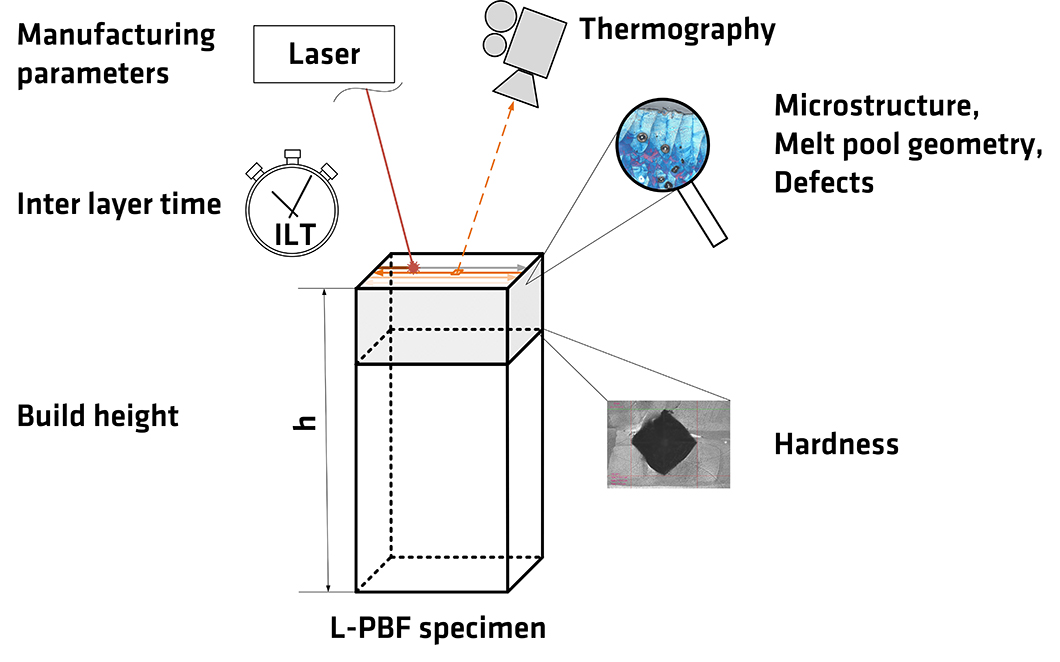
Schematic representation of the influencing parameters and analysis parameters
Source: BAM, Division Welding Technology
Additive manufacturing (AM) technologies offer a high degree of design freedom in the construction of components due to their layer-wise working principle. The manufacturing of small batch components and parts with a high degree of individualization benefit mostly from this. For the production of metallic components, the powder bed based Laser Powder Bed Fusion (L-PBF) is the most widely used AM technology. A three-dimensional volume model is first sliced into layers of a defined thickness. Based on the geometric information of the resulting two-dimensional cross sections, a metallic powder is melted layer by layer by a highly focused laser beam, creating solid material cohesion after rapid solidification. This manufacturing process has a multitude of factors that influence the resulting mechanical properties and the quality of the resulting components. In literature the inter layer time (ILT) as the time between the repeated melting of volume elements at the same lateral position in the following layer has hardly been considered so far. It is significantly influenced by the geometry of the component to be produced and by the exploitation of the powder bed volume.
The aim of this study is to investigate the effect of different inter layer times on the cooling of L-PBF components made of the austenitic stainless steel alloy 316L and on the resulting microstructure, defect formation and hardness. In addition to the inter layer time, three different volume energy densities of the manufacturing process parameters are considered. For the analysis of the cooling process an in-situ process monitoring by means of a thermographic camera is performed. It is shown that the inter layer time and the build height have a significant effect on the heat accumulation within the parts during production. It is also shown that this has a significant effect on the size of the sub-grain structures, the melt pool geometry and the hardness. Furthermore, an increase in defect density within the parts can be detected as an interplay between build height, inter layer time and volume energy density. The inter layer time is identified as a critical influencing factor for the production using L-PBF, especially for components with small cross sections.
Effects of inter layer time and build height on resulting properties of 316L stainless steel processed by laser powder bed fusion
Gunther Mohr, Simon J. Altenburg, Kai Hilgenberg
published in Additive Manufacturing, Vol. 32, pages 101080-1 to 101080-13, 2020
BAM, Division Welding Technology and Division Thermographic Methods