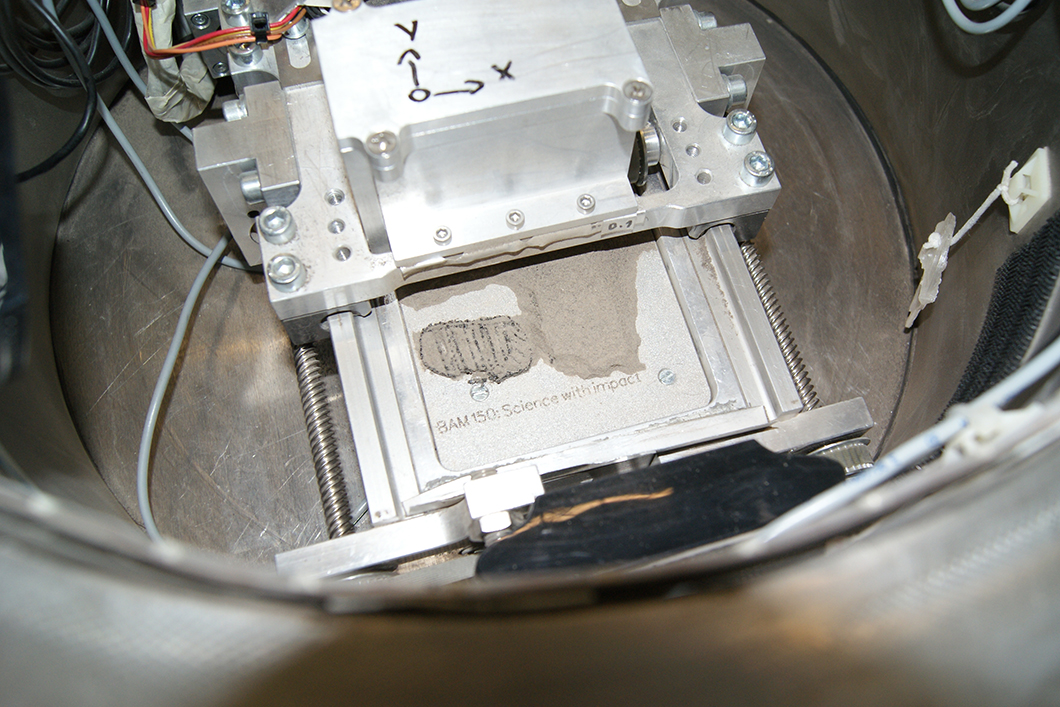
A big step for 3D printing - researchers print Neil Armstrong's famous footprint from lunar dust simulant during a parabolic flight
Source: BAM
Every gram and every centimetre counts on space missions - but how do you know at the launch which equipment will be needed later in space? Together with the Clausthal University of Technology, the Bundesanstalt für Materialforschung und -prüfung (BAM) is researching the possibility of using additive manufacturing to produce components, spare parts or tools in weightlessness. The scientists have now succeeded for the first time in printing under different gravitational conditions with material that would be available on site: simulated lunar dust. In the process, they have also reproduced a famous object from space history.
[Caption: A big step for 3D printing - researchers print Neil Armstrong's famous footprint from simulated moon dust during a parabolic flight. Source: BAM]
Additive manufacturing, also known as 3D printing, offers a wide range of possibilities for producing components from liquid, powder or filamentary starting materials. Powder bed processes (selective laser sintering) are among the most widely used and already the most developed industrial processes. In principle, metals, plastics and ceramics, but also composite materials are available as powders. All in all, additive manufacturing can be used to produce a large number of components or tools "ready to use" very flexibly and quickly, but above all directly at the respective location. Therefore, the technology also has great potential in space travel: e.g. in space stations in Earth orbit or for future moon or Mars missions.
The challenge, however, is to carry out powder-based additive manufacturing independently of gravitational forces. A team from BAM and TU Clausthal already developed an innovative process for this in 2017: In order to be able to process the dry powder, a continuous gas flow is established through the powder bed. This creates a flow field that attracts the particles of the powder - independently of gravity - towards the building platform. In order to be able to test this process under real conditions, BAM regularly takes part in parabolic flights of the German Aerospace Centre (DLR) and the European Space Agency (ESA), where different gravitational conditions are simulated.
"If it were possible to enable additive manufacturing under different gravitational conditions, the most that would have to be transported to the space station in addition to the printer would be the material, e.g. powder - and not a whole assortment of tools and spare parts. Especially for future Mars missions, nothing could be 'sent behind' because of the long distance: Being able to print a required part yourself on site therefore means maximum flexibility," explains Prof. Dr Jens Günster, expert for additive manufacturing processes at BAM and Chair of Advanced Ceramics at TU Clausthal.
During this year's parabolic flight experiments, Günster and his team tested the developed devices and processes under gravitational conditions such as those found on the moon and Mars. In addition to experiments with metallic powder, 3D printing with simulated lunar dust (lunar regolith simulant) was also tested for the first time. "The tests showed that the process works fundamentally not only in complete weightlessness, but also under different gravitational conditions and with different starting materials," Günster explains. "We were able to print small spanners from metallic powder. Also we used lunar regolith simulant under lunar and Martian gravitational conditions to create an object resembling the famous footprint Neil Armstrong left on the moon in 1969."
As part of the DLR-funded project "Powder-based additive manufacturing under reduced gravity conditions", the equipment used will be continuously adapted to different gravitational conditions. The use of materials in situ, so-called "In-Situ Resource Utilisation" (ISRU), would allow additional flexibility for future space missions. In another project funded by ESA, the large-scale sintering of lunar dust simulant is being investigated - in cooperation with the Clausthal University of Technology.