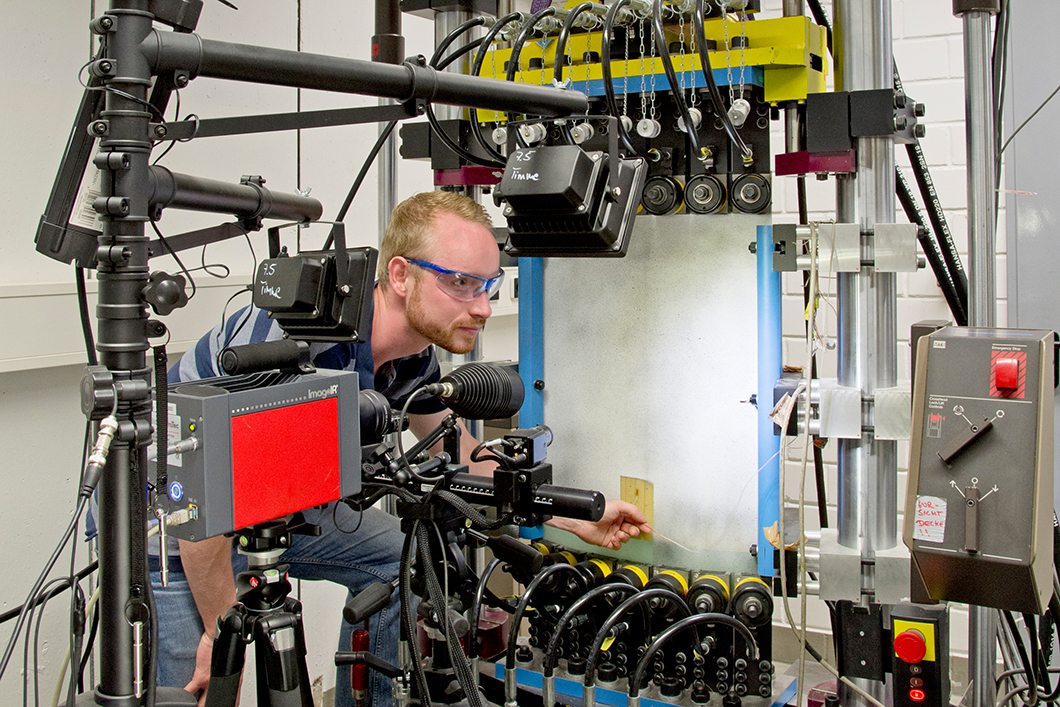
Dustin Nielow, working in the project team of Dr. Arne Kromm, at the shell test bench
Source: BAM
If damage to wind turbines occurs or safety system components fail, it triggers the highest alarm level. Design errors, incorrect assembly or natural wear of components are all possible causes. However, technical problems quite often start much earlier – sometimes as early as during production.
Modern materials are often designed just under the load limit so that even the smallest material defects can quickly lead to component failure. In addition, today's manufacturing processes often expose the materials to high stresses during the production phase. Temperature changes or different deformation behaviour of individual components are a few examples. These loads can trigger unwanted residual stresses in the material or in the manufactured components and are all potential causes for later material failure.
BAM experts are familiar with such problems. They determine material properties, search for or develop materials for specific uses and clarify material damage. Specific questions from experience are: what materials are suitable for aircraft engines? Why has a component not lasted as long as predicted? What caused a crack in a gas turbine?
In the MANUFACT project, the research team goes even one step further: they look into material imperfections created during the manufacturing process. Such imperfections can have far-reaching consequences. If, for example, cracks occur during the production of wind turbine rotor blades, they can continue unnoticed under load and ultimately lead to failure of the facility. Micro damage can lead to macro damage.
Avoid damage to wind turbines
The experts are investigating how fibre plastic composites behave under load on wind turbine rotor blades. Material failure can be particularly costly, thus there is a big need for research. Imperfections in manufacturing are sometimes unavoidable in very large parts such as rotor blades. Semi-finished products such as technical textiles or foam boards can only be produced in smaller sizes so must be joined together during the production of the huge rotor blades. Joints between lightweight components can become weak spots and eventually lead to component failure. The initial damage is sometimes only visible after 4 to 5 years, and wind turbines may even fail to reach their minimum service life of 20 years. Systematic investigations by BAM using a special test machine, the ‘shell test bench’, have clearly shown that imperfections such as thin gaps between foam pieces or simple layer overlaps introduced into shell segments led to a significant reduction in the service life of test specimens. Based on the results, BAM specialists can provide recommendations for the design of plant components and can predict their service life more reliably.
Track down dangerous hot cracks
Hot cracks, such as those that can occur during arc welding of certain materials represent dangerous imperfections in dynamically stressed components in things like power plant components or engine parts. Established non-destructive testing methods in some cases can find difficult to detect micro hot cracks. BAM experts want to find these hidden cracks and evaluate their impacts on the service life of components or equipment. In addition to the physical aspects, in the MANUFACT project, BAM experts are also investigating what ambient influences disturb the production process.
Understanding additive manufactured components
Additive manufacturing is MANUFACT’s third focus. Additive manufacturing produces three-dimensional objects based on virtual models. Various processes are available on the market. The objects are gradually created, layer-by-layer, and the quality of the objects is not always satisfactory. Many questions remain unanswered, especially in regard to microstructure properties and the strength of such components. The way in which boundary conditions in production influence the quality of the products is also not yet sufficiently well researched. Scientists want to find factors that can impair component integrity and reliability during the manufacturing process.
BAM pushes for a distinctive safety culture in Germany and for safety standards that will meet even the highest requirements in the future.
Interdisciplinary working and solving problems
In the project, diverse methods of non-destructive testing are the link for an interdisciplinary approach. Project manager Dr. Arne Kromm from the Weld Mechanics division says: "Our results so far show that it is precisely the interdisciplinary exchange between different fields of work that makes a significant contribution to increasing the understanding of individual phenomena, which is invaluable for the scientific work."