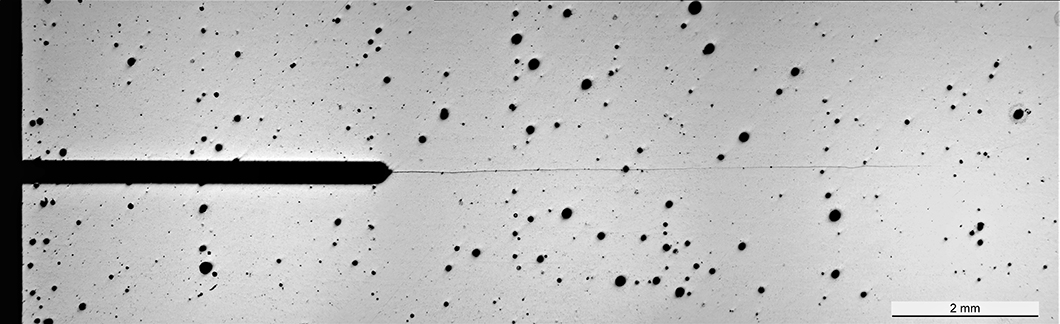
Crack growth in a notched specimen (SENB) made of L-PBF AlSi10Mg.
Source: BAM, division Weld Mechanics in collaboration with division Welding Technology
Project period
01/02/2020 - 31/01/2023
Project type
BAM project
Project status
Closed
Description
Additive manufacturing: The Laser Powder Bed Fusion (L-PBF) technique is particularly interesting for lightweight alloys as it offers advantages over the well-established casting processes. RESIFT aims at identifying the best heat treatment to optimise the fatigue life of an L-PBF AlSi10Mg alloy.
Location
Bundesanstalt für Materialforschung und -prüfung (BAM)
Unter den Eichen 87
12205 Berlin
Source: BAM
Additive manufacturing (AM) techniques are commonly used for the production of AlSi10Mg aluminium alloys. Its typical applications are found in the aerospace and automotive industries due to the high corrosion resistance, low density and high mechanical strength of the final components. AM components require less postprocessing than the cast counterparts, however heat treatments can be crucial to guarantee an adequate fatigue resistance and reduce residual stress. Even though a lot of research has been generated for certain L-PBF materials, the effect of stress relief remains mainly unexplored in L-PBF AlSi10Mg materials.
Source: BAM
Post-process heat treatments are generally performed to additive manufactured components before placing them in service, to relieve detrimental residual stresses and increase the ductility, at the cost of reducing strength.
The project aims at identifying the best heat treatment to optimise the fatigue life of a Laser Powder Bed Fusion (L-PBF) AlSi10Mg alloy. To this purpose, various heat treatments in the range of temperatures between 265°C and 300°C are performed and studied.
Source: BAM
Source: BAM
Partners
Bundesanstalt für Materialforschung und -prüfung (BAM)
Division Weld Mechanics
Division Micro Non-Destructive Testing
The material for the project was kindly provided by Deutsches Zentrum für Luft- und Raumfahrt (DLR)
RESIFT - Investigation of residual stress and microstructure effects on the fatigue behaviour of an L-PBF AlSi10Mg alloy
Additive manufacturing (AM) technology is reaching a well-established position in the production of high-performance components. Nevertheless, as the application of the technique to metallic materials is still relatively new and considering the complexity of the topic, further investigations are required.
Among the AM techniques, Laser Powder Bed Fusion (L-PBF) processes allow the building of metallic components layer-by-layer, reducing the post-processing needed and the consequent waste of material. A near net-shape complex-shaped component can be produced, minimizing the waste of raw material as well as the use of expensive subtractive tooling. The L-PBF technique is particularly interesting for lightweight alloys as it offers advantages over the well-established casting processes.
Aluminium silicon alloys are typically used in the production of high-performance and lightweight components for many applications in the aerospace, automotive, military, and biomedical field.
Post-process heat treatments are generally performed to a component before placing it in service, to relieve detrimental residual stresses and increase the ductility. The project aims at identifying the best heat treatment to optimise the fatigue life of an L-PBF AlSi10Mg alloy. To this purpose, various heat treatments in the range of temperatures between 265°C and 300°C are performed and studied. Under different heat treatment conditions, the evolution of microstructure and residual stress state is investigated to understand how the modifications impact the fatigue life.
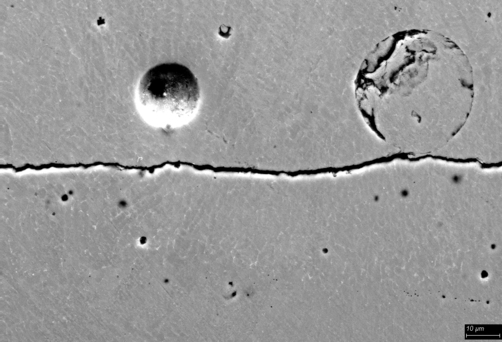
A crack propagating through the peculiar as built microstructure of a L-PBF aluminium sample. Nanometric silicon networks (in white) are embedded in the aluminium matrix (in grey). The spherical keyhole pores are formed during the process, when excess energy is imparted by the laser to the molten powder
Source: BAM, division Weld Mechanics and division Materialography, Fractography and Ageing of Engineered Materials
Reduce residual stresses
As-built L-PBF AlSi10Mg possesses increased mechanical properties when compared to conventionally produced materials due to the formation of finer nano-silicon networks and smaller grains. These microstructural features result from localized rapid cooling rates occurring during the process. The high thermal gradients occurring during the process also induce the build-up of high residual stress. Residual stresses can be detrimental or beneficial for the fatigue life of a component depending on their sign (i.e. tensile or compressive). To avoid unexpected failures as a result of unaccounted detrimental residual stress, post-process heat treatments are necessary.
Project coordination
Bundesanstalt für Materialforschung und -prüfung (BAM)
Division Weld Mechanics
Division Micro Non-Destructive Testing
Project partner
The material for the project was kindly provided by Deutsches Zentrum für Luft- und Raumfahrt (DLR)
Funding
The RESIFT project is supported by internal BAM funding.