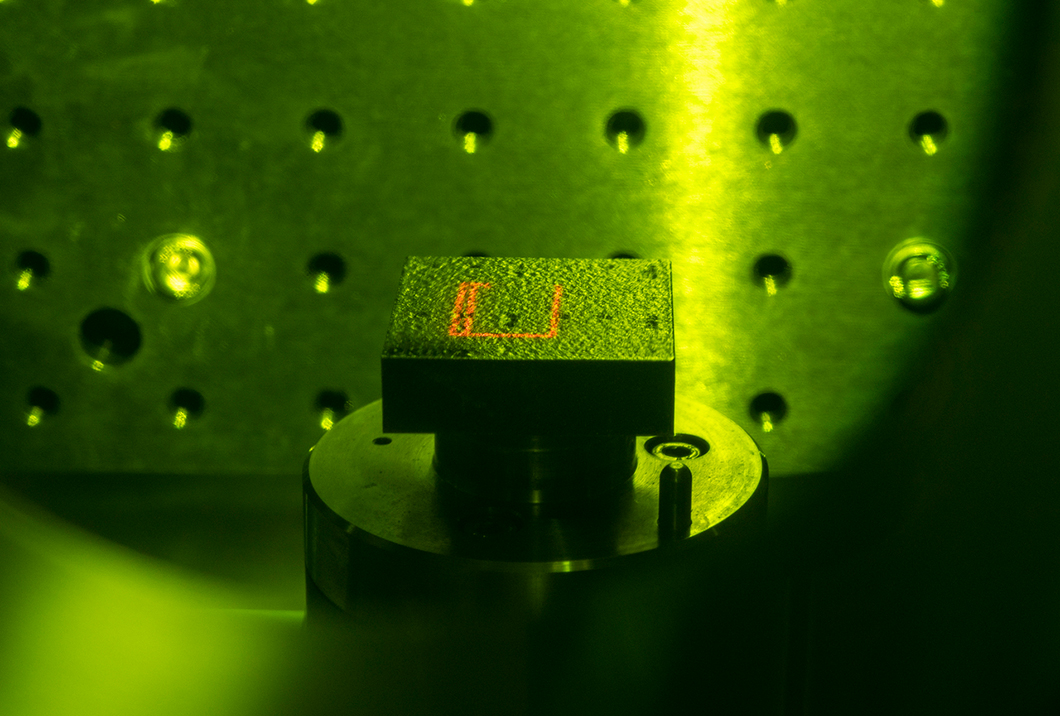
Mit Laserthermografie lassen sich Risse in einem additiv gefertigten Bauteil exakt lokalisieren.
Quelle: BAM
Die additive Fertigung metallischer Bauteile für sicherheitsrelevante Bereiche erfordert hohe Qualität. Schon kleinste Fehler können schwerwiegende Folgen haben. Die BAM entwickelt zusammen mit der ThetaScan GmbH ein Überwachungssystem, das Risse bereits während des 3-D-Drucks in Echtzeit erfasst.
Additiv gefertigte Komponenten werden aktuell erst nach dem Fertigungsprozess auf ihre Qualität überprüft. Zum Einsatz kommt dabei zumeist die Computertomografie, mit der zerstörungsfrei festgestellt werden kann, ob das Bauteil Poren oder andere Fehlstellen aufweist. Ein schadhaftes Bauteil wird verworfen und der Druckprozess – der manchmal mehrere Tage dauert – muss von Neuem gestartet werden. Das macht die additive Fertigung metallischer Bauteile für Unternehmen im Zweifel kosten- und zeitintensiver – und damit oft unwirtschaftlich.
„Besser wäre es, mögliche Defekte noch während des Druckens zu erkennen, um den Prozess rechtzeitig abbrechen oder korrigierend eingreifen zu können“, erklärt Tina Becker, BAM-Expertin für In-situ-Monitoringverfahren bei der additiven Fertigung. „Bislang ist das nicht möglich, weil handelsübliche 3-D-Drucker diese Funktion nicht vorsehen. Zudem verfügen kleine und mittlere Unternehmen gar nicht über die Kapazitäten, um selbst eine entsprechende Prozessüberwachung zu entwickeln und sie in einen vorhandenen 3-D-Drucker zu integrieren.“
Ein zweistufiges Verfahren erkennt Risse sofort
Die BAM hingegen besitzt langjährige Erfahrung mit zahlreichen Methoden der zerstörungsfreien Prüfung, auch im Bereich der additiven Fertigung. Neben der Computertomografie kommen etwa kamerabasierte Systeme und Wirbelstromsensoren zum Einsatz. Jetzt entwickelt die BAM zusammen mit dem Projektpartner ThetaScan GmbH, einem auf Werkstoff- und Prüftechnologie für die Luft- und Raumfahrt sowie die Automobil- und Kraftwerksindustrie spezialisierten Unternehmen, ein In-situ-Überwachungssystem für den 3-D-Druck im Laser-Pulverbett-Verfahren.
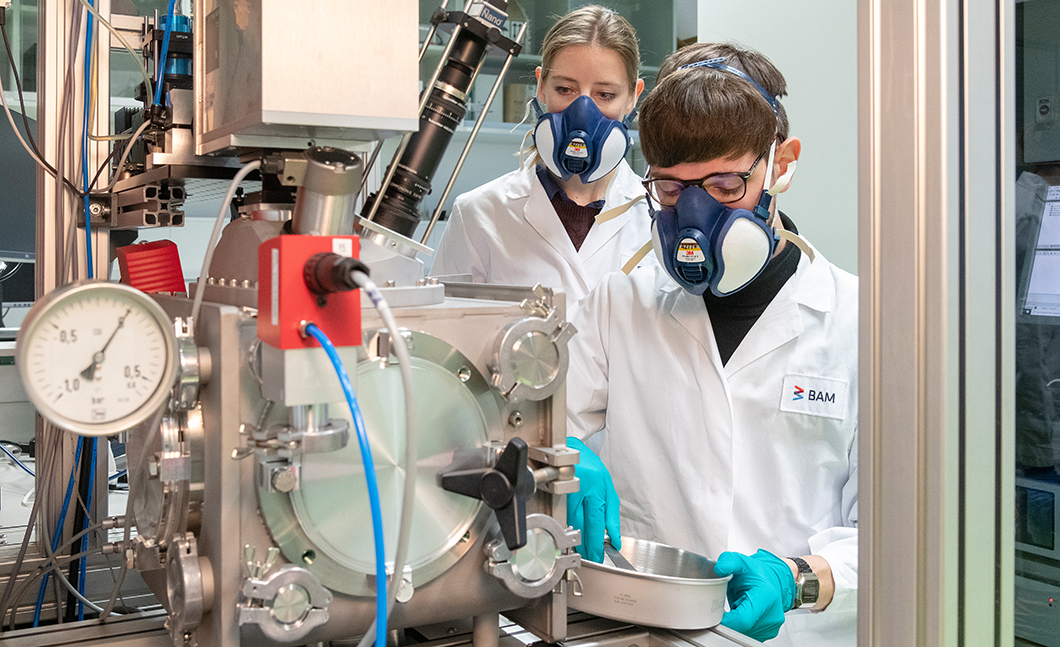
Philipp Breese und Tina Becker befüllen den 3-D-Drucker mit metallischem Pulver.
Quelle: BAM
„Um Defekte rechtzeitig zu erkennen, setzen wir auf einen zweistufigen Prozess“, so Beckers Kollege Philipp Breese. „Bereits während der additiven Fertigung wird jede Schicht des entstehenden Bauteils mit optimierter, d. h. hochauflösender optischer Tomografie auf Fehler untersucht. So können wir mögliche Defekte, z.B. Poren oder Delaminationen, frühzeitig identifizieren und sie für eine zweite Prüfung mit Laserthermografie auswählen. Das zweite Verfahren erlaubt uns dann auch die präzise Lokalisierung von Erstarrungsrissen in der ausgekühlten Schicht.“
3-D-Druck wird wirtschaftlich
Der Vorteil: Durch die Kombination beider Verfahren können Defekte erstmals noch während des laufenden Prozesses festgestellt werden – der zusätzliche Zeitaufwand ist überschaubar. Sind die Defekte zu gravierend, kann der Druckprozess unmittelbar abgebrochen werden. „Das erhöht die Sicherheit der gefertigten Bauteile und die Wirtschaftlichkeit des additiven Fertigungsprozesses“, erklärt Tina Becker. „Mit den von uns entwickelten Prüfsystemen, die erstmalig Risse in situ erkennen können, wird die Qualitätssicherung additiv gefertigter Bauteile effizienter und so der 3-D-Druck insgesamt für kleine und mittlere Unternehmen interessant. Die ThetaScan GmbH steht bereits im Austausch mit Unternehmen, um das System in bestehende und neue Anlagen zu integrieren.“
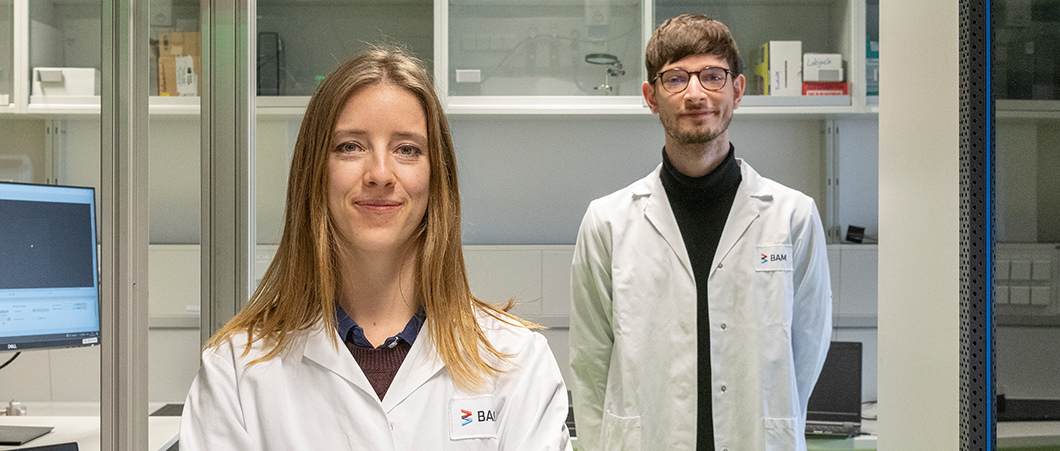
Tina Becker und Philipp Breese
Quelle: BAM