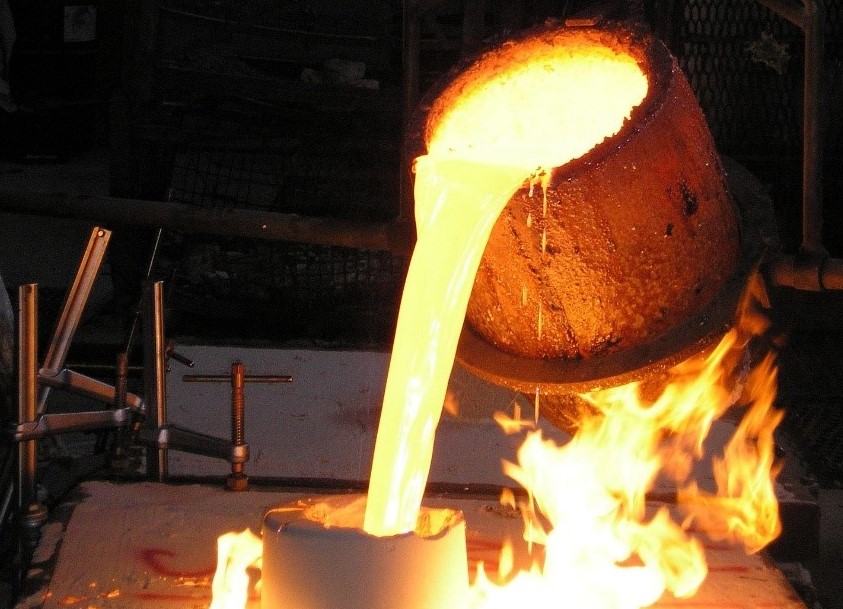
Source: pixabay.com
Project period
01/01/2022 - 30/06/2026
Project type
Collaborative research project
Project status
Ongoing
Description
Development of a neural network-based method for non-destructive testing by means of laser thermography (Thermographic Testing) of castings with a rough surface for near-surface imperfections as an alternative to magnetic particle and penetrant testing.
Location
Bundesanstalt für Materialforschung und -prüfung (BAM)
Richard-Willstätter-Straße 11
12489 Berlin
Cylinder crankcase Source: BAM
Source: BAM
The project aims to create a laser thermography-based NDT method for high-sensitivity detection of near-surface defects in cast components. Using neural networks, it will address surface influences to improve accuracy and reliability, while boosting testing speed for in-line inspections. Validation against established NDT techniques like magnetic particle and radiographic testing will ensure effectiveness. Guidelines, reference specimens, and manuals will also be developed to aid SMEs in adopting the technology.
Source: BAM
Source: BAM
Partners: Forschungsvereinigung Gießereitechnik e.V. (FVG)
Funding: Federal Government - Federal Ministry for Economic Affairs and Energy (BMWi) - Industrial Collective Research (IGF)
This research project focuses on advancing laser thermography, an innovative non-destructive testing (NDT) method, to detect near-surface imperfections in cast products with rough and complex geometries. The primary aim is to provide an alternative to magnetic particle and penetrant testing, which are limited in detecting hidden or closed defects. By integrating neural networks and refining the testing methodology, the project seeks to address the specific challenges faced by SMEs in the foundry industry. Additionally, the proposed multispectral inspection approach assists in the emissivity estimation using an integrating sphere, which helps in the correction of emissivity fluctuations across objects with non-uniform surfaces.
This work will enable the automation, reliability, and speed necessary for in-line quality control, contributing to the production of safer and higher-quality cast components. The outcomes of this research will provide SMEs in the casting industry with an advanced, cost-effective NDT method for quality control. By enabling fast, automated detection of near-surface imperfections, laser thermography will reduce reject rates, lower complaint costs, and improve competitiveness. Additionally, the methodology will support the development of lightweight, safety-critical components with complex geometries, aligning with modern market demands.
Project coordination
Dr.-Ing. Julien Lecompagnon, Bundesanstalt für Materialforschung und -prüfung (BAM)
Partners
Forschungsvereinigung Gießereitechnik e.V. (FVG)
Funding
Federal Government - Federal Ministry for Economic Affairs and Climate Action (BMWK) - Industrial Collective Research (IGF)