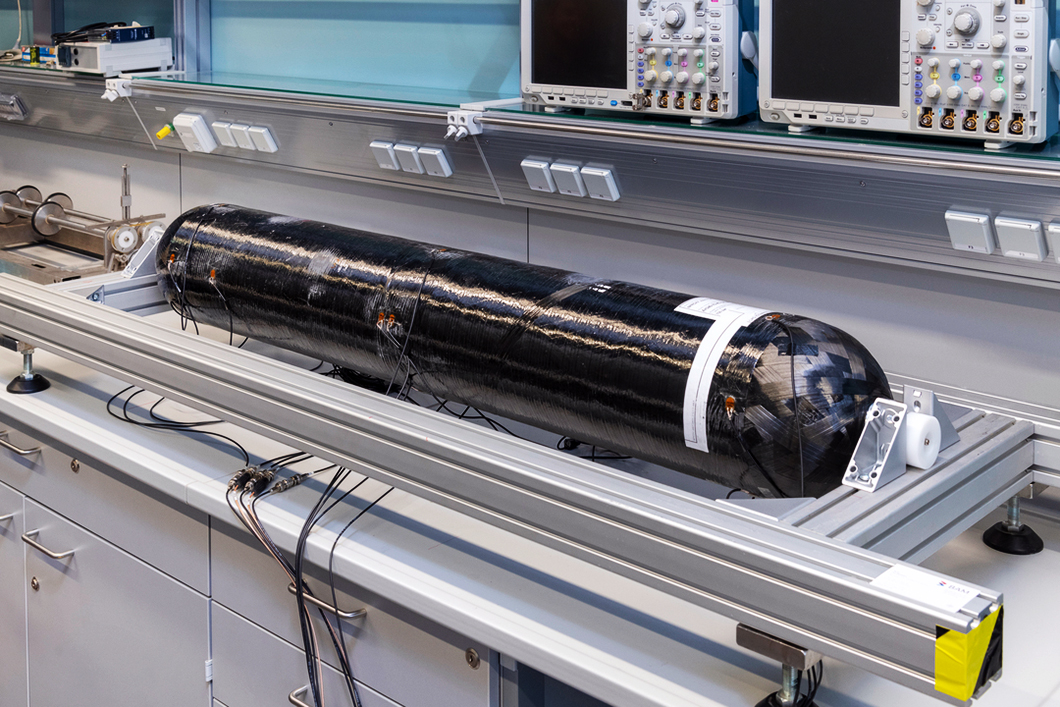
Up to 20 per cent CFRP material can be saved in the manufacture of hydrogen pressure accumulators
Source: BAM
Hydrogen pressure vessels play a key role in decarbonisation: in future they are to serve as "fuel tanks" for emission-free trucks, buses, trains, container ships and aircraft, as well as for the storage and transport of hydrogen. But the carbon fibre reinforced plastics (CFRP) from which the storage tanks are made have a large CO2 footprint due to their energy-intensive production. In a joint project, the Bundesanstalt für Materialforschung und -prüfung (BAM) is researching how the storage systems can be produced in a more climate-friendly way and how they can be used over a longer lifetime than before - with even greater technical safety.
Currently, up to 2.5 tonnes of CO2 are released during the production of a latest-generation hydrogen pressurised storage tank made of CFRP. Experts assume that the demand for these containers will rise sharply in the transition to a hydrogen economy. In addition to the transport sector, hydrogen pressure vessels will also be needed in the future for stationary power-to-gas applications and to transport the green energy carrier to hydrogen filling stations.
A new project coordinated by RWTH Aachen University and involving several companies that jointly manufacture such storage tanks aims to significantly improve their carbon footprint.
To achieve this, the project is tackling two issues: Firstly, the cost-intensive lightweight material CFRP is to be used more efficiently than before. "Currently, the tanks, which have to withstand a pressure of up to over 700 bar during operation, are designed particularly conservatively for safety reasons, i.e. a lot of material is used," explains Eric Duffner, expert for the storage tanks, who is responsible for BAM's participation in the project. "However, our investigations over many years indicate that the material can be used more sparingly."
Consistent digital process monitoring during production is intended to ensure that the storage units are manufactured more efficiently, i.e. using only as much CFRP material as necessary. "In the project, we assume that by optimising the production, around 20 percent of the material can be saved and at the same time even safer memories can be produced than before," says Duffner.
The second approach is aimed at the "lifetime" of the storage units, i.e. the period over which they are actually used. "Here, too, our extensive investigations into mechanical and thermal loads indicate that the storage units could remain in operation much longer than before," says Eric Duffner.
BAM will incorporate its findings from non-destructive testing methods into the project in order to place the current safety assessments and assumptions about service life on a better empirical basis. This will also help to save resources: Because if the storage tanks were to be able to be used in the future for, say, 10 years longer than they have been up to now, this would mean - in addition to the material savings in production - a considerable reduction in their carbon footprint.
Finally, the scientific results of the project are to be incorporated into the standards and laws on hydrogen pressure storage systems. The overall project is funded by the Technology Transfer Programme Lightweight Construction of the Federal Ministry of Economics and Climate Action.