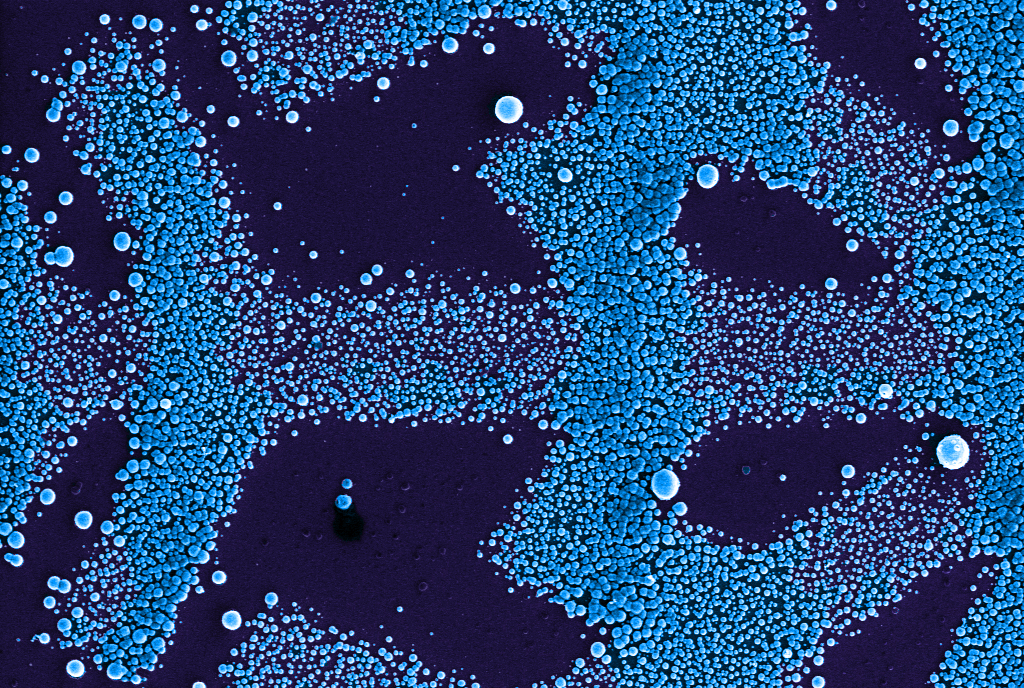
In order to use the potential of polydopamine, microstructures of a few ten-thousandths of a millimetre are required. BAM has now developed an innovative process to create them.
Source: BAM
The Bundesanstalt für Materialforschung und -prüfung (BAM) has developed an innovative process which allows polydopamine to be produced and deposited with unprecedented precision. Due to its unique properties, this material has great potential for applications in medical, sensor and safety technology. Presented by BAM the process makes it possible for the first time to produce the complex microstructures in the range of a few ten-thousandths of a millimetre.
The material of the future, polydopamine, is inspired by nature: Mussels produce the protein to attach themselves to surfaces of any kind. For some years now, polydopamine has also been produced in the laboratory. Because it adheres to materials of all kinds and can be described as an ideal "glue" for bonding materials together. Since polydopamine is at the same time highly biochemically active, it is excellently suited as a "reactor": Applied as a thin layer, it can impart unique chemical and physical properties to surfaces made of metal, ceramics or polymers. Thus, future applications in laboratory technology and so-called lab-on-a-chip systems are conceivable. Polydopamine could also be used in medical diagnostics, in vascular and cardiac medicine or in neurotechnology, for example as a contrast agent, bio-adhesive or for the controlled release of active substances.
For this purpose, extremely small amounts of dopamine solution have to be applied to a surface and then selectively polymerised, i.e. converted into a solid. The process is similar to 3-D printing - only this variation of molecular design involves a few ten-thousandths of a millimetre. With previous methods, it is not possible to control the morphology of the desired structures with sufficient precision.
A team at BAM led by Ievgeniia Topolniak has now used Multiphoton Lithography for the first time to build 2D microstructures from polydopamine. In this process, the individual layers of the liquid starting material are irradiated with pulsed laser light and thereby converted into the polymer polydopamine with its outstanding properties. By absorbing the photons of the laser, the basic elements polymerise into larger molecules and gain solid form. The speed and power of the laser allows the design of the microstructures to be controlled with high precision down to the range of a few ten-thousandths of a millimetre - a dimension that was previously unattainable for polydopamine.
Multiphoton lithography makes numerous areas of application for polydopamine, in which such precision of microstructuring is required, realistic for the first time. The BAM team's findings have now been published in the renowned journal Advanced Materials due to their significance for materials science.