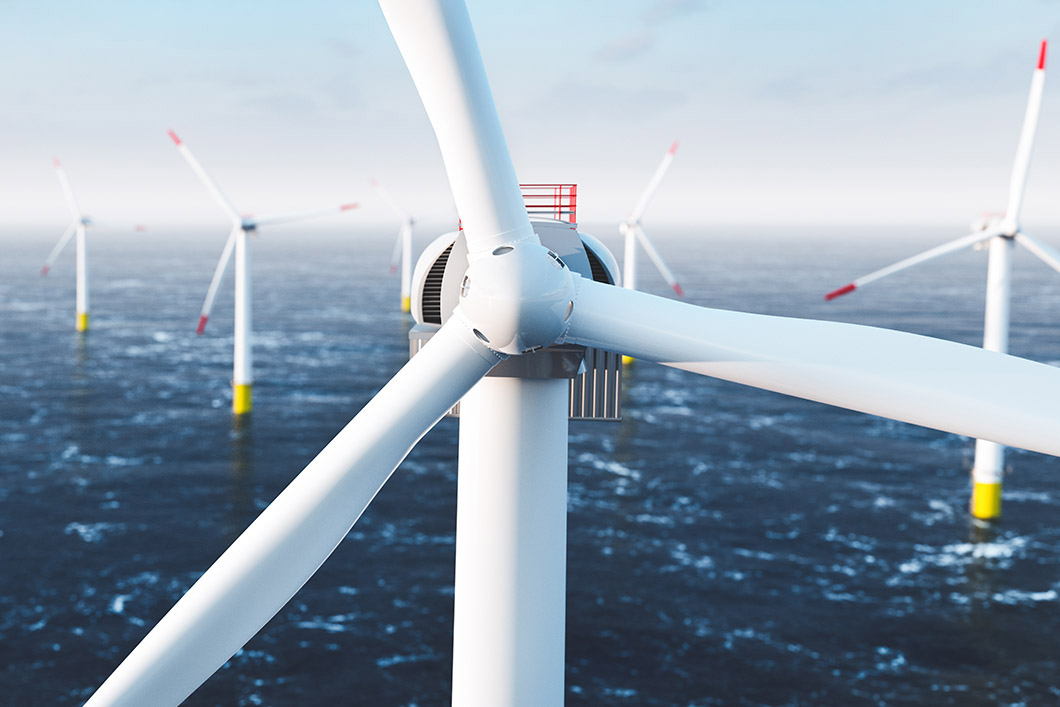
Source: Photocreo Bednarek/Adobe Stock
The expansion of offshore wind energy is crucial for Germany and the EU to achieve their climate goals. What is little known is that a significant amount of CO2 could already be saved during the manufacturing of the wind turbines. In a new project, BAM, together with partners from science and industry, is investigating the combination of lightweight design principles with digitalised manufacturing. The results promise considerable CO2 savings that can also be transferred to other areas of steel construction.
Offshore wind turbines stand on a huge support structure up to 60 metres of height; the larger part of it remains hidden below the waterline. Today, a single steel pile, a so-called monopile, is often used. For this, up to 2000 tonnes of steel are welded together - the production of which releases large amounts of CO2.
The tonnage and thus the amount of CO2 released during steel production is much lower when more filigree support structures are used instead of monopiles. However, these lightweight structures, known as jacket foundations, are still challenging in terms of production technology, so that CO2-saving potentials have not yet been realised industrially.
This is mainly due to the complex welding seams: Today, the jacket foundations are mostly welded manually and later transported to their place of use by special ships. Tolerances in manual production and high safety requirements result in a conservative design, i.e. thick-walled components are used.
"Automated welding processes that simultaneously achieve optimised geometries of the weld seams could increase the fatigue strength of the foundations and thus reduce the amount of steel required during manufacturing," explains Andreas Pittner of the Bundesanstalt für Materialforschung und -prüfung (BAM). "The potential savings are impressive."
For an average 12-megawatt turbine, 20 per cent in weight, i.e. about 400 tonnes of steel and correspondingly about 800 tonnes of CO2 could be saved compared to a monopile. By optimising the design of the welding seams according to bionic principles as well as savings in the energy-intensive welding itself, the CO2 content in production can be further reduced. All in all, for a wind farm with 100 turbines, there is a savings potential that would correspond to over 100,000 tonnes of CO2.
However, the very complex welding seams of the jackets still pose a challenge for automated production - which in turn would be a prerequisite for the application of lightweight design principles in steel construction.
The new joint project "SmartWeld", which is led by Andreas Pittner, is now addressing the associated issues. It is funded by the Federal Ministry for Economic Affairs and Energy as part of the Technology Transfer Programme for Lightweight Construction with 3.17 million euros and is scheduled to run for three years. In addition to BAM, the Institute for Steel Construction and the Test Centre Support Structures at Leibniz Universität Hannover, the Fraunhofer Institute for Wind Energy Systems (IWES), Salzgitter Mannesmann Forschung GmbH as well as Jörss - Blunck - Ordemann GmbH are involved.
"We want to enable the use of lightweight design techniques by continuous digitalisation of the entire manufacturing and testing chain," says Pittner. "This concerns the design of the equipment through manufacturing, component testing and quality management. In doing so, we deliberately work under industrial conditions so that the technology transfer to industry can succeed quickly later on."
Ultimately, the support structures of wind turbines are just one application example of the potential for saving CO2 through lightweight design. The findings of SmartWeld could later be transferred to other areas where large-format steel structures are manufactured, e.g. support structures for bridges.