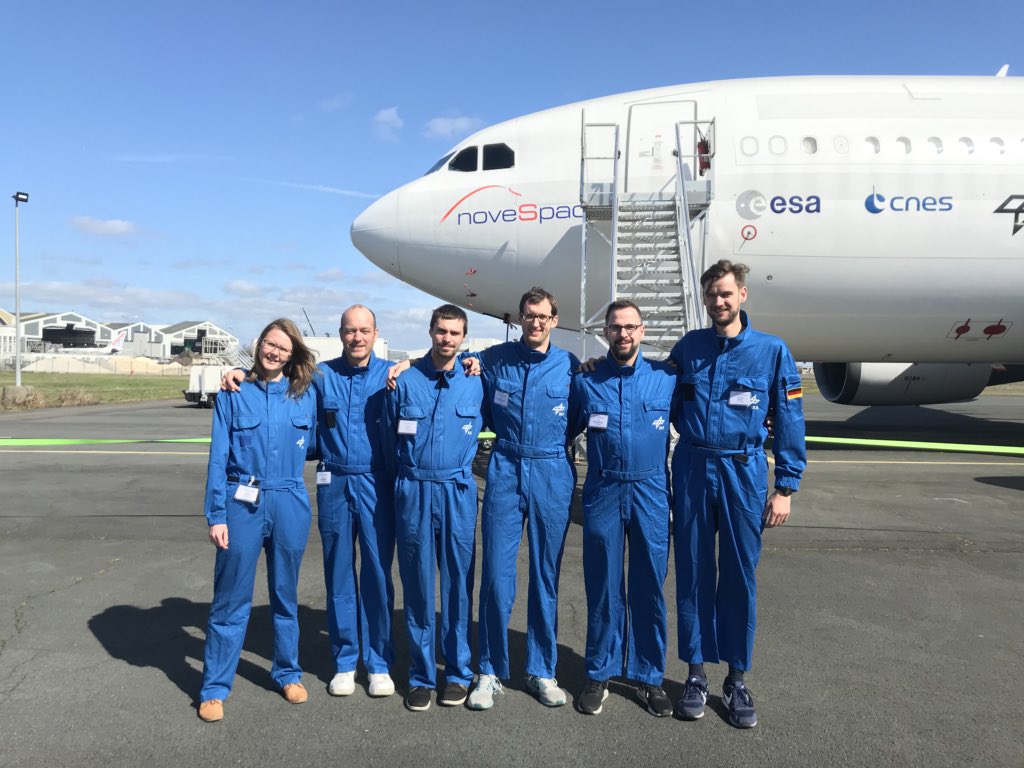
Ready for take off: The 2019 zeroG team is conducting experiments on additive manufacturing in microgravity conditions (from left to right Janka Wilbig, Prof. Dr Jens Günster, Dr Andreas Zocca, Jörg Lüchtenborg, Prof. Dr Kai Hilgenberg and Gunther Mohr)
Source: BAM, Section Corporate Communications
Research in zero gravity: a team led by Prof. Dr Jens Günster, Head of the Ceramic Processing and Biomaterials Division and Professor for high-performance ceramics at TU Clausthal is experimenting additive manufacturing in microgravity conditions. The goal is to be able to manufacture components from stainless steel, such as tools, in space. Over the last two years, the team has taken part in the DLR’s (German Space Center) parabolic flights with the project ‘Powder-based additive manufacturing in zero gravity’ in an effort to test the developed devices and methods under real conditions. The team also spent several days experimenting in zero gravity this year - together with the Welding Technology Division.
How does the powder-based method work?
Methods for additive manufacturing vary from subtractive methods such as milling, drilling and eroding in that material is brought together to form a component and is not removed. Powder-based processes are a category of former additive manufacturing processes.
During powder-based 3D printing processes, a component is built by applying layers of a free-flowing powder. In order to achieve this, a virtual 3D model of the component to be manufactured is cut into layers on a computer. Following the application of a layer of material in powder form, the geometry is then selectively transferred from the virtual 3D model into the individual layer. This is accomplished, for example, with glue or local compaction of the powder. These processes are then repeated layer by layer until the object is complete. As a final step, the component is completely encased by a powder bed. It can be easily removed from this and then cleaned.
Why is 3D printing in zero gravity topical?
This concept makes it possible to imagine manufacturing parts, components, spare parts or tools using a 3D printer in space as they are needed. Thus, only the material - the powder - would need to be transported to the space station and not a whole assortment of pieces. Additionally, nothing can be ‘sent back’ from future space missions to Mars. The ability to independently print a required piece would also provide maximum flexibility.
What are the current experiments about?
During two previous zeroG campaigns in September 2017 and March 2018, the production method Selective Laser Melting (SLM), a very successful in industry, was tested in zero gravity. Here, the focus was on the layered application of the powder. As gravity is a crucial requirement for applying thin layers of free-flowing powder, the challenge is to apply the powder layer independent of gravity. It was proven that a stream of gas through the powder could replace gravity, and the first metallic components were manufactured under zero gravity conditions.
The unit for powder application is being optimised in zero gravity within the current experiment once again. Moreover, the feasibility of coating metallic powders with a suspension is to be tested. These experiments serve as preparation for further experiments in zero gravity in space: Together with the DLR Institute for Materials Physics in Space, BAM is preparing an experiment for the autonomous 3D printing of metallic components in the "Mapheus" stratospheric rocket. There, the system will have six minutes at a time to print a part. The experiment and rocket launch are planned for summer 2020.