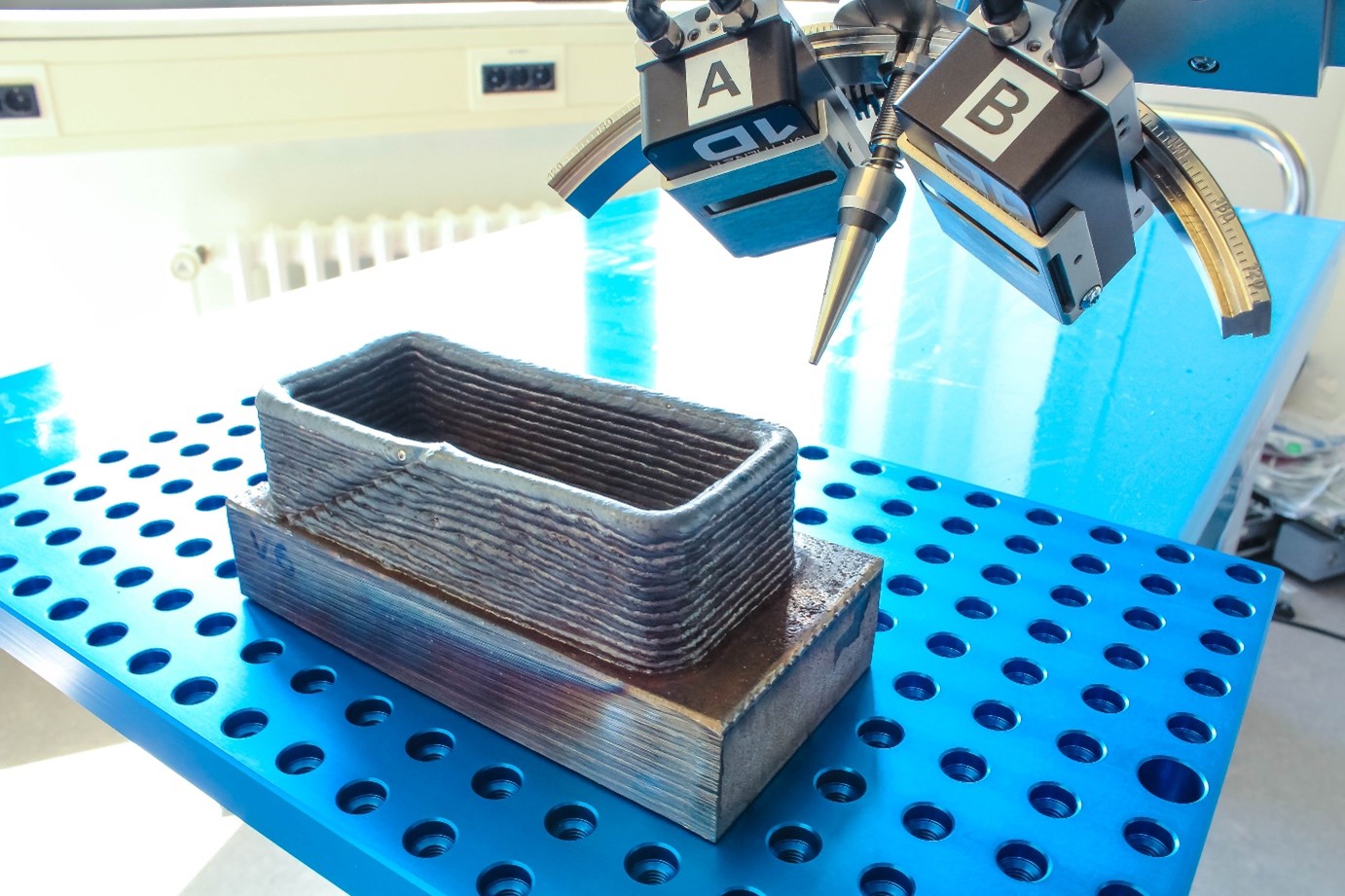
Residual stress analysis of an additive manufactured high-strength steel component
Source: BAM
The use of high-strength fine-grain structural steels has tremendous potential for many steel construction applications for weight-optimized, efficient structures with high mechanical load-bearing capacity, such as those currently required urgently in the wind energy sector. In addition, further significant increases in efficiency can be achieved applying additive manufacturing steps and bionic construction methods. For this purpose, commercial high-strength wire-shaped additive materials are already available for shape-giving metal active gas welding ("Wire Arc Additive Manufacturing", WAAM).
The broad economic application still lacks quantitative statements on the production-related stresses and component safety that results from additive manufacturing and ultimately affect component performance in operation. This relates in particular to process- and material-related influences and the shrinkage and distortion occurring during cooling, which are considerably hindered due to the stiffness of the surrounding construction. These interactions may result in high tensile residual stresses. Together with the special microstructures and high-strength material properties, this poses a considerably increased risk of cold cracking of the components.
This article therefore experimentally investigated how the process conditions in additive manufacturing by means of welding arcs, in particular the welding heat control, and the design of the components affect the microstructure and hardness and the residual stresses. Reference specimens (hollow cuboids) were manufactured using a fully automated welding system under systematic variation of the heat control and design. The residual stresses on selected surfaces of all specimens had been analyzed by means of X-ray diffraction (XRD) and correlated with the input variables of welding heat control and component geometry as well as with the resulting microstructure and hardness.
Thus, increased heat input with each weld bead showed a lower residual stress level in the welding direction of the component walls. However, too high temperatures during welding and low cooling rates can result in a too low strength of the material. In component design, it is primarily the component height that affects the stress state after welding. Low component heights with the same thickness and stiffness of the substrate plate cause a higher residual stress level in the component.
Influence of the WAAM process and design aspects on residual stresses in high-strength structural steels
K. Wandtke, D. Schroepfer, R. Scharf-Wildenhain, A. Haelsig, T. Kannengiesser, A. Kromm, J. Hensel,
published in Welding in the World, 67, pages 987–996 (2023).
BAM Department Component Safety
BAM Division Testing Devices and Equipment
BAM Weld Mechanics