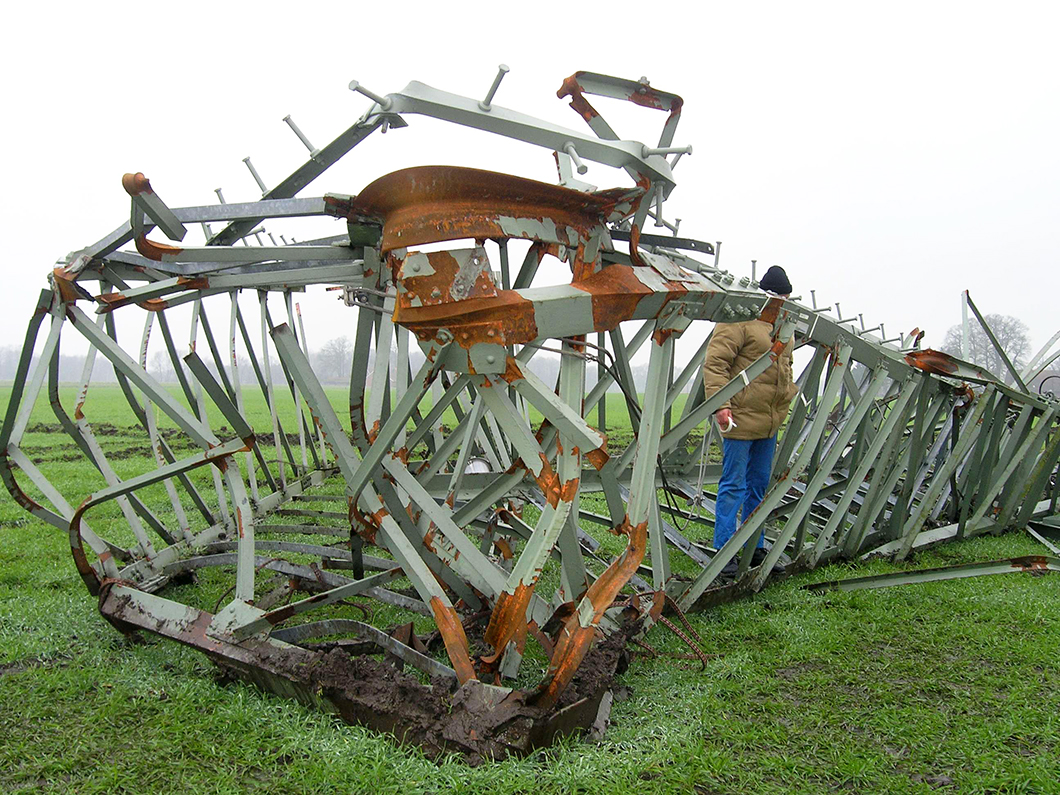
Investigation of a fallen electricity pylon, Münsterland 2005
Source: BAM
What practical examples can you tell us about?
Christian Klinger: We are not allowed to give exact details as most projects involve sensitive information and data that are subject to confidentiality. However, our costomers allowed us to talk about some older cases of failure analysis today. For example, the investigation of the downed electricity pylons in Münsterland was very exciting: In November 2005, ice and snow loads caused a large-scale disruption of the electricity supply network there, triggered by a total of 82 damaged electricity pylons. 250,000 people were without electricity, some of them for up to 50 hours. BAM prepared an expert report on the damaged pylons. The result: The combination of the weather-related high additional loads on one side and the brittleness of the Thomas steel led to the failure of the pole that caused the damage. In the following years, thousands of old pylons made of Thomas steel were replaced and the regulations for electricity pylons were changed.
Another spectacular case of failure happened in June 2008: At that time, one of the 32 wheelset shafts of the ICE 518 broke, which then derailed when leaving the Cologne main station. BAM carried out a failure analysis and found non-metallic inclusions in the wheelset shaft that could trigger fatigue cracks. The supervisory authority, the Federal Railway Authority, shortened the intervals for the ultrasonic inspection of all ICE 3 wheelset shafts from 300,000 to 60,000 and in some cases even 30,000 kilometres of mileage. In the end, all wheelset shafts were exchanged for ones with a larger diameter and different material.
In 2012, we were bound to secrecy when we investigated the causes of the explosion of the natural gas pressure tank of a motor vehicle. The tank had exploded during a refuelling operation. As a result of our investigations, the automotive industry made design changes. The tanks are now easier to access and any potential damage is easier visible. Since then, signs of the beginning of corrosion processes can be detected in time during technical inspections and affected pressure vessels can be removed.