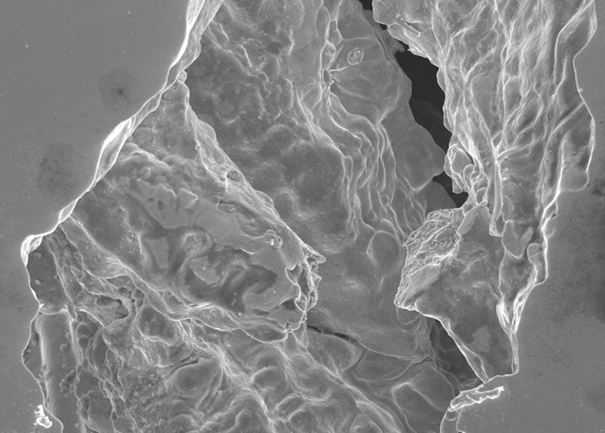
SEM image of a solidification crack in a high-strength weld metal
Source: BAM, Weld Mechanics division
Project period
01/05/2021 - 31/07/2023
Project type
Interdisciplinary project
Project status
Closed
Description
The project focuses on the influence of design boundary conditions on the solidification cracking tendency when welding high-strength steels.
Location
Bundesanstalt für Materialforschung und -prüfung
Unter den Eichen 87
12205 Berlin
Factors influencing solidification cracking Source: BAM, Weld Mechanics division
High-strength fine-grain structural steels offer the possibility of a material-efficient light weight design. Welding is the main joining technology. But the mechanical stresses resulting from often complex geometries already act on the joints during welding. The solidification cracking susceptibility of various high-strength filler metals is to be quantified under variable mechanical loads depending on the welding parameters.
Source: BAM
The aim of the project is to identify critical combinations of design features and welding parameters for different base and filler material combinations for the formation of solidification cracks. In the project, recommendations are to be developed with the help of which solidification cracks can be reliably prevented during welding of high-strength fine-grain structural steels
Source: BAM
Selected materials are subjected to a solidification cracking test under variable loads. After that the complexity of the weld boundary conditions is systematically increased. Single-layer butt joints are followed by tests on different seam and joint types. Critical loads are quantified using three-dimensional test facilities. Laboratory results are compared to industrial case studies and recommendations for practice are made.
Source: BAM
Project implementation
Bundesanstalt für Materialforschung und -prüfung (BAM)
Weld Mechanics division
Funding
AiF within the framework of the programme for the promotion of joint industrial research (IGF), Federal Ministry of Economics and Climate Action
BeKoRi - Evaluation of solidification cracking during welding of high-strength fine-grained structural steels
Initial situation
By using high-strength steels, it is possible to reduce the load-bearing cross-section for the same load. The weight of the construction is reduced. This is also desirable from the point of view of the CO2 balance, as less steel generally causes fewer emissions during production. To optimally counteract the same or higher loads with smaller amounts of material, modern constructions are becoming increasingly complex and elaborate. The result of this ongoing optimization is high mechanical stresses in large parts of the construction. Welding is the most important joining technology for steel. High stresses affect the weld seams not only in operation but already during joining. Under these aspects, solidification cracks can form in the weld seam even in materials considered resistant to solidification cracking.
Solution strategy
- Basic investigation of the susceptibility to solidification cracking of filler metals for S690 to S960 in the Varestraint test to quantify critical boundary conditions
- Transferability analysis based on MAG welded butt joints under controlled mechanical load in a 2 MN test facility
- Identification of failure criteria and verification on the basis of case studies with increasing degree of complexity
- Derivation of parameters and formulation of recommendations for practice
Project implementation
Bundesanstalt für Materialforschung und -prüfung (BAM)
Weld Mechanics division
Funding
The IGF project 21837 N / Fosta P 1516 "Bewertung konstruktiv bedingter Erstarrungsrisse beim Schweißen hochfester Feinkornbaustähle" of FOSTA is funded by the Federal Ministry of Economics and Climate Action via the AiF within the framework of the programme for the promotion of joint industrial research (IGF) on the basis of a resolution of the German Bundestag.

Source: IGF, AiF, FOSTA and BMWK