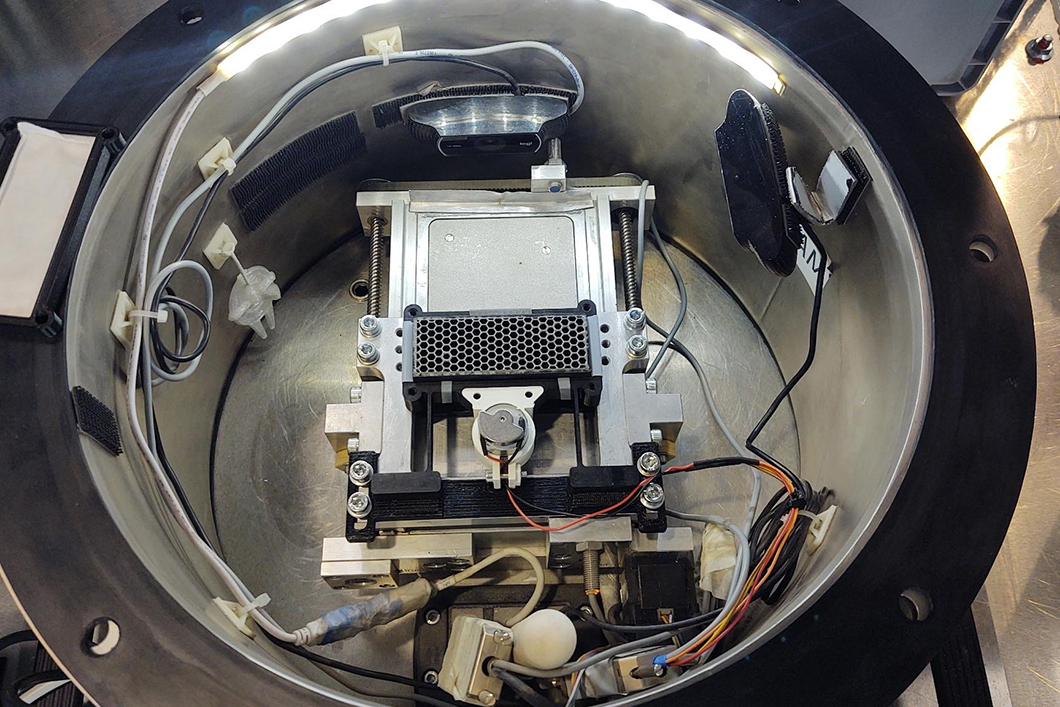
The facility used to study additive manufacturing under weightlessness was equipped with a new powder reservoir for current experiments
Source: BAM
From the laboratory to 3D printing in weightlessness: additive manufacturing processes offer a wide range of possibilities to produce different components or tools from one and the same material with complex designs, fast turnaround times and directly on site. Thus, applications for human spaceflight – in Earth orbit or on future Moon or Mars bases or during the mission to get there – are also of great interest. Together with the German Space Agency at DLR (German Aerospace Center) and DHM Prüfsysteme, BAM tested an improved design for 3D printing in weightlessness in DLR's 38th parabolic flight campaign in February 2022 and derived new findings from this.
"LSDzero - Powder-based additive manufacturing under reduced gravity conditions" is the name of the research project in which a component is built up layer by layer. The prerequisites for this are powder with sufficient flowability and a virtual 3D model of the desired component. After the layer has been deposited with the recoating system of the printer, the geometry is transferred from the virtual 3D model to the individual layer by means of a laser during the laser beam melting or laser powder bed fusion (LPBF) process. A central aspect here is the homogeneity of the layers before the sintering: If, for example, pores form in the component due to defects in the layer, this has a direct impact on the quality and stability of the final component.
An additional challenge for space applications are the different gravitational conditions. The handling of metal powders is essential for the LPBF process and challenging in the absence of gravity. In past experiments, the research team has shown that a gas flow throughout the powder bed can compensate for the missing gravitational forces in microgravity experiments such as parabolic flights. During the campaign in February, the scientists have once again optimised the powder layer application mechanism: The recoater or deposition unit that applies the powder to form a homogeneous layer previously consisted of a single powder container – which always led to an uneven distribution of the powder layer in weightlessness. Therefore, a new powder reservoir with multiple compartments has been tested in the last campaign. It limits the agglomeration of the powder to small and defined areas, and evaluations of the current experiments show that the new design improves the layer quality and thus increases the overall quality of the components.
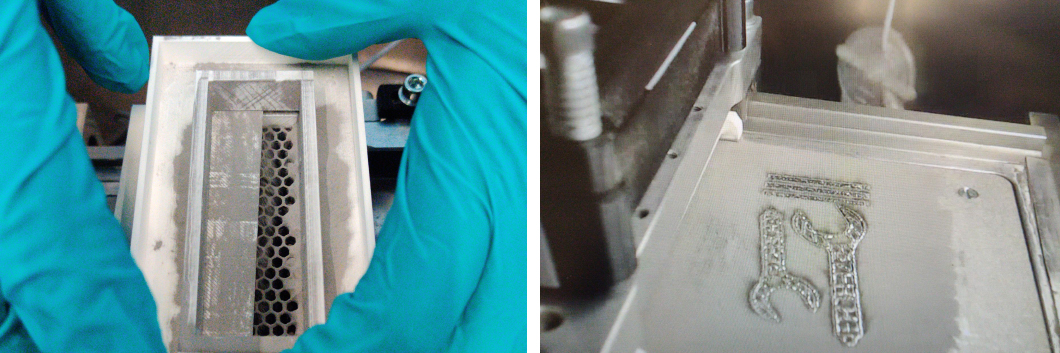
The new recoater design improves layer quality in 3D printing with metallic powder
Source: BAM
Detailed results of the development and evolution of the recoating systems for the gas flow assisted powder deposition process have been presented in March at the International Conference on Advanced Manufacturing for Air, Space and Land Transportation (ICAM22). The conference, co-organised by the European Space Agency (ESA) and the US Aeronautics and Space Administration (NASA), brings together international expertise in advanced manufacturing technologies (e.g. materials and processes) and space for the first time.
To bundle competences in the field of 3D printing for aerospace applications, BAM also supports the formation of the Aero+Space working group of the Mobility goes Additive (MGA) network. Patron of the Aero+Space Working Group is the Technical University of Berlin. The working group connects industry and research groups to define mutual requirements and carry out joint projects, e.g. in the field of materials, processes or qualification and standards.