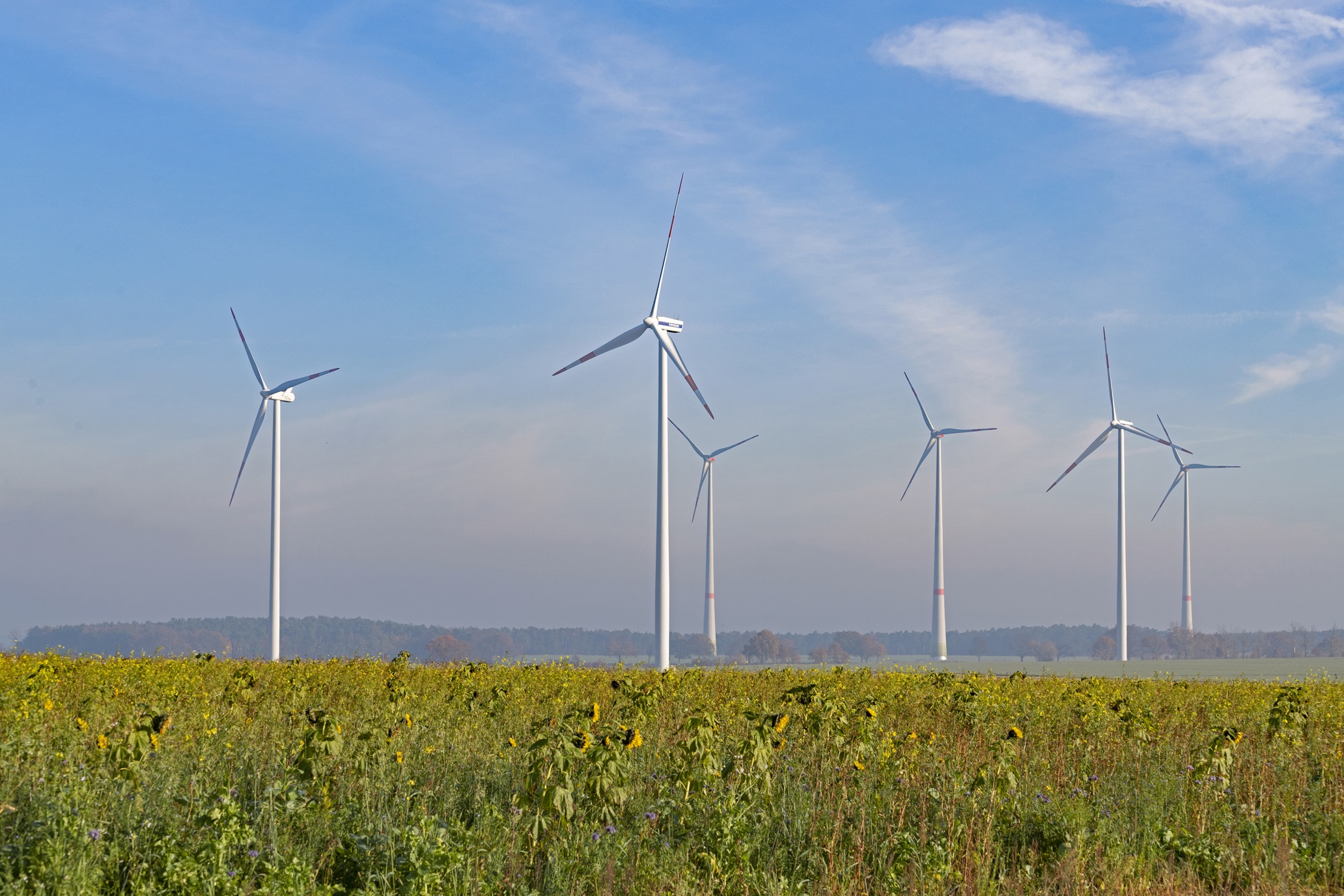
Source: BAM
Project period
01/01/2024 - 31/12/2028
Project type
Collaborative research project
Project status
Ongoing
Description
ReliaBlade2 enhances the reliability of wind turbine rotor blades through advanced thermographic monitoring and analysis of material fatigue and structural damage. This process not only improves the durability of the blades but also reduces the operating costs of wind turbines.
Location
Bundesanstalt für Materialforschung und -prüfung (BAM)
Richard-Willstätter-Straße 11
12489 Berlin
Source: BAM
The structural integrity of rotor blades for wind turbines is one of the biggest challenges facing the wind industry. As part of ReliaBlade2, modern and efficient test procedures are being developed to certify new rotor blade designs. In addition to the actual structural tests, accompanying measurements are carried out using modern inspection methods. In this way, better forecasting tools can be developed to help predict damage in rotor blades during operation.
Source: BAM
Source: BAM
In ReliaBlade2, thermographic measurements are carried out in fatigue tests on laboratory samples and two 70+ m rotor blades. Material parameters and fatigue behavior are examined in the laboratory tests. The cyclic blade tests are accompanied by thermographic measurements to characterize structural properties and incipient damage. The findings are used to improve the design of the rotor blades.
Source: BAM
Partners:
- Fraunhofer IWES (Coordinator)
- Nordex Energy SE & Co. KG
- WRD Wobben Research and Development GmbH
- TPI Composites Germany GmbH
- Leibniz Universität Hannover
Associated partners:
- RE Technologies GmbH
Funding:
- Bundesministerium für Wirtschaft und Klimaschutz (BMWK)
- Projektträger Jülich (PtJ)
ReliaBlade2: New technologies for the rotor blades of tomorrow
Wind turbine blades are crucial components of a wind turbine, as they significantly influence its efficiency, longevity and overall performance. The ReliaBlade2 project is focussing on extending the service life of rotor blades and thus reducing electricity costs.
Industrial partners (Nordex, TPI Composites, Enercon) and research institutes (BAM, Fraunhofer IWES, Leibniz Universität Hannover) are working together in ReliaBlade2. For the first time, design parameters are being exchanged between manufacturers and testing laboratories to adapt the cyclic fatigue tests of the rotor blades to the rotor blade design.
BAM's role in ReliaBlade2
BAM's division Thermographic Methods has extensive experience in active and passive thermography of rotor blades. Measurements on entire rotor blades in the field and their components under real conditions present particular challenges. BAM's contributions are focussed on:
- fatigue tests on material components: BAM develops and validates thermographic tests of specimens made of glass fibre reinforced plastic in cyclic fatigue tests. This includes the definition of standard test specimens, the thermographic inspection of material fatigue during fatigue tests and the comparison of thermography with other testing techniques. The aim is to develop a meaningful damage model in order to improve strength predictions.
- inspection and structural monitoring of entire rotor blades: Cyclic and static fatigue tests of entire rotor blades are used in the development and certification of rotor blades. The knowledge gained from such tests can be used to develop damage predictions for rotor blades in the test and also in the field. BAM's aim is to incorporate thermography into these forecasts and recognise damage at an early stage. In this way, the design of future rotor blades can be improved on the basis of these findings.
Thermography in rotor blade testing
Thermography can visualise internal damage to structures such as rotor blades or laboratory samples. The more a component - or a region within a component - is subjected to load during cyclic testing, the warmer it becomes. This phenomenon occurs even before any damage occurs in the component and allows critical structural areas to be detected thermographically. In addition, thermography allows the so-called "thermoelastic effect" to be used to directly visualise cyclic stress in the component. The resulting "thermoelastic stress analysis" takes place contactless and continuously in the cyclic fatigue test.
As material fatigue increases, damage to the material becomes more and more likely. If damage eventually occurs, this leads to friction and the component heats up locally.
Thermography can therefore detect the onset and development of damage at an early stage and with spatial resolution. This is crucial for predicting fatigue and failure. Existing models for damage development in entire rotor blades can thus be verified experimentally.
As part of ReliaBlade2, BAM will validate the applicability of thermography in fatigue tests and contribute to the development of new test standards and methods. This will contribute to improving the stability of rotor blades and strengthening the competitiveness of the European wind energy market.
Partners
- Fraunhofer IWES (Coordinator)
- Nordex Energy SE & Co. KG (in German)
- WRD Wobben Research and Development GmbH
- TPI Composites Germany GmbH
- Leibniz Universität Hannover
Associated partners
Funding
Federal Ministry for Economic Affairs and Climate Action
Projektträger Jülich (PtJ)