ultra-high-strength materials currently require considerable effort to be joined together. This leads in part to a significant deterioration in joint properties. In addition, forming processes are so complicated that they shorten the service life of forming tools significantly. Measures to prevent wear in these tools are therefore urgently needed", explains Prof. Hilgenberg the starting point of his work. Initial research results provide promising information. The precision pulsed laser equipment has succeeded in developing a resource-efficient process with low localisable energy input that can provide answers to the questions about joining technology from industry.
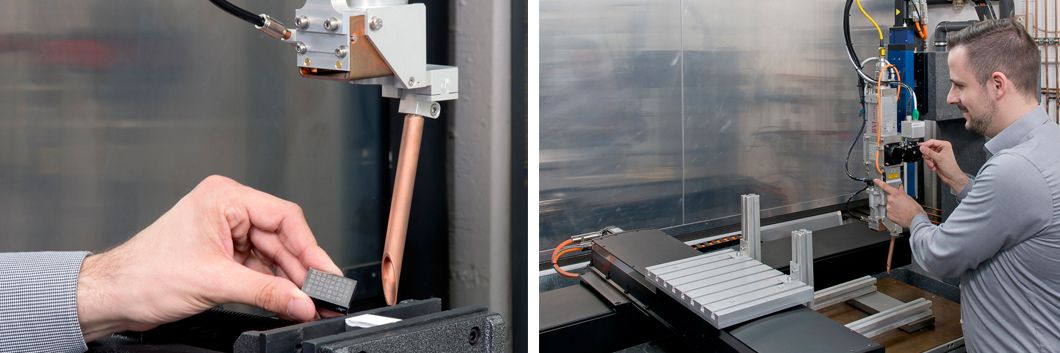
Prof. Kai Hilgenberg from the Welding Technology Division preparing a laser implantation (left) and electromagnetic influence on the weld pool during laser beam welding (right).
Source: BAM
The research is carried out in close cooperation with the Institute of Machine Tools and Factory Management of TU Berlin. The projects are a perfect example of BAM’s outstanding cooperation partnerships with renowned research institutions. In particular, the project aimed at determining the friction and wear behaviour of laser-implanted surfaces shows how BAM's internal networking contributes to outstanding research results and the development of innovative processes. "In addition to BAM’s good technical infrastructure and its staff’s broad expertise, the working group benefits above all from interdepartmental, collegial cooperation", explains Prof. Hilgenberg.
The scientists make an important contribution to the success of their colleagues. The surface structures developed in the working group are tested for their properties by tribometers from Macrotribology and Wear Protection division for example. Non-destructive testing can best detect the newly created surface and material analysis enables a deep understanding of the material. "The implementation of such a complex project is only possible through scientific cooperation at BAM," emphasises Prof. Hilgenberg.
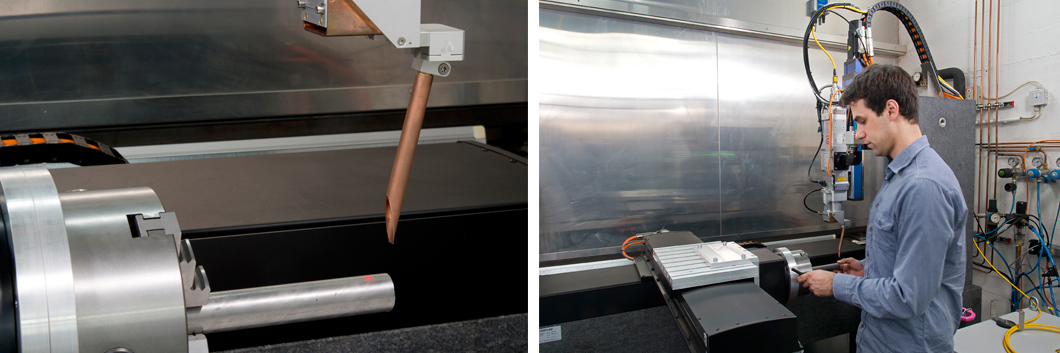
André Fritzsche, also from the Welding Technology Division, shows laser implantation on bodies of rotational symmetry.
Source: BAM
Just one example of many: pulsed lasers can precisely shape surface structures
Felix Spranger is working on his Ph.D. thesis at the Welding Technology Division and is using the equipment for his research within the project "Friction and wear behaviour of laser-implanted surfaces". In his thesis, he is researching a laser implantation process to improve heavy-duty metal forming tools, which is of particular interest to major steel manufacturers and the car industry.
For his research, Spranger uses pulsed laser radiation for the targeted melting of hard ceramic particles into metallic base materials. For this purpose, a layer of hard ceramic particles is applied to a metallic substrate. Then, Mr. Spranger uses a pulsed fibre laser to heat discrete surface points to more than 1500 °C within a few milliseconds. The metallic base material melts at this temperature while the hard ceramic particles remain intact. The particles are incorporated in the melt, which hardens after cooling and leaves a positive surface structure on the metal component. What looks like a hilly landscape under the microscope are really high-strength metal-matrix composite implants that protrude from the metal plate and are extremely hard.
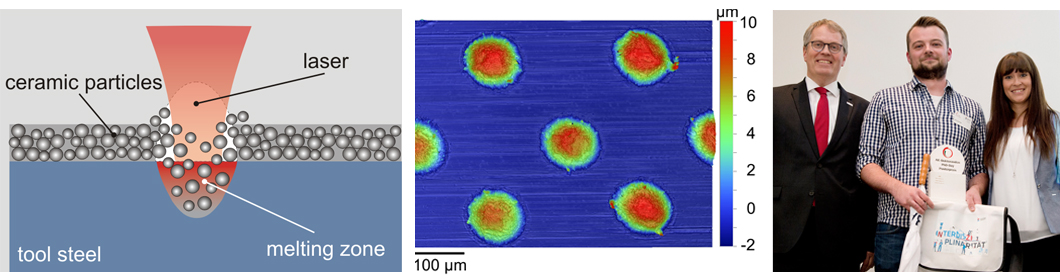
Figure 1 (left): Laser implantation; Figure 2 (middle): Resulting surface topology; Photo (right): Felix Spranger (2nd from right) received the BAM internal poster award for his project poster in autumn 2017.
Source: BAM and Welding Technology Division (Figures 1 und 2).
The first half of the three-year project is over and the theoretical basics are already well researched. Now it is time to gain further insight into implementation. Such modified tool surfaces should contribute to the development of resource-efficient and safer manufacturing processes. It is expected that targeted surface structuring can optimise friction behaviour and thus wear can be significantly reduced.
Speed counts in the free economy
BAM needs partners from the private sector to arrange for the process to be pilot tested under industrial conditions. However, the precision pulsed laser system still has to be modified for industrial use. In the current phase of research, accurate data needs to be gathered to put the research on a solid footing. As it is currently built, the precision pulsed laser system works extremely precisely, but not very quickly. "When used in the free economy, there are certain tolerance limits within which the results may vary. What matters more is speed and thus profitability", explains Prof. Hilgenberg. That the new process will find application in industry can already now be seen. "There are already inquiries from two big companies", he reveals.