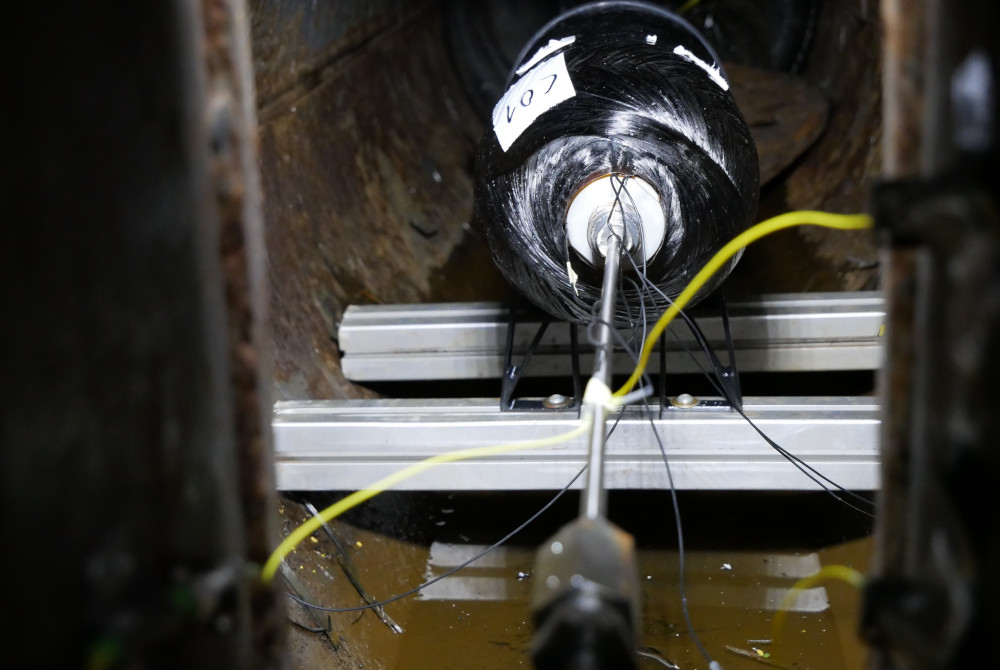
Composite pressure vessel with integrated fibre-optic sensors immediately before a burst test.
Source: BAM
Composite pressure vessels are becoming increasingly important for a wide range of applications, including the storage of hydrogen gas and breathing air. To further increase their safety level, their behaviour must be investigated holistically, including the impact of the manufacturing process. Composite pressure vessels are mostly manufactured using the wet filament winding process, which is characterized by multiple parameters influencing the performance of the finished component.
In the published study, two designs of 6.8-litre composite pressure vessels were manufactured. The geometry, stacking sequence of the carbon fibre plies and the materials used were kept constant for both designs. The only differing parameter was the internal pressure in the polymer liner during the filament winding process. The goal of the internal pressure regulation was to achieve a more even residual stress state and minimize the waviness of carbon fibre plies.
To monitor the strains in the composite structure, we embedded fibre optic sensors into the composite structures of four cylinders. In total, 10 composite pressure vessels were manufactured and subjected to slow burst tests to assess their safety performance.
Our statistical evaluation of the results shows that an increase in the survival rate is achieved due to the internal pressure regulation. This is a result of the decreased scattering of the burst pressures. Since internal pressure regulation during filament winding leads to negligible additional cost, the method has been proven to increase the safety performance in a nearly cost-neutral manner.
Impact of internal pressure control during manufacturing on residual stresses and safety performance of type 4 pressure vessels
Author links open overlay panel
Bartosz Popiela, Stephan Günzel, Marcus Schukar, Georg W. Mair, Katerina Krebber, Holger Seidlitz
Composites Part C: Open Access, 2025