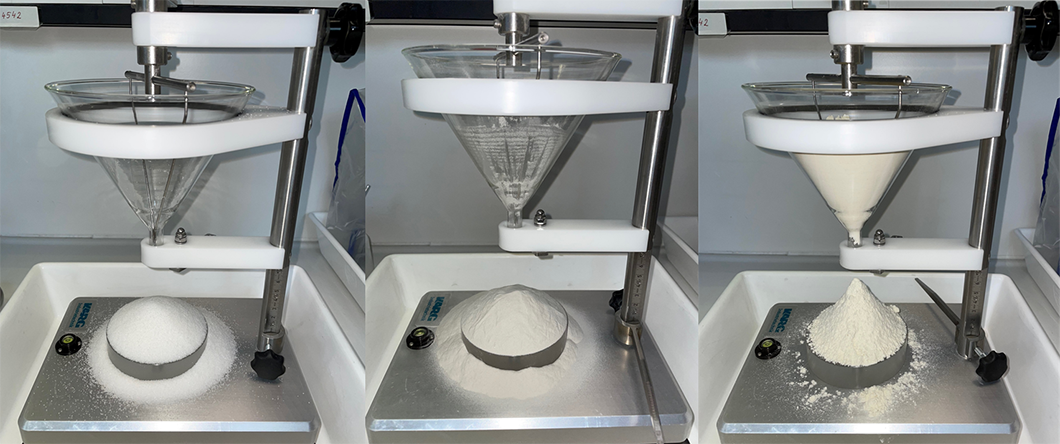
Conical pile for the measurement of the angle of repose: one of the quartz sand powders from the publication (middle image), compared to sugar (left) and flour (right).
Source: BAM, Advanced Multi-materials Processing division
Powders are a unique form of a material. In fact, powders can be considered as another state of matter. They can be compressed like a gas (but not as much). When compacted, they behave like a solid, and in the right condition powders can also flow like a liquid.
The flow behavior of powders is critical in many applications, one of which is additive manufacturing – a revolutionary technology in materials processing of ceramics, metals, and polymers. Powder bed fusion and binder jetting are additive manufacturing technologies in which a powder is deposited layer-by-layer to form a so-called “powder bed”. It is within this powder bed that the final printed part is embedded. The quality of the powder bed, and especially its packing density, is dictated by the ability of the powder to flow in the process. This behavior is commonly referred to as the powders “flowability” and part of our daily life when pouring sugar in your morning coffee or when emptying a bag of flour during baking. Sometimes the powder flows as well as a fluid, sometimes it does not flow at all.
A central problem of powder handling in additive manufacturing is the lack of a unifying definition. Instead, a variety of methods are used, the results of which are hard to compare. This limitation hampers process reproducibility, quality control, and knowledge transfer across processing technologies in additive manufacturing, which ultimately affects the performance of the printed part. Developing a unifying approach to feedstock flowability in additive manufacturing is therefore urgently needed to promote industrially viability and maturity of this novel materials-processing technology.
A team led by Andrea Zocca and Jens Günster, from the Multimaterials Processing division of the Materials Engineering department at BAM, and in collaboration with the Chair of Advanced Ceramic Materials at the Technische Universität Berlin, has now been able to develop a quantitative statistical method that unifies a variety of approaches, allowing to reliably distinguish between the flowability of seemingly similar powders that, however, behave very differently in different additive manufacturing processes. By investigating the correlations between flowability characterization and powder bed densities, the team identified which methods enable the prediction of powder bed density prior to processing, thereby helping materials scientists and process engineers in achieving dense, reproducible, and safe components. These findings, recently presented in Additive Manufacturing 47 (2021) 102250, will serve research and industry in unifying the characterization and screening of powders for additive manufacturing, paving the way to transferable standards of an emerging technology.
Characterization of powder flow behavior for additive manufacturing
Ilaria Baesso, D. Karl, Andrea Spitzer, A. Gurlo, Jens Günster, Andrea Zocca
published in Additive Manufacturing, Vol. 47, article 2250, pages 1 - 14, 2021
BAM, Advanced Multi-materials Processing division