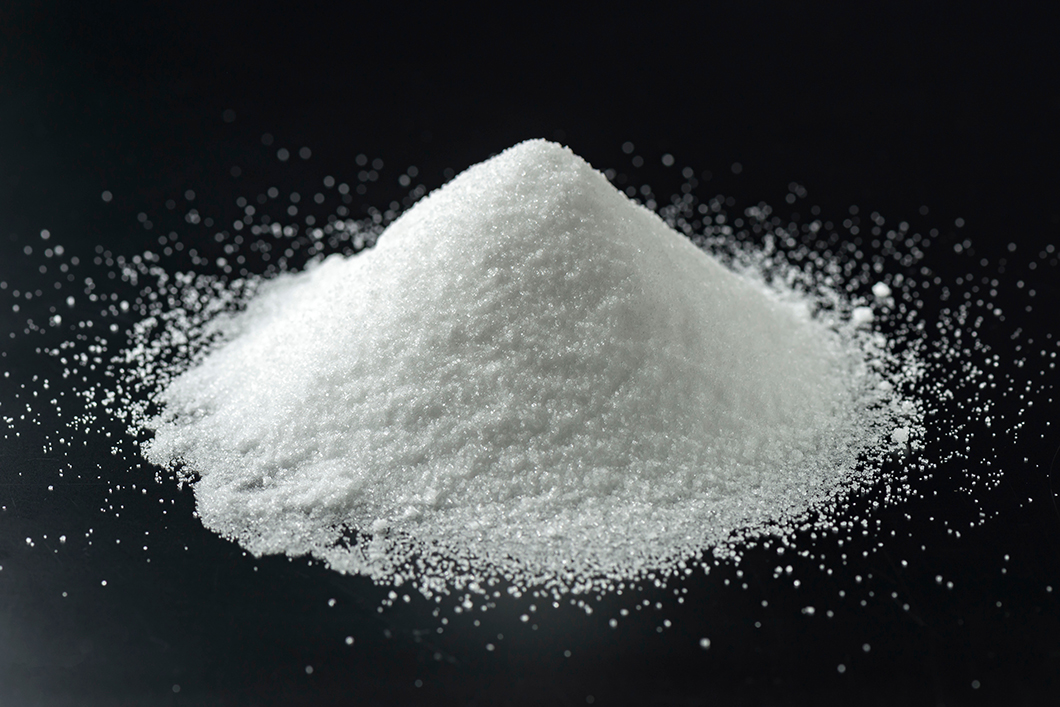
BAM scientists are looking for alternatives to lithium batteries. Sodium-ion batteries are considered promising. The advantage of sodium is that it is available everywhere.
Source: Adobe Stock / Kei Utsuki
Electrical energy storage systems are indispensable for the energy transition: They power electric vehicles, serve for stationary intermediate storage of electricity from wind turbines or solar plants and are used for many industrial applications. So far, corresponding batteries have been based almost exclusively on lithium-ion technology. However, lithium has serious disadvantages: The global reserves of the lightweight alkali metal are limited, its mining is expensive and not very environmentally friendly. In addition, the electrodes of lithium-ion batteries currently require cobalt and nickel, metals that are either mined under problematic conditions or are highly toxic.
Promising “drop-in technology”
Researchers worldwide are therefore looking for environmentally friendly alternatives to lithium. Sodium-ion batteries are considered particularly promising. They would be a “drop-in technology”, i.e. they can be quickly transferred to standard battery production. They also require neither cobalt nor nickel. And: sodium is easily available as a natural component of rock salt. However, the weak point of sodium-ion batteries so far has been the material of the “positive pole”, somewhat simplified called the “anode” of a battery. It is the fuel of an electric battery. When charged, the anode material should be able to store as many positive sodium ions as possible. Thus, it is decisive for the efficiency of the battery.
"If we are successful with our concept, it will provide a big innovation boost for the sodium-ion technology."
Customised composite materials as ion storage materials
Instead of graphite – as in the case of the somewhat smaller lithium ions – so-called hard carbons have so far been used for this purpose in sodium-ion batteries. The disadvantage: not only sodium ions can be stored in the pores and channels of the carbon. Electrolyte, an ion-conducting liquid inside the battery cell, also gets in. This leads to losses in storage capacity and impairs efficiency.
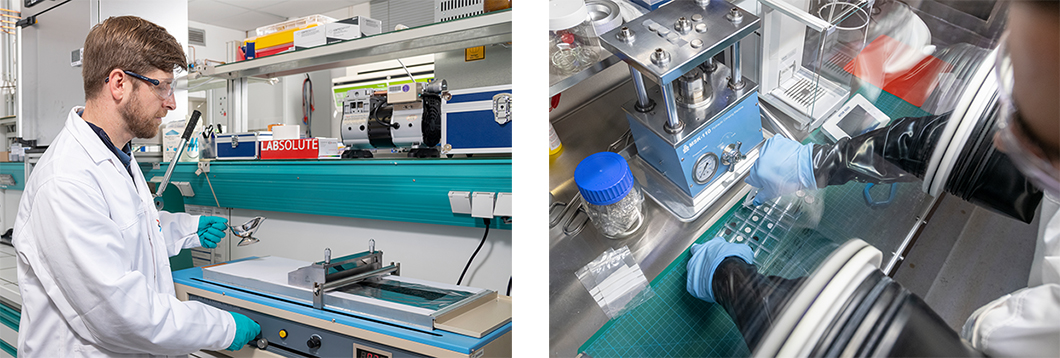
For the anode of a battery cell, Tim Fellinger coats a thin aluminium foil with carbon paste (left). Button cell batteries are assembled in a glovebox (right).
Source: BAM
In a cooperative project, BAM is researching alternative anode materials to compensate for this disadvantage and decisively advance the sodium ion technology. The project is based at BAM’s battery test centre. “It is very complex to find the ideal structure for these novel materials,” explains Tim-Patrick Fellinger, principal investigator of the collaborative project and an expert in energy materials. “We want to develop tailor-made composite materials that offer space for as many sodium ions as possible, but keep out interfering electrolytes. The challenge is to find a material that is both safe and efficient.”
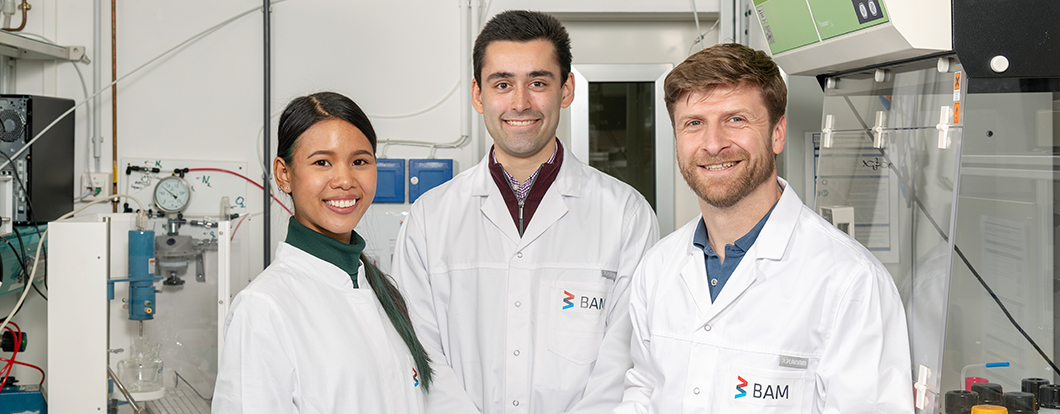
Juthaporn Wutthiprom, Alexander Appel and Tim-Patrick Fellinger (from left to right)
Source: BAM
For this purpose, Fellinger’s team is cooperating closely with the Helmholtz-Zentrum Berlin, the Technische Universität Berlin and several companies that specialise in carbon materials for batteries. “The rapid exchange of knowledge with industry is particularly important to us,” says Fellinger. “If we are successful with our concept, it would mean a big innovation boost for sodium-ion technology as a whole.”
Find more information in DialySorb - Carbons as anodes in sodium-ion batteries