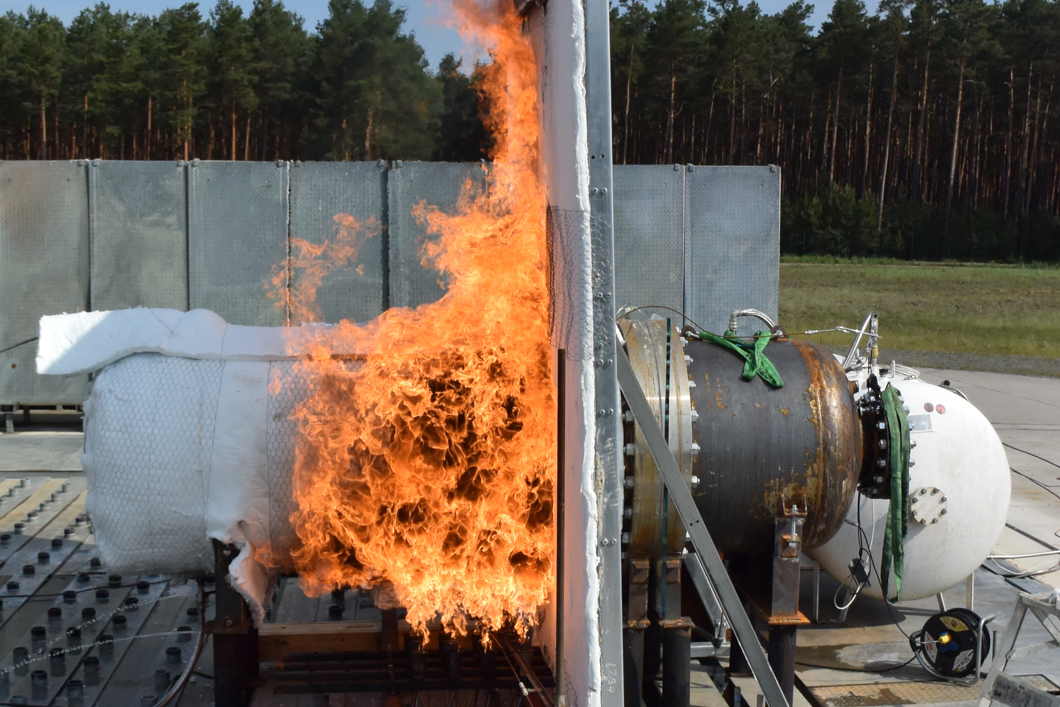
Dangerous goods container during underfiring in a test rig
Source: BAM
About 300 million tonnes of dangerous goods are transported through Germany every year, according to the Federal Statistical Office. Almost half of them are travelling by lorries. BAM’s research plays an important role in the safety of these transports. In an international project, BAM scientists are investigating the impacts on dangerous goods tanks in accidents.
“For example, we are investigating how a tank behaves under extreme loads such as when exposed to a fire,” explains Prof. Dr. Frank Otremba. He not only observes the tank’s behaviour during a fire, but also tries to predict the complex events using a three-dimensional computer model. “We want to understand what happens within the containers in such an accident and make them even safer,” says Otremba.
Universally unique test rig
BAM has developed a test rig for this purpose that is universally unique. The centrepiece is a standard pressure vessel made of steel with a diameter of one metre and 2600 litres capacity. The tank interior is divided in two: the larger section holds a liquid. Water and ethanol were used in the initial tests. Soon a tank filled with liquefied butane gas will be underfired in the test rig.
Experts refer to this as a pool fire: a liquid has spilled out in an accident and gets ignited beneath the tank. More than 100 sensors record any change in temperature and pressure in the tank during the fire. The smaller chamber contains an observation unit. A 19-millimetre thick, transparent special glass wall separates it from the rest of the pressure vessel. The scientists use cameras and laser technology to track the events inside the tank while it is being exposed to a fire from the outside. In addition, the research team can visualise liquid and steam movements using small silver-coated ceramic balls. “This is a somewhat adventurous design, but we can directly follow the thermodynamic processes and record videos and photos as well as measure flow velocity,” explains Otremba.
Large temperature differences increase the pressure in the tank
Layers of different temperatures develop in the container during underfiring. “A vapour phase develops in the dome of the tank”, explains Otremba. “And if the liquid underneath is still cold, temperature differences of several hundred degrees can occur in a comparatively small zone at the interface between liquid and steam.” These large temperature differences impose dangerous stresses on the wall of the tank that may cause it to fail at this point. An additional danger arises from rising steam temperatures in the gaseous volume. This reduces the strength of the wall material, which can ultimately lead to catastrophic container failure. For example, a non-insulated 2500-litre metal tank half filled with water can burst after seven minutes.
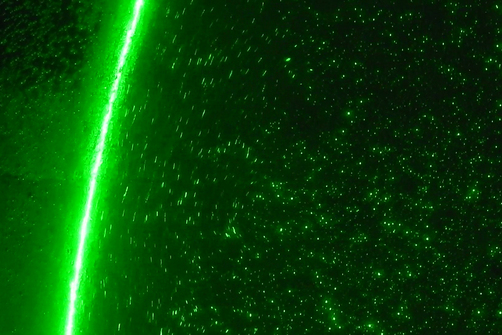
The movements of the fluid and bubbles on the wall become visible during a full engulfment test.
Source: BAM
The data from BAM’s experiments serve as the basis for the computer calculations developed by researchers in the University of Bologna (Italy) and Queen’s University of Ottawa (Canada). The international team is investigating how well the three-dimensional mathematical models reflect reality.“We can optimise the models very well,” says Otremba. “The data is then used for strength calculations for the tank’s external layer.” This allows the research team to make suggestions as to how tanks can withstand even abnormal stress better. The computer model also provides information as to how long the container can withstand a fire. This is of special interest, for example, for the fire brigade since a bursting pressure vessel poses a great danger to rescue teams.
Containers should be optimised
The more details the researchers know about the behaviour of hazardous goods containers during a fire, the better the containers can be optimised. BAM also recommends these safety measures at the international level. Of course there are computer models available for assessing tank safety. “Industry and regulatory bodies around the world are currently using simplified models for safety assessment of tanks under exceptional loads,” says Otremba. These models usually divide the tank into different zones and use average temperature and pressure distribution values in their calculations. This simplified approach has been proved effective in practice but at the same time it requires very high safety margins in risk assessments. “We are very optimistic that our investigations, combined with accompanying numerical analyses, will help to reduce such additional safety margins without compromising the safety of the containers,” says Otremba. This can make the manufacturing of dangerous goods tanks more cost-efficient.