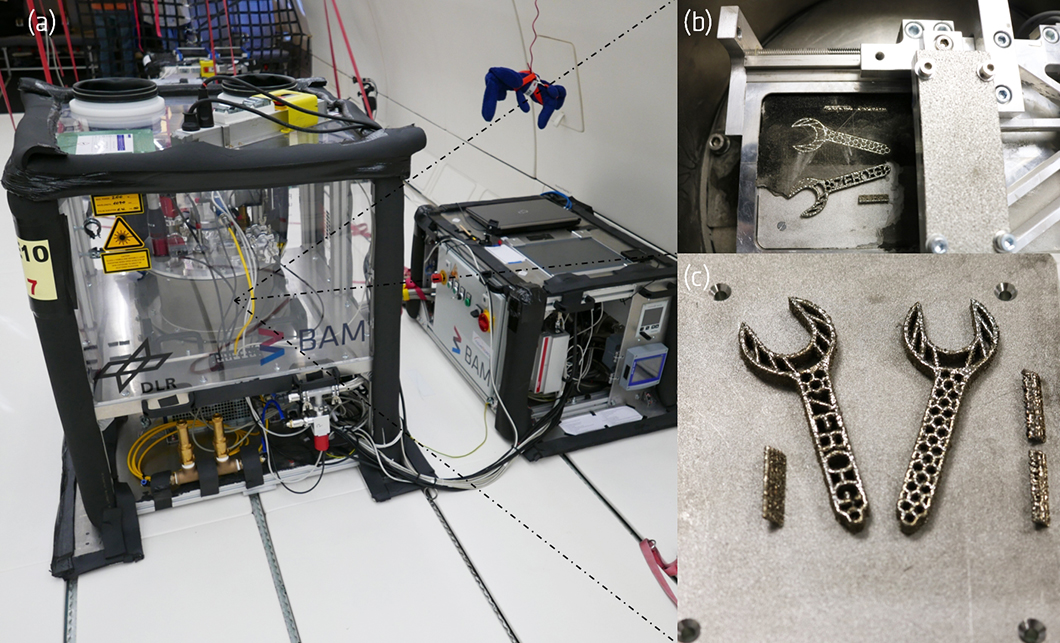
(a) Setup for LBM in μ-gravity mounted in the Airbus A310 ZERO-G during a parabolic flight campaign; (b,c) samples laser beam melted in µ-gravity
Source: BAM, Ceramic Processing and Biomaterials division
As humanity contemplates manned missions to Mars, strategies need to be developed for the design and operation of hospitable environments to safely work in space for years.
Already for the international space station (ISS), the planning of spare parts is an essential aspect of resupply missions. Still, it is not possible to have every spare part and tool available at
any time. Considering future human exploration of space involving longer missions and much larger distances to cover, it is even clearer that in-space manufacturing becomes a necessity.
To address these challenges, additive manufacturing (AM) technologies appear extremely attractive. In AM, compared to subtractive manufacturing, a component is built by adding a material, typically layer-by-layer. These technologies offer high flexibility in design and the ability to manufacture ready-to-use components directly from a computer aided model. For the manufacturing of metal parts, laser beam melting (LBM) is a widely spread AM process. This technology works by depositing thin layers of a powder and by selectively laser melting the powder in each layer according to the cross-section of the geometry to build. However, the deposition of powder layers for powder-based AM in absence of gravity is a challenging task, since the flow of the powder and the stability of the powder bed are generally governed by gravitational forces. For this reason, standard laser beam melting machines are not suitable to be used in µ-gravity conditions.
This paper describes a novel technology which enables the deposition of powder layers in the absence of gravity. The process is based on a gas flow established throughout the powder layers, which is used to stabilize the powder.
The paper reports in detail the development of a setup based on this technology and the testing which was performed in the course of three campaigns of parabolic flights. In a campaign, the airplane flies a maneuver which is named “parabola” for 31 times in one flight. In the central part (the cap) of each parabola, 22 s of µ-gravity are experienced. This phase was used to validate the deposition of powder layers in µ-gravity. Moreover, a preliminary study surveyed the effect of laser melting in µ-gravity. Finally, in this study the worldwide first metallic tool, a 12 mm wrench, has been manufactured by LBM at μ-g conditions. In summary, these results are a first step in enabling the additive manufacturing of metallic components in space.
Enabling the 3D Printing of Metal Components in μ-Gravity
Andrea Zocca, Jörg Lüchtenborg, T. Mühler, Janka Wilbig, Gunther Mohr, T. Villatte, Fabien Léonard, Gert Nolze, M. Sparenberg, J. Melcher, Kai Hilgenberg, Jens Günster
erschienen in Advanced Materials Technologies, pages 1900506 et seq., 2019
BAM, Divisions Ceramic Processing and Biomaterials Welding Technology Materialography, Fractography and Ageing of Engineered Materials