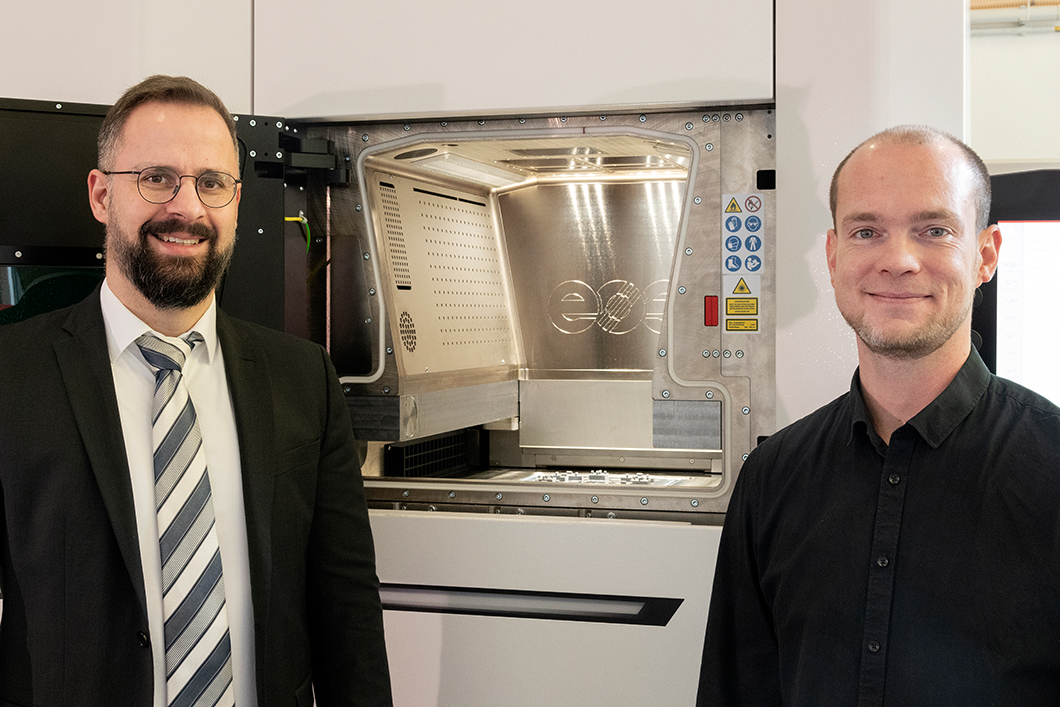
Dr. Kai Hilgenberg, Head of the BAM Competence Centre for Additive Manufacturing and Dr. Martin Epperlein, coordinator of the pilot project in front of the new 3D printing facility for metals (from left to right).
Source: BAM
The Bundesanstalt für Materialforschung und -prüfung (BAM) has expanded the equipment park of its Competence Centre for Additive Manufacturing: the new EOS M300-4 multilaser system is intended to improve additive manufacturing processes and digitalise quality assurance. The system is part of the living lab for SMEs that is being set up at BAM's centre of excellence. It supports companies in bringing 3D printing of safety-relevant components into application more quickly.
Additive manufacturing holds great potential for the production of highly complex components, bionically inspired lightweight components or even prototypes. It can be used in many industries - from aircraft construction and gas turbines to medical technology. However, the quality assurance of additively manufactured products is still a challenge. During the manufacturing process, large amounts of data are generated even for small components. They are difficult to evaluate due to the large number of formats. In addition, there is a lack of norms and standards for additive manufacturing that ensure component quality.
In the new Additive Manufacturing for SMEs living lab, BAM is working together with the central partners of the German Quality Infrastructure (QI) on solutions for digitally supported quality assurance as part of the QI-Digital initiative. "The aim is to jointly develop a networked process chain that fully digitally tracks the entire manufacturing process - from the source material to the manufacturing process to the finished component and the downstream non-destructive tests," says Kai Hilgenberg, head of BAM's Additive Manufacturing Competence Centre. "The data obtained in this way will be used to create smart standards and digital certificates that enable end-to-end digital quality assurance for additive manufacturing."
The research work in the living lab is supported by the new multilaser system, in which four lasers work in parallel. This speeds up the manufacturing process. In addition, the AM team wants to expand the facility with equipment for process monitoring, such as thermographic and optical cameras. In this way, important data on quality-relevant process parameters will be obtained, which can be evaluated specifically and quickly using AI methods.
The digital process chain should be in place in the real laboratory at BAM by mid-2023. However, interested companies can already actively participate in the development, testing and application of the networked process chain. "Our living lab offers optimal conditions for testing new technologies for digital quality assurance in an industrial environment," says Martin Epperlein, coordinator of the pilot project at BAM. "The bundling of a wide range of competences at BAM is unique and our laboratory helps to bring scientific results into industrial application more quickly."
"Our EOS M 300-4 is not only one of the most powerful multilaser systems for metal 3D printing, but a digital production platform. With its digital interfaces, it enables the digitalisation of the entire industrial process chain," adds Dr. Tina Schlingmann, Regional Director EMEA, EOS GmbH. "This enables BAM to develop a modern digital infrastructure for efficient quality assurance for additively manufactured components using our technology."
Find more information on the BAM Additive Manufacturing Competence Centre here.