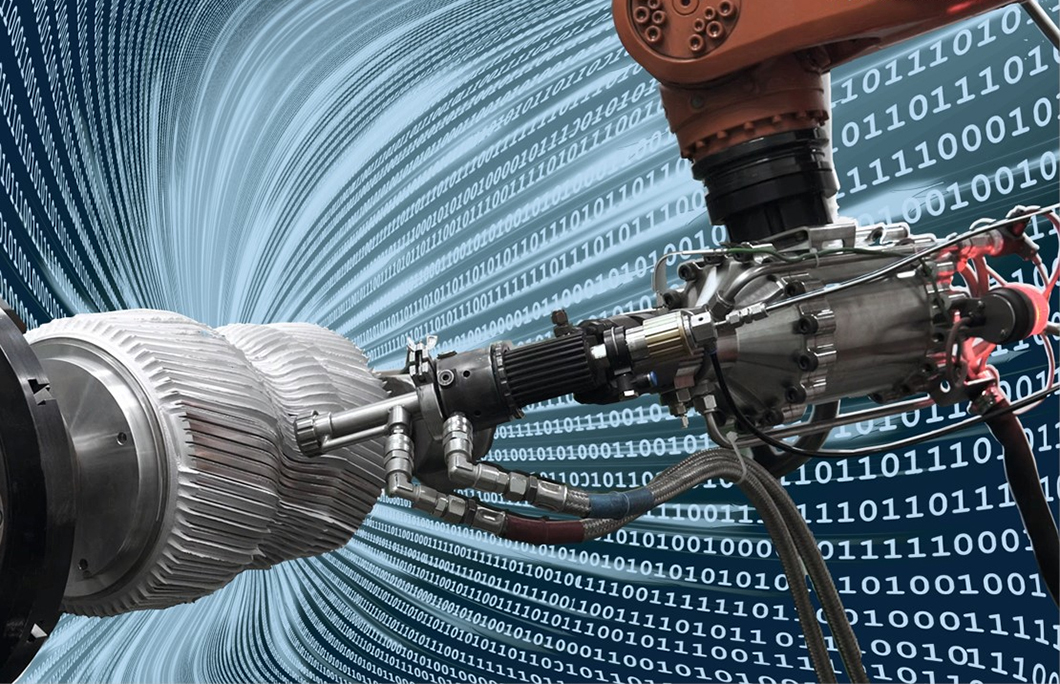
Robot arm with cold spraying system
Source: Helmut-Schmidt University | University of the Federal Armed Forces Hamburg
Project period
21/01/2021 - 31/12/2024
Project type
Collaborative research project
Project status
Closed
Description
The goal of CORE is the improvement of cold spraying for the repair of highly stressed components in the aerospace industry to significantly reduce the costs and resource consumption of repair work.
Location
Bundesanstalt für Materialforschung und -prüfung (BAM)
Unter den Eichen 87
12205 Berlin
Component with repaired zone (top) Source: Helmut-Schmidt University | University of the Federal Armed Forces Hamburg
Source: BAM
Source: BAM
Source: BAM
Partners
Helmut-Schmidt University | University of the Federal Armed Forces Hamburg
Bundesanstalt für Materialforschung und -prüfung
Lufthansa Technik AG
Airbus Defence and Space GmbH
GTT-Technologies
H. Loitz Robotik
Impact Innovations GmbH
KIT - Karlsruhe Institute of Technoloty
Funding
dtec.bw
CORE - Computerized Refurbishment
Cold spraying as a repair process in the aerospace industry
The production of highly stressed components in the aerospace industry is usually cost and resource intensive. Due to high safety requirements, components that are defective because of faulty manufacturing or mechanical stress are often replaced. As an alternative, local repair of defects can lead to large cost savings and is in line with sustainable, resource-saving business practices. In view of that, a promising process is cold spraying, in which metal particles are accelerated to supersonic speed in a gas stream and applied to a surface. High, local plastic deformation removes oxide layers and creates a strong bond between the particle and the surface. This allows new material to be applied layer by layer. For component repair, a defect is first worked out (e.g. by milling). The removed material is then reapplied near-net-shape by means of cold spraying. Subsequently, the the original component geometry is mechanically worked out. The advantage of the cold spraying lies in the low heat input. In other additive manufacturing processes, this can lead to a degradation of the material properties in the component.
The CORE project: Automation of the cold spraying process
Ideally, the goal of a repair process is to restore the component properties of the undamaged (new) component. If the process parameters are not optimized, this cannot be guaranteed, as defects, microcracks and residual stresses may be introduced. In particular, the cyclic strength can be greatly reduced compared to a new part. The challenge in cold spraying is the large number of parameters that must be set. Different component and defect geometries imply a great variation of the optimum parameters. Until now, these have had to be determined individually for each repair.
The CORE project is pursuing the approach of digitally recording all critical framework conditions of cold spraying and implementing a process chain for the repair procedure in an automated and computer-controlled manner. This is intended to ensure the reproducibility of the required properties. High-strength aluminum alloys from the aerospace industry are used as the base material in the project. Typical component and defect geometries will be defined together with the industrial partners. In cooperation with the industrial partners, a test cell for cold spraying is being set up at Helmut Schmidt University for the repair of components. In the further course of the project, this will be used to determine algorithms for defining optimum process parameters regarding mechanical properties. Accompanying the investigation of the mechanical properties, material tests will be carried out to determine residual stresses and defect distributions.
BAM's contribution to the CORE project
An important aspect affecting the mechanical properties of cold sprayed repair-material is the adhesion to the base material. To optimize it, the adhesion of the coating is investigated after prior laser structuring of the surface to be coated. The parameters of the surface preparation are chosen to achieve the best possible adhesion. The work on laser structuring is being carried out at BAM's Additive Manufacturing of Metallic Components division.
Component fatigue plays an important role, especially in the aerospace sector. In order to determine the cyclic mechanical properties of repaired components, fatigue tests are carried out in the Weld Mechanics division using repair materials produced with different process parameters. The tests include fatigue life testings, fatigue crack growth determination, and cyclic plastic deformation behaviour testing. Subsequently, fractographic and microstructural investigations of the cause of failure will be performed. Besides purely mechanical damage, corrosion plays an important role for component integrity. Stress corrosion cracking is considered particularly critical in this respect, as it can lead to sudden, brittle failure of components without prior external indication. The sensitivity of repaired material to stress corrosion cracking is determined in the Component Safety department.
The results of the fatigue tests are used in the development of algorithms for automated reprocessing of component defects at Helmut Schmidt University. Fatigue crack growth is important regarding the evaluation of the material's defect tolerance and can thus serve to identify possible permissible defects in the component. The experimentally determined cyclic deformation behaviour is used to create a material model for simulating specimen and component deformation.
Project coordination
Helmut-Schmidt University | University of the Federal Armed Forces Hamburg
Institute of Materials Engineering, Prof. Dr.-Ing. T. Klassen, Dr. rer. nat. F. Gärtner
Project partners
Bundesanstalt für Materialforschung und -prüfung (BAM)
Division Weld Mechanics division
Additive Manufacturing of Metallic Components division
Helmut-Schmidt University | University of the Federal Armed Forces Hamburg
Institute of Materials Engineering,
Professorship for Automation Technology
Other project partners
Lufthansa Technik AG
Airbus Defence and Space
GTT-Technologies
H. Loitz Robotik
Impact Innovations GmbH
KIT - Karlsruhe Institute for Technology
Funding
The CORE project is funded by the Center for Digitization and Technology Research of the German Armed Forces dtec.bw

Source: dtec.bw