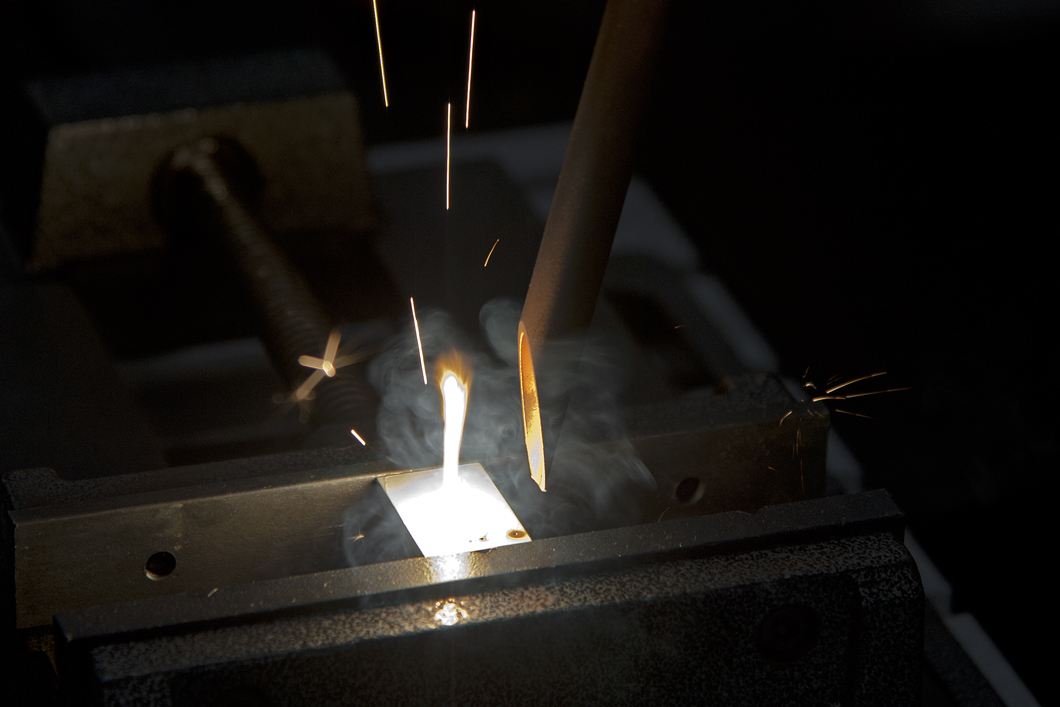
Oberflächenstrukturierung mittels Laserimplantation führt zu signifikanter Härtesteigerung und Verschleißfestigkeit z. B. an verschleißgefährdeten Werkzeugen.
Quelle: BAM
Mithilfe von an der BAM entwickelten Verfahren könnte es zu weitreichenden Veränderungen in Füge-und Umformtechnik kommen. Ein interdisziplinäres Team konzipierte eine Pulslaser-Präzisionsanlage für innovative Schweiß- und Strukturierungsverfahren, die den Herausforderungen neuer Materialien gewachsen sind.
Die Zukunft des Schweißens
Wie sieht die Zukunft des Schweißens aus? Im Fachbereich Schweißtechnische Fertigungsverfahren beschäftigt sich eine interdisziplinäre Arbeitsgruppe mit dem Namen „Verfahren und Technologien für hochbeanspruchte Schweißverbindungen“ unter der Leitung von Prof. Dr. Kai Hilgenberg mit dieser Frage. Er ist als Juniorprofessor an der TU Berlin und zudem an der BAM im Fachbereich Schweißtechnische Fertigungsverfahren tätig.
„Der fortschreitende Trend zur Mischbauweise im Karosseriebau und der Einsatz neuer Materialien stellen die konventionellen Schweiß- und Umformverfahren zunehmend auf die Probe. Neuere hoch- und höchstfeste Materialien können momentan nur unter erheblichem Aufwand gefügt werden. Das führt teilweise zur deutlichen Verschlechterung der Verbindungseigenschaften. Außerdem sind die Umformungsverfahren so aufwendig, dass sie erhebliche Standzeitverkürzungen der Umformwerkzeuge zur Folge haben. Maßnahmen, die dem Verschleiß dieser Werkzeuge vorbeugen, sind daher dringend notwendig“, erklärt Hilgenberg den Ausgangspunkt seiner Arbeit. Erste Forschungsergebnisse liefern vielversprechende Anhaltspunkte: Mithilfe der Pulslaser-Präzisionsanlage ist es gelungen, ein ressourcenschonendes Verfahren mit niedrigem lokalisierbaren Energieeintrag zu entwickeln, das Antworten auf fügetechnische Fragestellungen aus dem industriellen Umfeld liefern kann.
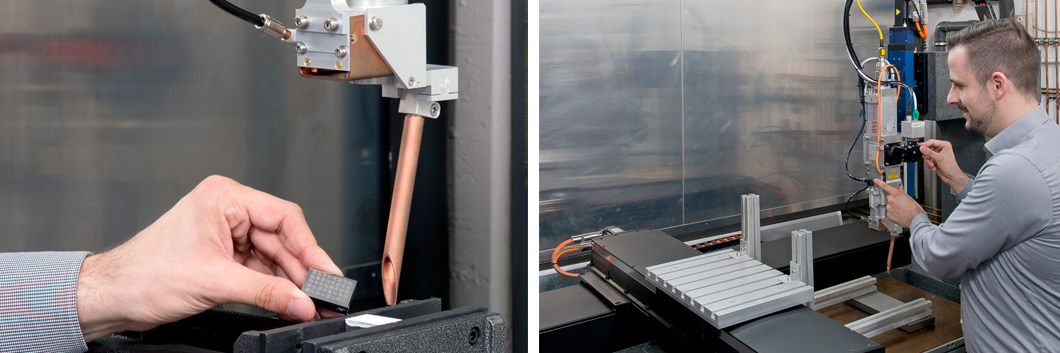
Prof. Dr. Kai Hilgenberg vom Fachbereich Schweißtechnische Fertigungsverfahren zeigt die Vorbereitung für eine Laserimplantation (links) und die elektromagnetische Schmelzbadbeeinflussung beim Laserstrahlschweißen (rechts).
Quelle: BAM
Teamwork im Interesse der Wissenschaft
Die Forschung wird in enger Zusammenarbeit mit dem an der TU Berlin ansässigen Institut für Werkzeugmaschinen und Fabrikbetrieb realisiert. Die Projekte sind beispielhaft für die hervorragenden Kooperationspartnerschaften der BAM mit wissenschaftlich renommierten Institutionen. Insbesondere das Projekt zur Bestimmung des Reibungs- und Verschleißverhaltens laserimplantierter Oberflächen zeigt auf, wie die BAM-interne Vernetzung zu überragenden Forschungsergebnissen und zur Entwicklung innovativer Verfahren beiträgt: „Die Arbeitsgruppe profitiert dabei neben der guten technischen Ausstattung und breiten Expertise an der BAM vor allem von der abteilungsübergreifenden, kollegialen Zusammenarbeit.“, erklärt Hilgenberg.
Die Wissenschaftlerinnen und Wissenschaftler leisten einen wichtigen Beitrag zum Erfolg ihrer Kolleginnen und Kollegen. Die in der Arbeitsgruppe entwickelten Oberflächenstrukturen werden bspw. mit Tribometern aus der Makrotribologie auf ihre Eigenschaften überprüft. In der zerstörungsfreien Prüfung kann die neu entstandene Oberfläche optimal erfasst werden und die Werkstoffanalytik lässt tiefere Einblicke in das Material zu. „Die Umsetzung eines derart komplexen Projektes wird erst durch die wissenschaftliche Zusammenarbeit an der BAM möglich“, betont Hilgenberg.
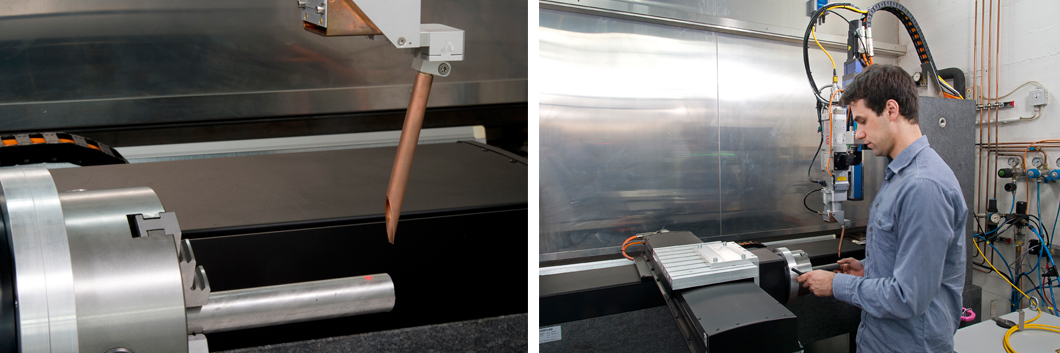
André Fritzsche, ebenfalls im Fachbereich Schweißtechnische Fertigungsverfahren beschäftigt, zeigt die Laserimplantation an rotationssymetrischen Körpern.
Quelle: BAM
Nur ein Beispiel von vielen: Oberflächenstrukturen durch Pulslaser präzise formen
Felix Spranger arbeitet an seiner Doktorarbeit im Fachbereich Schweißtechnische Fertigungsverfahren und nutzt die Anlage im Rahmen des Projektes „Reibungs- und Verschleißverhalten laserimplantierter Oberflächen“ für seine Forschung. In seiner Dissertation erforscht er ein Laserimplantationsverfahren, das zur Verbesserung von hochbeanspruchten Umformwerkzeugen zur Bearbeitung von Metall dient und daher besonders für große Stahlhersteller und die Automobilindustrie extrem interessant ist.
Spranger nutzt für seine Forschung gepulste Laserstrahlung zum gezielten Einschmelzen von keramischen Hartstoffpartikeln in metallische Grundstoffe. Auf eine metallische Grundfläche wird dazu eine Schicht aus keramischen Hartstoffpartikeln aufgetragen. Im Anschluss nutzt der Wissenschaftler einen gepulsten Faserlaser, um die Grundfläche punktuell innerhalb weniger Millisekunden auf über 1500 °C zu erhitzen. Bei diesen Temperaturen schmilzt der metallische Grundstoff während die keramischen Hartstoffpartikel intakt bleiben. Die Partikel werden in der Schmelze eingebunden, die nach dem Auskühlen wieder verhärtet und eine positive Oberflächenstruktur auf dem Metallteil hinterlässt. Was unter dem Mikroskop aussieht wie eine Hügellandschaft, sind hochfeste Metall-Matrix-Composite-Implants, die aus der Metallplatte herausragen und extrem hart sind.
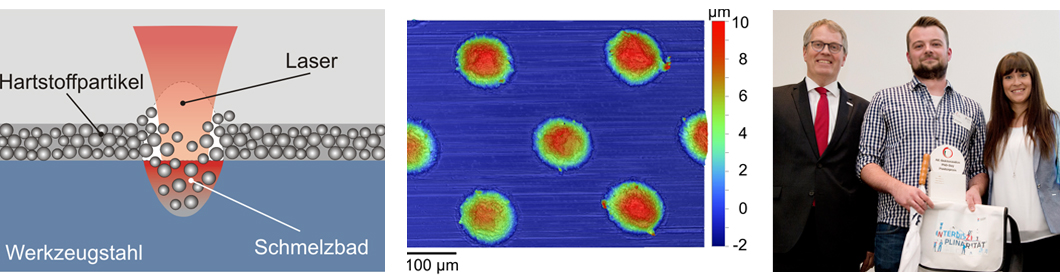
Abbildung 1 (links): Laserimplantation; Abbildung 2 (mitte): Resultierende Oberflächentopologie; Felix Spranger (Bild rechts, 2.v.r.) erhielt für sein Projekt-Poster im Herbst 2017 den BAM-internen Posterpreis.
Quelle: BAM und Fachbereich Schweißtechnische Fertigungsverfahren (Abbildungen 1 und 2)
Die erste Hälfte des drei Jahre andauernden Projektes ist vorbei und die theoretischen Grundlagen sind bereits gut erforscht. Nun gilt es, weitere Erkenntnisse zur Umsetzung zu gewinnen. Derart veränderte Werkzeugoberflächen sollen einen Beitrag zur Gestaltung ressourcenschonender und sicherer Fertigungsprozesse liefern. Es wird erwartet, dass durch eine gezielte Oberflächenstrukturierung das Reibverhalten optimiert und damit der Verschleiß signifikant reduziert werden können.
In der freien Wirtschaft zählt das Tempo
Damit das Verfahren unter industrienahen Umständen getestet werden kann, braucht die BAM Partner aus der freien Wirtschaft. Für den industriellen Einsatz muss die Pulslaser-Präzisionsanlage allerdings noch modifiziert werden. In der derzeitigen Phase der Forschung müssen genaue Daten erhoben werden, um die Forschung auf eine valide Basis zu stellen. So wie sie im Moment konzipiert ist, arbeitet die Pulslaser-Präzisionsanlage sehr präzise, aber nicht sehr schnell. „Beim Einsatz in der freien Wirtschaft gibt es gewisse Toleranzgrenzen, innerhalb derer die Ergebnisse variieren dürfen. Dafür zählt eher das Tempo und damit die Rentabilität“, erklärt Hilgenberg. Zuversichtlich, dass das neue Verfahren Anwendung in der Industrie findet, zeigt er sich dennoch: „Es gibt bereits Anfragen von zwei großen Firmen“, verrät er.