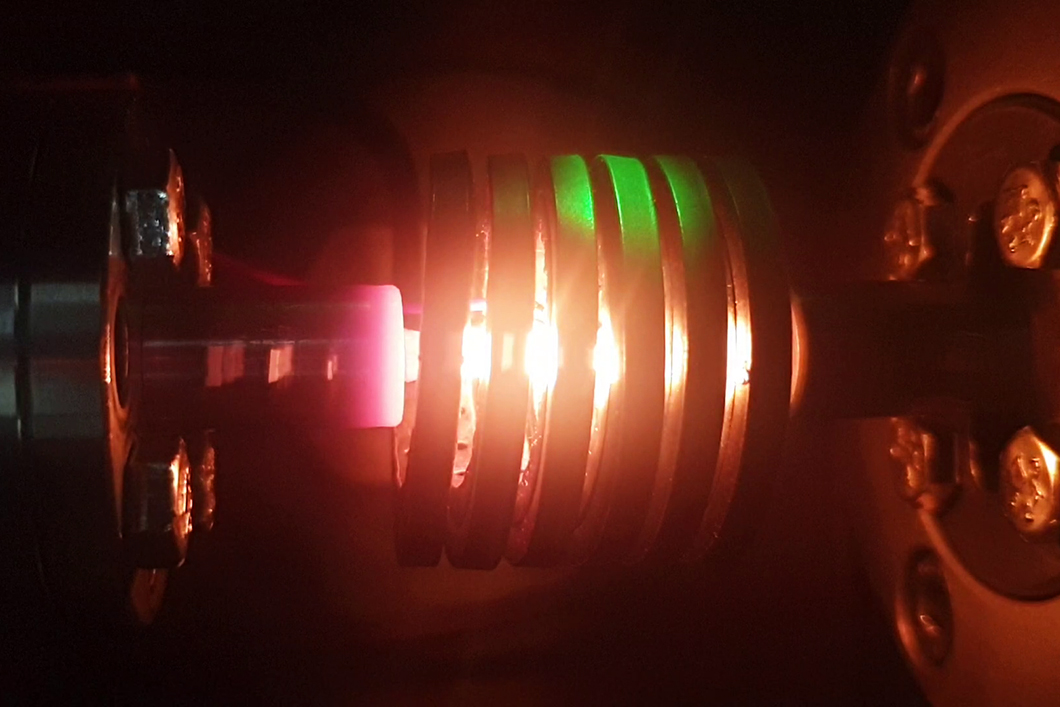
Thermal simulation of the heat-affected zone of a submerged arc welded joint in the induction coil of the quench dilatometer
Source: BAM, department Component Safety
Project period
01/05/2021 - 31/10/2022
Project type
Collaborative research project
Project status
Closed
Description
The project investigates the influence of the welding metallurgy of modern, high-strength steels on the hydrogen-assisted cold cracking susceptibility of offshore components in interaction with the increased stiffness of submerged arc thick plate welds.
Location
Bundesanstalt für Materialforschung und -prüfung (BAM)
Unter den Eichen 87
12205 Berlin
UP welding head, thick sheets, welded seam Source: BAM, department Component Safety
High-strength submerged arc welded (SAW) steel heavy plates are used for foundation structures of offshore wind turbines. One challenge is the high structural shrinkage restraint of the welds with additional mechanical stress. Another challenge is the different composition of the base and filler materials with influence on the mechanical properties and hydrogen diffusion in the weld. In a critical combination, hydrogen-assisted cold cracking can occur.
Source: BAM
The objective is to enable cold-crack-free welding processing of high-strength and shrinkage-restricted welding joints of heavy plates with different compositions during multi-wire submerged-arc welding (SAW). The interaction of microstructure, hydrogen diffusion, and high residual stresses of high-strength submerged-arc welded heavy plates has not been investigated to date. Systematic separation and evaluation of the interaction of these three factors is necessary to evaluate delayed the hydrogen-assisted cold cracking (HACC) susceptibility.
Source: BAM
Samples are extracted from weld specimens under free-shrinkage condition. The microstructure- and alloy-specific hydrogen transport behaviour is investigated (by electrochemical charging and carrier gas hot extraction). The reproduction of the real, strongly increased multiaxial stress state of the SAW joints of heavy plates succeed by means of restraint welding tests with component-like stiffness and locally hindered weld joint shrinkage
Source: BAM
Project coordination
Bundesanstalt für Materialforschung und -prüfung (BAM)
Partner
Forschungsvereinigung Stahlanwendung (Fosta) e.V.
Funding
AiF within the framework of the program for the promotion of joint industrial research (IGF), Federal Ministry of Economics and Climate Action
PhoSten - Prevention of cold cracking in thick plate welds of high-strength steels
Initial situation and motivation
The central challenge for the future is climate neutrality and the provision of green energy in Germany. In particular, offshore wind power is of highest importance, especially against the background of the additional aim of generating hydrogen by electrolysis. In addition, the size of wind turbines will continue to increase in the future and, hence, the need for more stable foundation and tower structures. For the foundation structures in offshore wind farms, mainly thick-walled steel heavy plates are used, for example for monopiles. Here, wall thicknesses of up to 200 mm are achieved e.g., for ring segments, which are processed by submerged-arc welding (SAW) multi-wire technology. Materials currently used with yield strength of up to 355 MPa are increasingly reaching their limits here. The use of higher-strength materials, such as S690, offers several advantages:
- significant weight savings due to the possible wall thickness reduction
- more efficient material utilization
- lower welding processing costs due to the smaller seam cross sections to be filled.
In general, SAW can be expected to introduce high hydrogen concentrations in the welding seam. The high stiffness of the thick plates and the resulting locally increased shrinkage restraint of the welding seam cause greatly increased multi-axial residual stress states. The critical interaction of these factors may lead to delayed hydrogen-assisted cold cracking (HACC). In this context, the alloying concept of the steel heavy plates used significantly influences the delayed HACC. For example, the hydrogen diffusion changes as a consequence of the different thermal stability of the Ti, N or V-containing precipitates and via grain growth in the heat-affected zone (HAZ) of the weld. Both topics alter the so-called hydrogen trapping behaviour in the material. Hence, the extent of the time delay is directly dependent on the chemical composition and the welding parameters. In addition, due to the high dilution of base material and filler metal in SAW of thick plates, the concepts for the welding heat input assessment, such as the calculation of preheat and interpass temperatures via the carbon equivalent (e.g., according to DIN EN 1011), fail. Furthermore, the concepts are not applicable when the HACC occurs in the HAZ. The mechanical behaviour of the SAW joint is affected in the HAZ in terms of hardening (Nb-rich steels) or softening (Ti-rich steels). In particular, hard HAZ regions with reduced ductility are a-priori (mechanically) notch-sensitive and thus at high risk for delayed HACC.
In welding processing, the current state of the art explicitly does not consider structure- and alloy-dependent hydrogen diffusion behaviour or the influence of different heat dissipation on the SAW joint microstructure. Hence, there is a strong need for further investigations.
It is completely open how changing alloying concepts affect the hydrogen diffusion and, thus, the delayed HACC in SAW of thick plates. However, knowledge of the alloy-specific diffusion behaviour in the weld and HAZ is extremely important, e.g., for the development of sufficient post weld heating concepts to avoid HAC.
Solution strategy
The interaction of microstructure, hydrogen diffusion and high residual stresses (due to the high shrinkage restraint) of high-strength heavy plates with yield strengths ≥ 690 MPa joined by SAW has not been investigated so far. Systematic separation and evaluation of the interdependencies of these three factors is necessary to evaluate the delayed HACC. For this purpose, the microstructure- and alloy-specific hydrogen transport behaviour of SAW joints made from different base material and welding consumables combinations under variation of welding heat input must be known. Derived heat treatment procedures provide, if necessary, alloy-specific measures. The necessary determination of the influence of the real, strongly increased multiaxial stress conditions in SAW heavy plate joints can be achieved on a laboratory scale only by ensuring similar component stiffness and locally hindered weld shrinkage of the specimens. For this purpose, the following partial results are to be achieved:
- Determination of hydrogen ingress from the used welding consumables (wire and flux) combinations in different states (as-received/re-dried) on ISO 3690 specimens.
- Mapping of weld microstructures and specific precipitation behaviour of similar and dissimilar high-strength base and welding consumable combinations on free-shrinkage SAW specimens.
- Determination of microstructure and alloy specific hydrogen diffusion coefficients to derive heat treatment times and release temperatures.
- Component welding tests under external shrinkage restraint to transfer real multiaxial stress conditions to laboratory scale.
- Recommendations for favorable material combinations and welding heat input, and practicable alloy-dependent hydrogen removal heat treatment (DRHT) diagrams.
Work packages
Comprehensive experimental investigations are planned to address the metallurgical causes affecting mechanical properties and hydrogen diffusion in high-strength submerged-arc welded heavy plates. For this purpose, the welding heat input, its dissipation and the design-induced shrinkage and their influence on the multiaxial residual stress state are to be quantified. Common base material and welding consumable (wire and flux) combinations of the strength class 690 MPa are to be used.
Project management
Bundesanstalt für Materialforschung und -prüfung (BAM)
Department Component Safety
Division Weld Mechanics
Research partners
The PhoSten project is a research cooperation between the Bundesanstalt für Materialforschung und -prüfung (BAM) and the Forschungsvereinigung Stahlanwendung e. V. (FOSTA)
Funding
The IGF project 21714 N / Fosta P 1525 "Avoidance of cold cracking in submerged arc thick plate welds made of high-strength steels" of FOSTA - Forschungsvereinigung Stahlanwendung e. V., Düsseldorf, is funded by the Federal Ministry of Economics and Climate Action via AiF within the framework of the program for the promotion of joint industrial research (IGF).