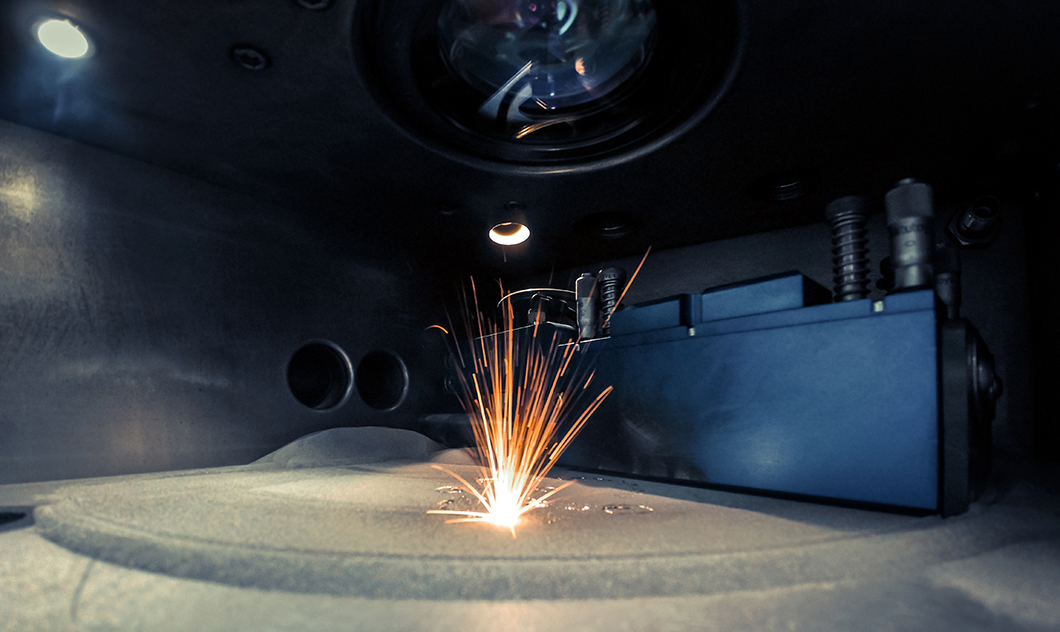
A 3D printer that prints metal. Metal is sintered into shape under the influence of a laser.
Source: iStock
Project period
01/01/2023 - 31/12/2024
Project type
Collaborative research project
Project status
Ongoing
Description
The aim of the "MRO 2.0 - Maintenance, Repair & Overhaul, phase II" project is to develop new technologies for maintenance and repair activities in an expediently automated refurbishment process chain, including the upgrade for high-efficiency gas turbines.
Location
Bundesanstalt für Materialforschung und -prüfung
Unter den Eichen 87
12205 Berlin
In the newly built production hall of Siemens Energy, research will in future be conducted on repair and maintenance topics. Source: Werner-von-Siemens Center
Source: BAM
Source: BAM
Review: MRO 2.0 - Maintenance, Repair & Overhaul – phase 1
The "MRO 2.0 - Maintenance, Repair & Overhaul" project began in 2020. The first phase (01.07.2020 - 31.12.2022) focused on developing new technologies for maintenance and repair activities that simultaneously represent an upgrade, i.e. an improvement in the properties of the component. Improved properties in turn lead to higher efficiency and lower emissions.
The use of future technologies such as digital solutions or additive manufacturing processes can lead to product and process innovations that enable longer operating intervals. Within the framework of the Werner von Siemens Centre, components, systems and machines will no longer be repaired in the classic way, but will be equipped with better properties through new technologies during the repair process: Upgrade instead of Repair. Maintenance, Repair and Overhaul refers to the classic maintenance and repair business with which components, systems and machines are overhauled. Typically, this is done through static repair process chains in which the same value-adding steps are carried out continuously. After repair or maintenance, the plant and machinery continues to operate with identical characteristics.
BAM's contributions in phase 2
CAx chain for the repair of moving blades by wire arc process
Dr. Andreas Pittner, Welding Technology Division
Water vapor resistance of ceramic materials for combustion chambers
Artur Göbel, Materialography, Fractography and Ageing of Engineered Materials Division
Development of a quality tool for in-situ process monitoring of additive manufacturing in the powder bed processes
Dr.-Ing. Kai Hilgenberg, Additive Manufacturing of Metallic Components Division
Damage and measure prediction
Dr. Jürgen Olbricht, Experimental and Model Based Mechanical Behaviour of Materials Division
Determination of wall thickness of turbine blades
Dr.-Ing. Jens Prager, Acoustic and Electromagnetic Methods Division
Detection of cracks of turbine blades
Dr. Mathias Ziegler, Thermographic Methods Division
Project coordination
Dr.-Ing. Jens Prager, Bundesanstalt für Materialforschung und -prüfung (BAM)
Partners
Siemens Energy Global GmbH & Co. KG
Technische Universität Berlin
Fraunhofer Institute for Production Systems and Design Technology
KleRo GmbH Roboterautomation
GESTALT Robotics GmbH
YOUSE GmbH
Datalyze Solutions GmbH
SERVITIZE UG
CONTACT Software GmbH
Funding
The project is carried out within the Werner-von-Siemens Centre for Industry and Science. It is funded by the Investitionsbank Berlin (ProFIT) and co-financed by the European Regional Development Fund (ERDF).

Logo of the Werner-von-Siemens Centre for Industry and Science
Source: WvSC

Logo des EU European Regional Development Fund
Source: EU