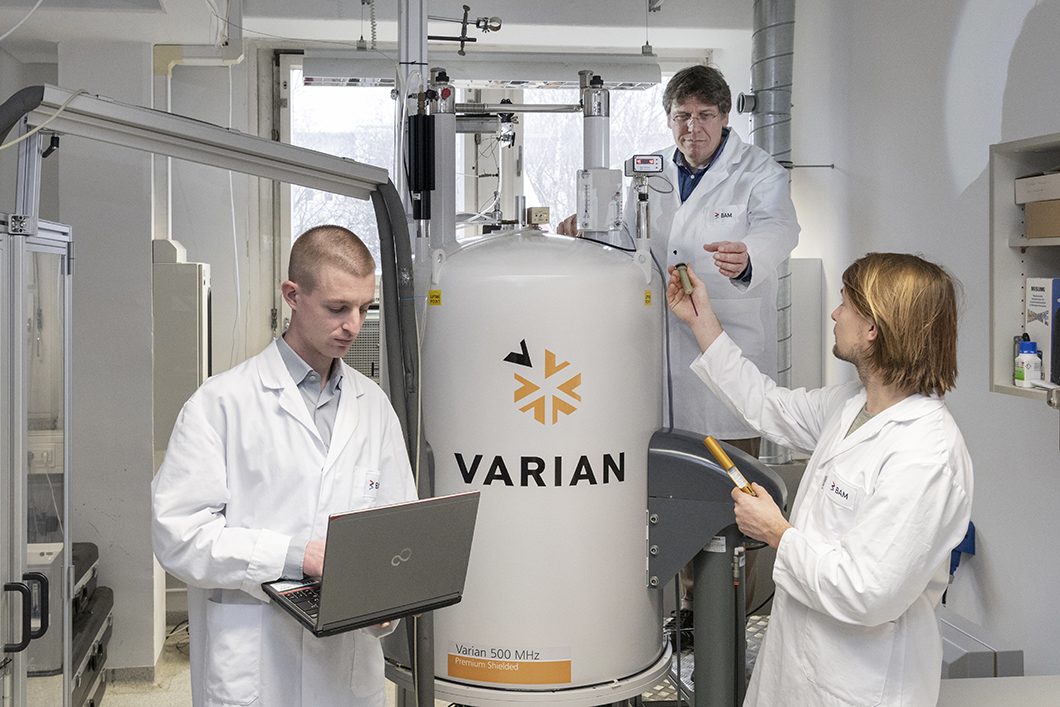
Research on new production facilities for which there is little experience to date: Dr Klas Meyer, Dr Michael Maiwald and Martin Bornemann-Pfeiffer (from left to right) from the Process Analytics department want to put the safety of processes and plants through their paces.
Source: BAM
The chemical process industry delivers substances for all types of products – car seats, clothing materials, medicines, varnishes, paints and much more. Until now these substances were produced in fixed assembled production facilities. Scientists at the Bundesanstalt für Materialforschung und – prüfung (BAM) are conducting research on a new smart production module that will be able to quickly and flexibly produce chemically custom-built products.
To ensure the leading international position of the German process industry, companies must digitise their production processes. For this purpose, new methods, processes, sensors and automation technologies are in demand.
Individual companies are in fact already testing the application of modular production. “In the future, standard components will be able to be combined into optimal production units for the production of smaller quantities of speciality chemicals or pharmaceutical raw materials,” says Martin Bornemann-Pfeiffer from the Process Analytical Technology division at BAM. Individual process steps are designed as standardised modules, which allows for greater flexibility in the facilities. “Production quantity can be adjusted to current demand by switching modules on or off, and new production processes are established faster.”
3D Printed Mixer made from Ceramics
For one of these modules, BAM scientists, with the help of a special simulation process, first modelled a mixer for chemical reactions from ceramics on the computer and then printed it out in 3D. Fitted with “skilfully interlaced tablets”, as Bornemann-Pfeiffer explains, the mixer homogenises the initial products so that at the end a product of the best quality is produced.
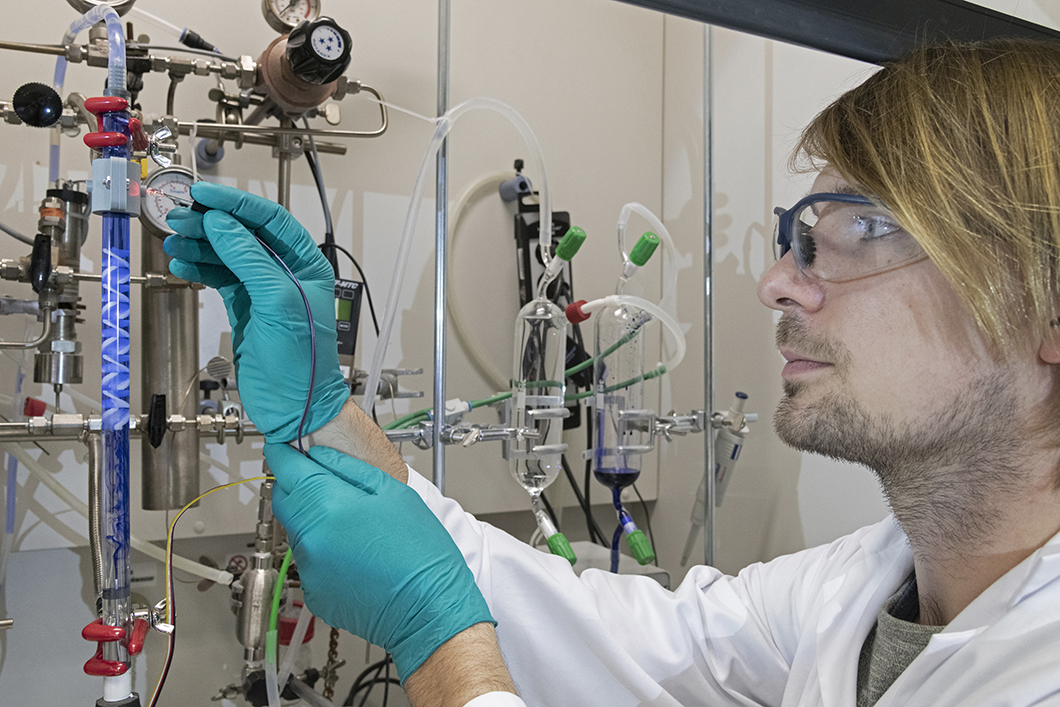
Martin Bornemann-Pfeiffer shows a model for illustration: the team has modelled a mixer for chemical reactions from ceramics on the computer and then printed it out in 3D.
Source: BAM
Virtual Representation of a Chemical Reaction
The special thing/feature: with a diameter of only five millimetres, the mixer fits into a nuclear resonance spectrometer (NMR spectrometer). Chemical reactions can therefore be precisely and reliably analysed in real time. “This is to help us understand the process better,” says the process technician, “and they can optimise it if necessary.” At the same time, scientists use flow simulation to measure whether the mixing process runs smoothly. They model the time sequence of the reaction. From the simulation data and the NMR analysis, they develop a digital twin of the entire reaction system on the computer. This digital twin virtually represents the mixer and NMR including all the processes – based on mathematical models.
More safety through online quality control
“With the twin, we can control whether the NMR measurements correspond with the models and we can search for problems in the system,” emphasises Dr. Klas Meyer, also from BAM’s Process Analytical Technology division. For example, whether something has gotten into the mixer. At the same time, the models are improved by continuously measured values over time. This in turn results in optimisations for the development of the real model. We also speak of “cyber physical production system”. This reduces development times for new products enormously.
“These are completely new production facilities which we have had little experience with to date,” says Dr. Michael Maiwald, head of the Process Analytical Technology division. “At BAM, we have the expertise to put the safety of such processes and facilities through its paces.” This competence is significant for the chemical industry to open up to new technologies.