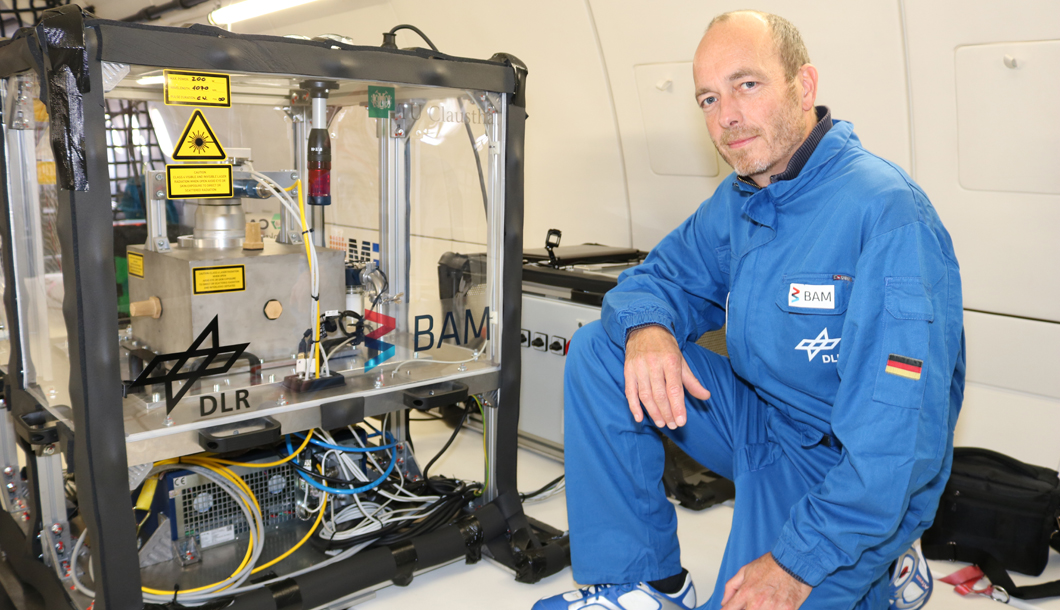
On board the Airbus 310: Prof. Jens Günster and his team conduct experiments to test powder- based additive manufacturing processes in weightlessness.
Source: BAM
BAM is currently concentrating on two main areas of research in the further development of additive manu-facturing with ceramic materials:
Processes for powder-based additive manufacturing in space
Why focus on additive manufacturing in space? Components, spare parts or tools could be manu-factured as required. Then only the material, here the powder, would have to be transported to the space station and not a whole range of parts. This is an enormous advantage for long missions with limited weight capacities and limited storage space. NASA is currently using the filament- based additive manufactur-ing process on the International Space Station (ISS), in which a filament of heated plastic is extruded layer by layer to produce a three- dimensional object.
In contrast to NASA, BAM is investigating the industri-ally very successful powder-based additive manufactur-ing processes for their suitability for use in a weightless environment. In a first Zero-G experiment, a parabolic flight in September 2017, the focus was on the layered application of the powder. Since gravity is a decisive prerequisite for the application of a thin layer of flowable powder, the challenge is to apply the powder layer independently of gravity. It has been demonstrated that a gas flow through the powder can supplant the need for gravity. In this method, the powder particles are effectively sucked into place.
In a second Zero-G experiment in spring 2018, metallic powders were applied as layers under weightlessness for the first time and fused locally into a component by means of laser radiation. The aim is to make the great potential of the laser beam melting process for the additive manufacture of ready-to-use metallic compo-nents accessible to future space missions.
Technology rollout for LSD-based 3D printing of ceramics
Layer-wise slurry deposition (LSD) uses the slurry casting technique developed for ceramic processing to produce densely-packed powder layers and powder beds for the 3D printing of ceramics. Components made of both silicate ceramics and of high-performance ceramics can be manufactured with this process.
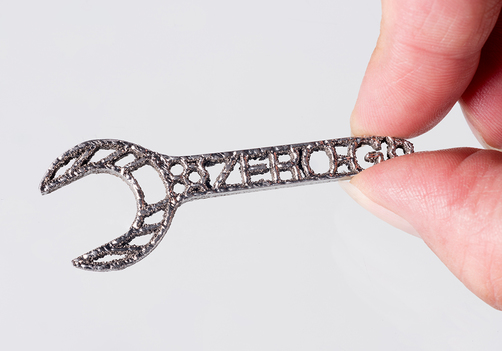
A spanner additively manufactured during the Zero G experimen
Source: BAM
Since the LSD process is superior or highly complemen-tary to other technologies already established on the market for the additive production of ceramics, the technology rollout was funded as part of the EXIST research transfer initiative of the Federal Ministry of Economics and Energy. The aim is to develop, design and test an additive production machine for the manufacture of dense ceramic parts. The parts could be individually designed porcelain parts or special parts for plant and mechanical engineering.