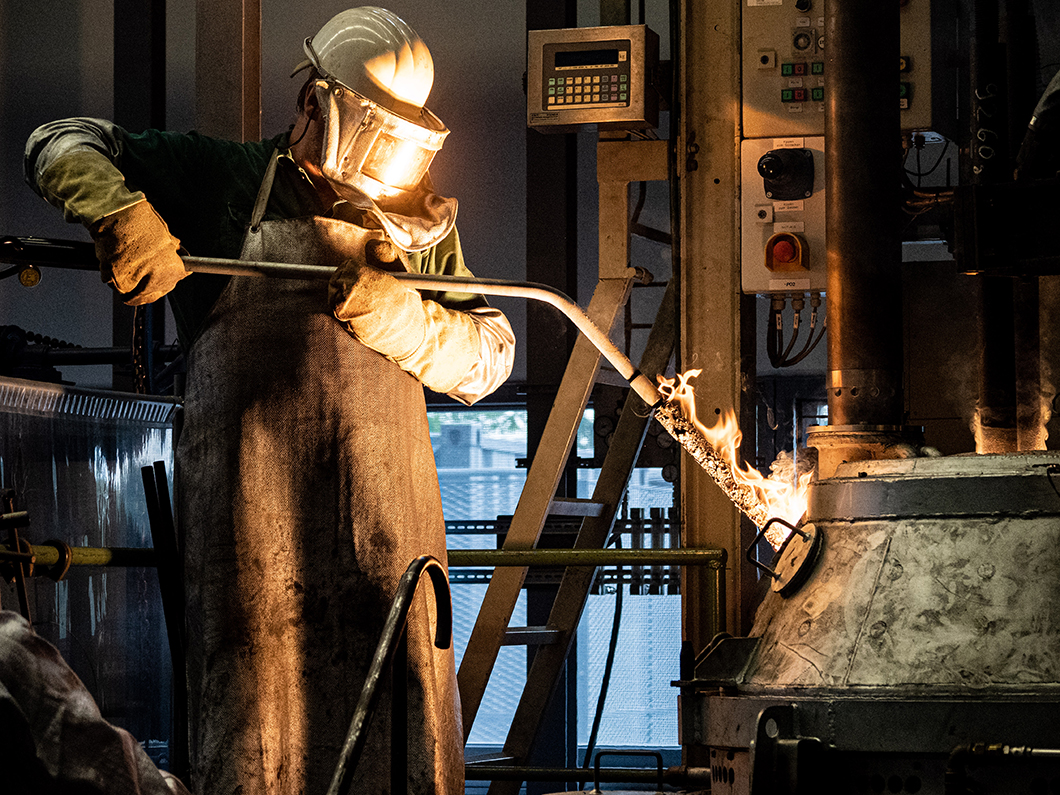
Temperature measurement at BAM's small-scale arc furnace
Source: BAM, Thermochemical Residues Treatment and Resource Recovery division
Project period
01/02/2021 - 31/01/2024
Project type
Collaborative research project
Project status
Closed
Description
Steelmaking slags are by-products of crude steel production that contain a mass fraction of up to 30% iron. The SlagCEM project is investigating the recovery of this iron with concurrent production of a hydraulic binder.
Location
Bundesanstalt für Materialforschung und -prüfung (BAM)
Richard-Willstätter-Straße 11
12489 Berlin
Sampling at the small-scale electric arc furnace Source: BAM, Thermochemical Residues Treatment
Source: BAM
SlagCEM aims to recycle steelmaking slag as completely as possible. The iron is to be recovered and the mineral material is to be made usable as a hydraulic binder. The process thus contributes to saving primary raw materials and reducing greenhouse gas emissions in the cement industry.
Source: BAM
Source: BAM
Project coordination
Bundesanstalt für Materialforschung und -prüfung (BAM)
Thermochemical Residues Treatment and Resource Recovery division
Partners
ArcelorMittal Eisenhüttenstadt
Technische Universität Berlin
Deutsches Zentrum für Luft- und Raumfahrt e.V.
FEhS - Institut für Baustoff-Forschung e.V.
thyssenkrupp Industrial Solutions
Öko-Institut e.V.
LTB Lasertechnik Berlin
Steelmaking slags - a by-product with potential
German crude steel production generates over 5 million tons of steelmaking slag per year. This by-product still contains a mass fraction of up to 30% iron oxide, which is lost for further use in the current common use of the slags in road construction.
The SlagCEM project is investigating the recovery of crude iron from steelmaking slags. By separating the iron from the slag, its chemical and mineralogical composition is closely matched to that of the Portland cement clinker. This makes it possible to produce a hydraulic binder for the cement industry in the same process.
Implementation of the high-temperature process
In a high-temperature process, the largely oxide-bound iron can be recovered by reducing it to metallic iron in the molten slag at ~1800 °C. These temperatures are uneconomical in a large-scale process and problematic with regard to the refractory material.
In SlagCEM, the process is to be adapted in such a way that large-scale implementation is feasible under economic conditions. To this end, the composition of the slag is to be modified in order to bring the viscosity into a technically suitable range and to enable iron recovery at lower temperatures. The goal is to perform the reduction on liquid steelmaking slags directly in the steel mill at ~1600 °C. At the same time, a mineral product with good cementitious properties is to be produced.
Project team consisting of research institutes, steel and cement industry
With expertise from research institutes, the steel and the cement industry, a technically, logistically and economically manageable process is to be developed that will generate marketable products. To this end, the Bundesanstalt für Materialforschung und -prüfung (BAM), the Technical University of Berlin (TUB), the German Aerospace Center (DLR) and the FEhS - Institut für Baustoff-Forschung are investigating the effects of a chemical modification on the melting behavior of steelmaking slags from ArcelorMittal Eisenhüttenstadt and on the cementitious properties of the binder produced. By means of online LIBS (Laser Induced Breakdown Spectroscopy) from LTB Lasertechnik Berlin, it will be possible to analyze occurring changes already during the experiments. The collaborating partners CEMEX Deutschland AG and Spenner GmbH & Co. KG evaluate the performance of the product as a binder.
Based on the project results, ArcelorMittal will plan a large-scale demonstrator with which the process can be tested and integrated in a steel mill. A final assessment of the ecological impact of the process, for both the steel and cement industries, will be made possible by a life cycle assessment (LCA) of the entire recycling process prepared by Öko-Institut e.V.
Project coordination
Bundesanstalt für Materialforschung und -prüfung (BAM)
Partners
Bundesanstalt für Materialforschung und -prüfung (BAM)
Thermochemical Residues Treatment and Resource Recovery division
ArcelorMittal Eisenhüttenstadt
TUB Technische Universität Berlin
DLR Deutsches Zentrum für Luft- und Raumfahrt e.V.
FEhS Institut für Baustoff-Forschung e.V.
thyssenkrupp Industrial Solutions
Öko-Institut e.V.
LTB Lasertechnik Berlin
Funding
The SlagCEM project is funded by the German Federal Ministry of Education and Research (BMBF) under the funding guideline „Resource-efficient circular economy - Building and mineral cycles (ReMin)“, which is part of the FONA framework program.