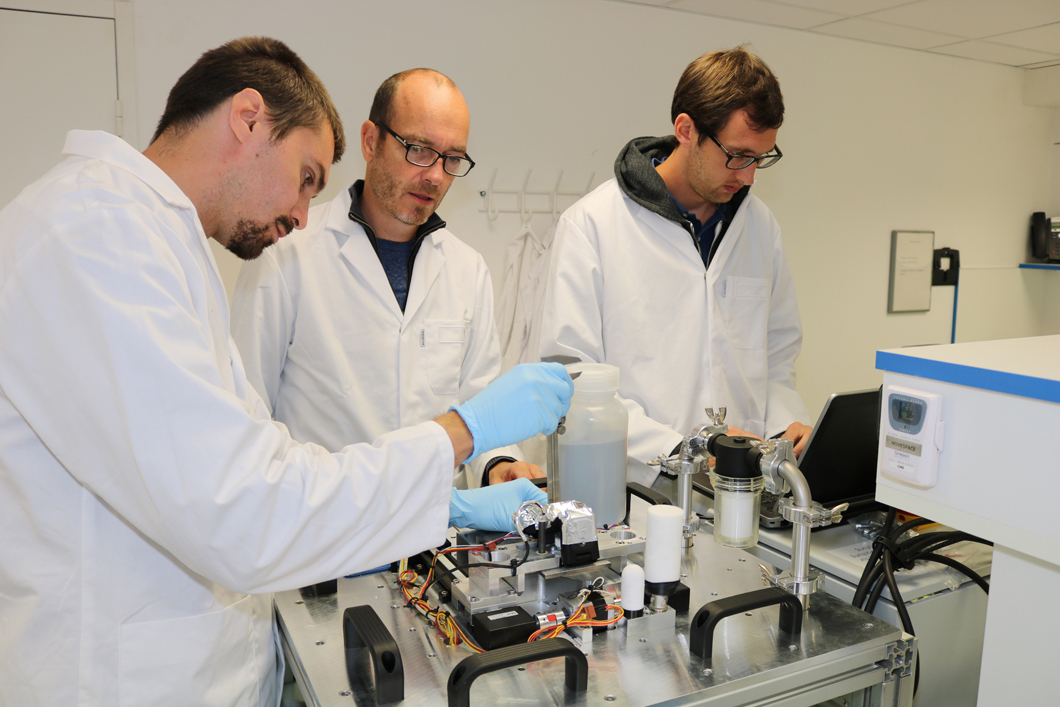
The team of Prof. Dr. Jens Günster, Head of Division Ceramic Processing and Biomaterials, and high-performance ceramics professor at the Clausthal University of Technology will be carrying out tests on additive manufacture under microgravity conditions.
Source: BAM, Section Corporate Communications
Research in zero gravity: The team of Prof. Jens Günster, head of the Ceramic Processing and Biomaterials division and high-performance ceramics professor at the Clausthal University of Technology will be carrying out tests on additive manufacturing under microgravity conditions. In addition to Prof. Günster, Dr. Andrea Zocca, also from the Ceramic Processing and Biomaterials division, Ph.D. students Jörg Lüchtenborg and Pedro Lima will attend the on-site tests. Clausthal University of Technology Ph.D. student Thomas Mühler and DLR Ph.D. student Marc Sparenberg will also take part in the flights. This is another milestone in the successful collaboration between BAM, DLR and Clausthal University of Technology following the "Self-assembled Multifunctional Structures for Adaptive High-Performance Lightweight Construction" Ph.D. programme, which was approved last year.
3D printing has never been explored in weightlessness – BAM, DLR and Clausthal University of Technology are pioneers.
Prof. Dr. Günster: What are you testing in zero gravity?
The "Powder-based additive manufacturing in zero gravity" project produces components by applying layers of a flowable powder using 3D printing. The production is based on data models; in this case, powder is shaped using binder jetting, i.e. injection of a liquid binder, comparable to the well-known 3D printing process. What is new, however, is that the process gas (in this case air) is sucked through the powder layers (gas-flow-assisted powder deposition) so that the powder bed can be stabilised without gravity.
Some of the methods used here have already been patented internationally: they are based on two patent families that have been jointly patented by BAM and Clausthal University of Technology within Germany and by BAM alone outside Germany.
BAM and Clausthal University of Technology are contributing their many years of experience in process development in additive manufacturing, i.e. process technology. As a third partner, DLR provides guidance towards space travel.
What do you want to achieve with the project?
Aerospace engineering is an important research area in Germany. ISS (International Space Station) and similar projects help to train people for longer stays in space. A safe supply of spare parts, tools and components for tests, and not least the life aboard a space shuttle, is necessary for long missions to the Moon and Mars.
BAM, DLR and Clausthal University of Technology are making an important contribution to the establishment and further development of strategies based on the individual manufacturing of relevant components during space missions using additive manufacturing. 3D printing in space will enable astronauts to produce their own tools, saving space and providing maximum flexibility. 3D printing has never been explored in zero gravity – BAM, DLR and Clausthal University of Technology are pioneers. However, the process of gas-assisted powder deposition is also of great interest for industrial applications on Earth. A higher packing density of the powder particles and an improved layer application of finer, non-flowable powders are two major advantages compared to conventional layer application methods.
How do you prepare yourself for the experiments in zero gravity? What technical equipment is on board? And how do you prevent the powder from floating around in weightlessness?
A test facility has been constructed for the test which can map the gas-flow-assisted powder deposition as a process and meets the extreme safety requirements in an aircraft and during parabolic flights. For instance, very high mechanical stability that withstands nine times the acceleration due to gravity is required. To prevent the powder from escaping the facility under, the layer application process must take place in a hermetically sealed double enclosure. A gas flow through the powder towards the building platform ensures the powder is trapped and produces a defect-free layer application.
Why precisely a parabolic flight? One could use other options such as a drop tower or a rocket for tests in zero gravity...
NASA launched the ‘printed in space’ campaign several years ago. Here, fine plastic filaments were extruded into larger components using an established additive manufacturing method. Although the quality of the components is not good, this ISS experiment generated many headlines. We are planning similar tests and the DLR parabolic flight is a first step in this direction where we have about 45 minutes of weightlessness available in 120 parabolic flights within the 30th campaign. No other test platform can achieve that.
Background
Parabolic flights are used for scientific tests in microgravity and for testing space techniques. A DLR parabolic flight campaign usually consists of three flight days, each with four flight hours and 31 parabolas being flown in each. In parabolic flights, an aircraft rises steeply from the horizontal flight, throttles the thrust of the turbines and flies a parabola where weightlessness prevails for about 22 seconds. In total, approximately 35 minutes of weightlessness are available in a flight campaign – alternating with normal and double acceleration due to gravity, which researchers can use for their tests. Up to 40 scientists can participate in a flight, where generally 12 to 13 on-board experiments take place.