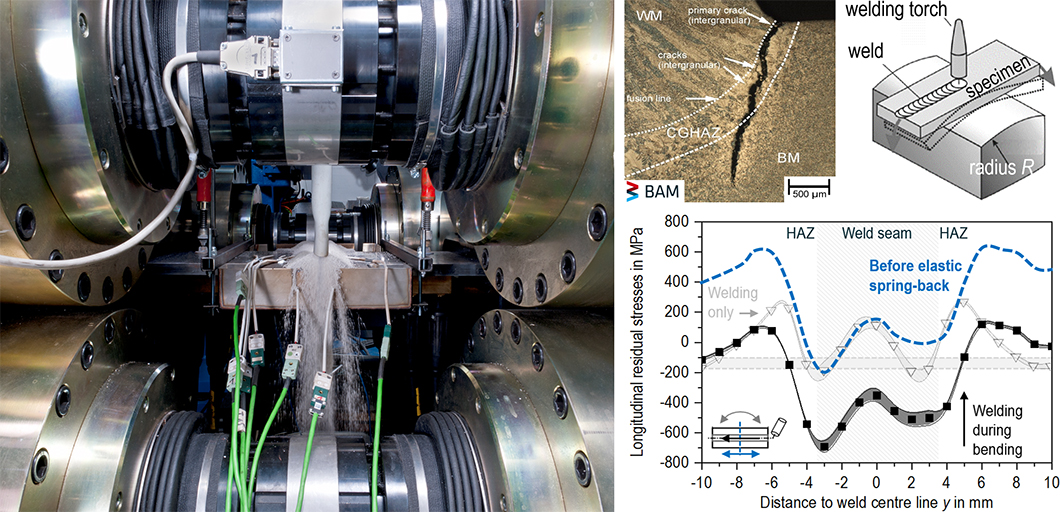
Transferability studies for crack prevention involving residual stress evaluation: From submerged-arc welding on component specimens and the 2 MN test system to testing concepts using small-scale laboratory specimens
Source: BAM, division Weld Mechanics
High safety requirements are specified for welded components, e.g. in power plants or installations that are exposed to high temperatures. In particular, these include the prevention of cracking. Creep-resistant steels are predestined for such applications but require extensive heat treatment after welding. The welded components, some of which take months to complete, are usually reactors or pressure vessels weighing several 100 t and are annealed for several hours at over 700 °C in hangar-like furnaces. So-called stress relief cracks can occur during this process, depending on the pre-stressing from the welding process. Their cause is a complex interaction of metallurgical, welding process and mechanical influences. In order to be able to investigate this type of cracking in detail, the extreme boundary conditions occurring in practice must also be realistically reproduced in the laboratory. In addition to the heat conduction of the high-performance submerged arc welding process, the design aspects due to the enormous component dimensions, i.e. high mechanical stiffness during welding, must also be considered. Parts I and II of this article series focused on cracking mechanisms. Part III deals with the transferability of stress analyses to a new very small-scale laboratory test under additional external loading during welding. With the 2 MN test system developed at BAM and different specimen setups related to actual components, welding experiments could be successively scaled over many orders of magnitude and the stresses on all specimens could be evaluated. For this purpose, residual stress analyses in the weld volume were also obtained by means of neutron diffraction at the reactor (HZB). It was shown that the high stresses caused by the welding process on large components can be transferred exceptionally well to the new testing technique on a laboratory scale. Based on the investigations, a series of recommendations could be made as to how the crack safety during welding of these sensitive materials can be systematically investigated and evaluated precisely with a low expenditure of time and materials.
Influence of welding stresses on relief cracking during heat treatment of a creep-resistant 13CrMoV steel Part III: assessment of residual stresses from small-scale to real component welds
Dirk Schröpfer, Arne Kromm, Thomas Lausch, Michael Rhode, R. C. Wimpory, Thomas Kannengießer
published in Welding in the World, pages 1–15, 2021
BAM division Weld Mechanics