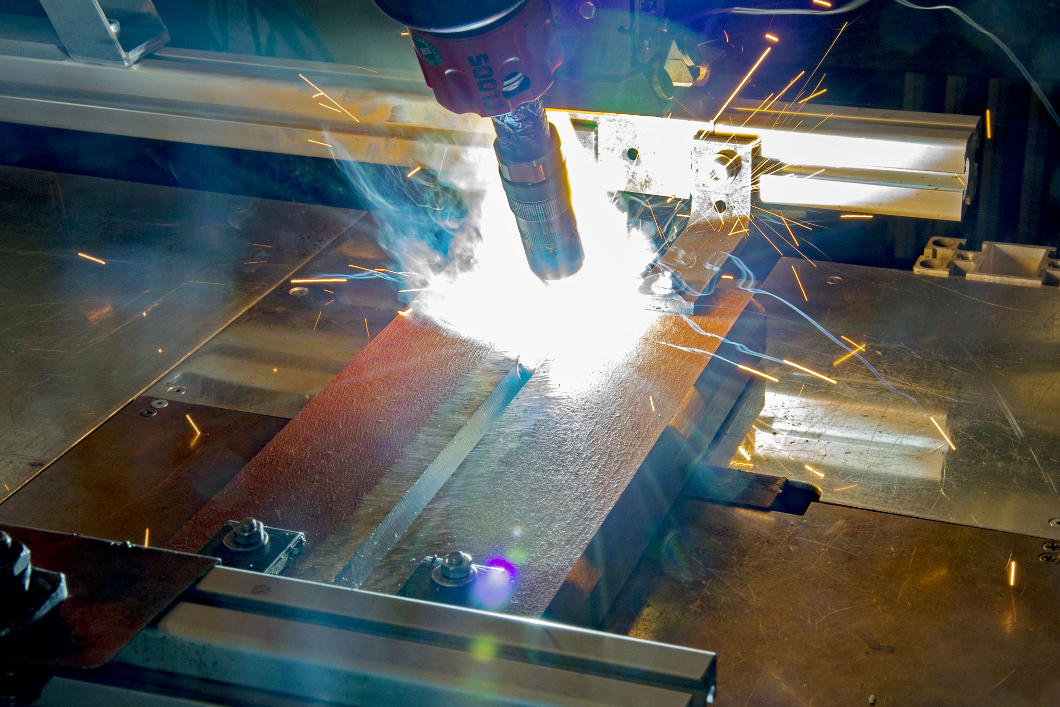
Für dicke Bleche geeignet: Laser-Hybridschweißverfahren mit elektromagnetischer Schmelzbadunterstützung
Quelle: BAM
Offshore-Windkraftanlagen zählen zu den wichtigsten Zukunftstechnologien. Doch für den Bau von Windrädern und anderen großen Industrieanlagen aus Metall sind tausende Schweißnähte nötig. Der BAM ist es gelungen, ein Verfahren zu verbessern, mit dem nun besonders dicke Metallbleche verarbeitet werden können. Mit dieser Idee können die Hersteller von Windparks, Kreuzfahrtschiffen, Pipelines, Turbinen und viele andere Anwender in der Industrie viel Zeit und Geld sparen.
Das Schweißen gehört zu den ältesten Techniken, die der Mensch entwickelt hat, um zwei Metallstücke miteinander fest zu verbinden. Doch je dicker die Bleche werden, desto schwieriger lassen sie sich verarbeiten. "Wir haben eine Methode entwickelt, mit der bis zu 30 Millimeter dicke Bleche in einem einzigen Arbeitsgang geschweißt werden können", sagt Dr. Andrey Gumenyuk. Ein Erfolg, der weltweit auf großes Interesse stößt.
Mit Laserstrahl und Lichtbogen
Das Team der BAM greift dabei auf eine erprobte Technologie zurück: das Laser-Hybrid-Schweißen. "Dieser kombinierte Einsatz von Laserstrahl und Lichtbogen hat sich seit Jahrzehnten bewährt, weil Roboter die Schweißnähte schnell erstellen können und nur wenig Nacharbeiten nötig werden", erklärt der Wissenschaftler. Im Automobilbau lag die erste große industrielle Anwendung bei Blechen mit ein bis drei Millimeter Stärke. Anfang der 2000er Jahre zogen dann die Werften für den Schiffbau nach, die meist zehn Millimeter dicke Metallteile verarbeiten.
Doch wenn die Bleche noch dicker werden, dringt die Energie des Schweißgerätes nicht mehr tief genug in das Material ein. "Wanddicken ab zehn Millimeter sind mit konventionellen Schweißverfahren nicht mehr in einem Durchgang schweißbar", erklärt Gumenyuk. Bisher versehen Anlagenbauer die Bleche, die verbunden werden sollen, daher mit einer V-förmigen Fuge, damit das Schweißgerät auch die tiefste Stelle erreichen kann. Dann werden die Bleche in mehreren Durchgängen zusammengeschweißt. Diese Mehrlagentechnik ist extrem zeitaufwendig und verursacht hohe Kosten, weil die Fuge mit teuren Zusatzmaterialien gefüllt werden muss.
"Dank unserer Entwicklung reicht jetzt ein einziger Schweißvorgang", erklärt der Ingenieur. Mit einem stärkeren Laserstrahl wird eine schmale, tiefe Schmelzzone erzeugt, die das gesamte Metall durchdringt. So lassen sich die Bleche gradkantig verschweißen. "Dafür müssen wir höhere Laser-Leistungen als allgemein üblich einsetzen", erklärt Gumenyuk. Die BAM arbeitet daher seit zehn Jahren mit einen 20-Kilowatt-Laser.
Die Idee: Langsamer Schweißen mit Hilfe eines Magneten
"Mit unserem Verfahren erzeugen wir über die gesamte Blechdicke von 20 Millimetern und mehr einen schmelzflüssigen Bereich", erklärt der Ingenieur. Das hat allerdings auch Nachteile, denn die Abkühlungsbedingungen in der Schweißzone reduzieren die Zähigkeit des Materials. Zudem versucht die flüssige Metallsäule nach unten zu entweichen. Die entscheidende Idee: Ein Elektromagnet unterhalb des Bleches generiert im Metall elektromagnetische Kräfte, die in der Schweißzone einen Stützeffekt erzeugen. "So können wir langsamer schweißen und die Schweißverbindungen erreichen die geforderte mechanische Festigkeit und Zähigkeit", sagt der Wissenschaftler. So ist es Gumenyuk und seinem Team gelungen, die bisherige Begrenzung für die Anwendung des Laser-Hybrid-Schweißens von zehn Millimetern schrittweise in Richtung 30 Millimeter zu verschieben. Dabei profitieren sie von dem Know-how, das die BAM auf diesem Forschungsgebiet seit über drei Jahrzehnten angesammelt hat.
Mangelhaft ausgeführte Schweißarbeiten können zu schweren Unfällen führen und technische Anlagen dauerhaft außer Gefecht setzen. "Das kombinierte System, das wir jetzt für Dickblech-Anwendungen einsetzen, entwickeln wir an der BAM bereits seit 2007", erzählt Prof. Dr. Michael Rethmeier, Leiter des Fachbereichs Schweißtechnische Fertigungsverfahren. "Wir werden an den Anforderungen der Anwender gemessen und müssen eine Reihe von Qualitätsnormen erfüllen, sonst könnte man das neue Verfahren nicht in der Industrie und im Anlagenbau einsetzen", so Rethmeier.
Revolution für Offshore-Windparks?
Zwei Aspekte sind besonders interessant für die zukünftigen Anwender: "Wir schweißen auch Speziallegierungen auf der Basis von Nickel oder Titan, die beispielsweise für den Bau von Turbinen eingesetzt werden", sagt Gumenyuk. Und trotz ihrer Leistungsfähigkeit bleibt die neue Schweißtechnik voll automatisiert in verschiedenen Positionen mobil einsetzbar. Das ist beispielsweise bei der Verlegung von Rohrleitungen interessant, bei der ein Schweißroboter für eine Rundnaht das Rohr umkreisen muss.
Für Offshore-Windparks könnte die Technologie zudem eine kleine Revolution auslösen. Für den Aufbau der Sockel- und Turm-Elemente sowie der unterstützenden Strukturen der Windenergieanlagen werden Bleche verarbeitet, die zum Teil über 80 Millimeter dick sind. Das mehrlagige Schweißen dauert dabei für eine einzige Schweißverbindung mehrere Stunden oder gar Tage. Mit dem Verfahren der BAM geht das deutlich schneller und kostengünstiger. So kann das neue Schweißverfahren sogar einen wichtigen Beitrag zur Energiewende liefern.