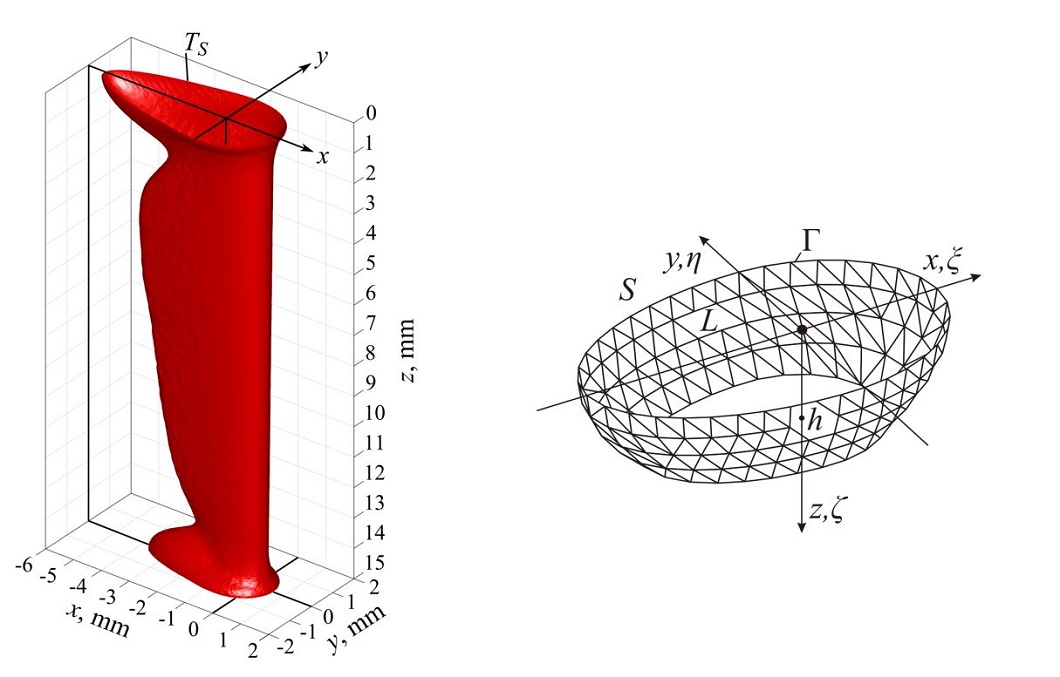
3D weld pool interface defined by the solidus temperature (left) and division of an exemplary weld pool interface into boundary elements (right)
Source: BAM,
In recent years, deep welding has become an everyday industrial tool that enables the joining of thick materials. The proper prediction of a welded joint requires information on the local microstructure and mechanical properties, which depend mainly on the temperature cycle of the workpiece. A numerical framework for simulation of the steady-state thermal behaviour in keyhole mode welding has been developed. It is based on the equivalent heat source concept and consists of two parts: computational thermo-fluid dynamics and heat conduction. The solution of the thermo-fluid dynamics problem by the finite element method for a bounded domain results in a weld pool interface geometry being the input data for a subsequent heat conduction problem solved for a workpiece by a proposed boundary element method. The keyhole shape as well as the main physical phenomena, such as thermo-capillary and natural convection and temperature-dependent material properties are taken into consideration. The developed technique is applied to complete-penetration keyhole laser beam welding of a 15 mm thick low-alloyed steel plate at a welding speed of 33 mm/s and a laser power of 18 kW. The fluid flow of the molten metal has a strong influence on the weld pool geometry. The thermo-capillary convection is responsible for an increase of the weld pool size near the plate surfaces and a bulge formation near the plate middle plane. The numerical and experimental molten pools, cross-sectional weld dimensions and thermal cycles of the heat affected zone are in close agreement.
Assessment of thermal cycles by combining thermo-fluid dynamics and heat conduction in keyhole mode welding processes
Antoni Artinov, Victor Karkhin, Pavel Khomich, Marcel Bachmann, Michael Rethmeier
International Journal of Thermal Sciences, Vol. 145, 105981 1, 2019
BAM Welding Technology division