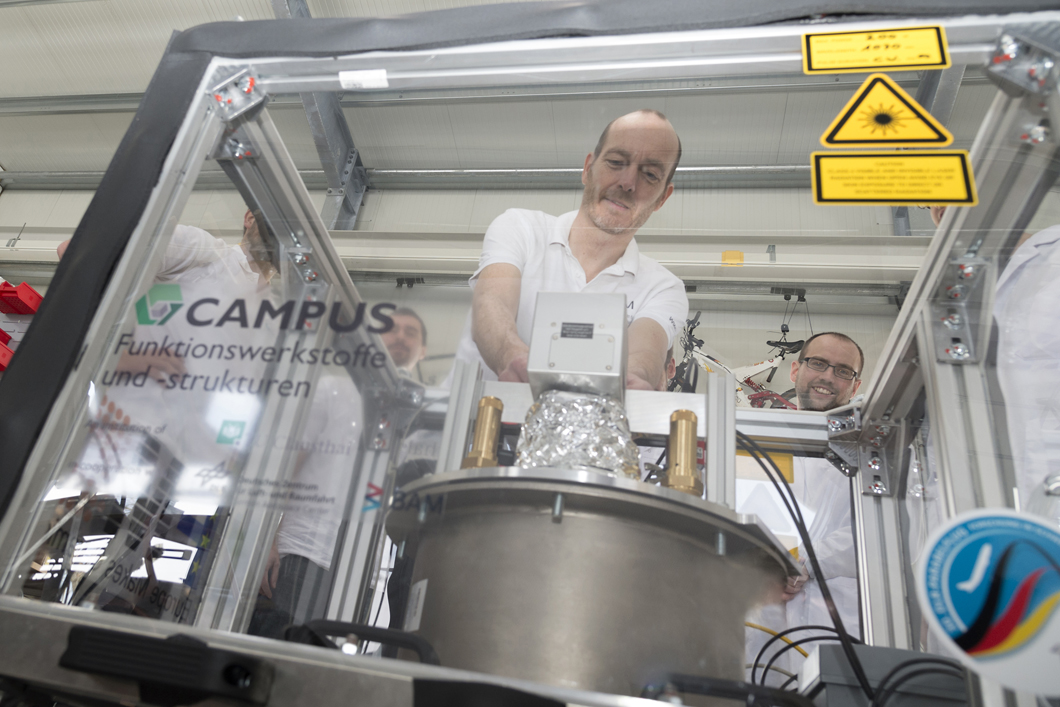
Das Team um Prof. Jens Günster prüft die Strahlenschmelzanlage zur additiven Fertigung. Erstmals wird mit metallischen Pulvern experimentiert.
Quelle: BAM
Forschen in der Schwerelosigkeit: Das Team von Prof. Dr. Jens Günster, Leiter des Fachbereiches Keramische Prozesstechnik und Biowerkstoffe und zugleich Professor für Hochleistungskeramik an der TU Clausthal führt Experimente zur additiven Fertigung unter Microgravity-Bedingungen durch. Ziel ist es, Komponenten aus Edelstahl wie zum Beispiel Werkzeuge im Space herstellen zu können.
Neben Prof. Günster sind Dr. Andrea Zocca, Jörg Lüchtenborg und Pedro Lima sowie Gunther Mohr vom Fachbereich Schweißtechnische Fertigungsverfahren beteiligt. Ergänzt wird das Team um Dr.-Ing. Thomas Mühler von der TU Clausthal und Marc Sparenberg, Doktorand am DLR Institut für Faserverbundleichtbau und Adaptronik in Braunschweig. Im September 2017 konnte das Team erstmalig in "echter" Schwerelosigkeit im Rahmen der 30. Parabelflugkampagne des DLR Versuche mit der speziell konstruierten Strahlenschmelzanlage durchführen. Nun folgen weitere, denn das Team konnte sich erneut für einen Platz im Parabelflugzeug qualifizieren. In der Woche vom 5. bis zum 8. März soll ein Schraubenschlüssel aus Metall entstehen.
Wir erwarten, dass erste "ready to use" Komponenten aus Edelstahl unter Mikrogravitation gefertigt werden.
Herr Prof. Dr. Günster: Mit Ihrem Projekt „Pulverbasierte additive Fertigung unter Schwerelosigkeit” haben Sie im letzten Jahr an der Parabelflugkampagne des DLR teilgenommen. Welches Potential von 3D-Druck im Space sehen Sie?
Additive Fertigungsverfahren sind die Zukunft der nachhaltigen Produktion. Im Gegensatz zum Fräsen, Bohren und Erodieren wird Material zu einem Bauteil zusammengeführt und nicht abgetragen. Dadurch wird immer nur so viel Rohstoff verwendet, wie tatsächlich auch gebraucht wird. Diese Verfahren sind auch für die Raumfahrt interessant, um zum Beispiel auf einer Raumstation Bauteile, Komponenten, Ersatzteile oder Werkzeuge nach Bedarf anzufertigen. Es müsste dann nur das Pulver und nicht ein ganzes Bauteilsortiment zur Raumstation transportiert werden. Das spart Material und Gewicht und somit auch Treibstoff für den Weltraumtransport.
Bislang kommt auf der Internationalen Raumstation ISS ein 3D-Drucker zum Einsatz, der ein Filament aus aufgeheiztem Kunststoff Schicht für Schicht aufträgt, um ein dreidimensionales Objekt herzustellen. In diesem Parabelflugexperiment testet ein Konsortium von Wissenschaftlern der BAM, der TU Clausthal und dem DLR Institut für Faserverbundleichtbau und Adaptronik nun auch die industriell sehr erfolgreichen pulverbasierten Fertigungsverfahren auf ihre Eignung für einen Einsatz in Schwerelosigkeit, um ihr großes Potenzial für künftige Weltraummissionen zugänglich zu machen. Hierbei ist wesentlich, dass der Aufbau von Schichten mit dem pulverförmigen Ausgangsmaterial, auch als Feedstock bezeichnet, auch ohne Gravitation funktioniert. Ein Gasstrom durch die Bauplattform und das Pulverbett führt zu einer auf Strömung basierenden Kraftkomponente, die die Schwerkraft ersetzt. Dieses Verfahren ist unter anderem in den USA bereits patentiert.
Während der letzten Parabelflugkampagne gelang es Ihnen, erste Objekte in Schwerelosigkeit zu drucken. Mit welchen Herausforderungen hatten Sie dabei zu kämpfen und was haben Sie bei der zweiten Versuchsreihe vor?
In der ersten Flugkampagne September 2017 wurde als Ausgangsmaterial ein keramisches Pulver verwendet. Dies lag an den erheblichen Sicherheitsauflagen, die der Betreiber der Flüge, die Firma Novespace, vorgibt. Es wäre schon kompliziert eine konventionelle Strahlschmelzanlage in einem Flugzeug zu installieren, aber das neue Verfahren erfordert zusätzlich einen Gasstrom durch die Bauplattform und das Pulverbett. Daher wurde in einem ersten Experiment nicht gleich ein potentiell brennbares oder sogar explosionsgefährliches Metallpulver verwendet sondern ein weitestgehend inertes, also ein sich chemisch träge verhaltendes Keramikpulver.
In dieser für uns ersten Kampagne konnten so wesentliche funktionelle Merkmale des neuen Schichtauftragsverfahrens getestet und sogar erste Bauteile mittels Laserstrahlung gesintert werden. Dazu war die Einstellung einer Schutzgasatmosphäre in einem abgeschlossenen Druckbehälter mit Gaszirkulation zunächst nicht nötig. Dies ist nun genau das Ziel der zweiten Kampagne: Eine zweite Evolutionsstufe der Anlage soll nun das Verarbeiten metallischer Pulver unter Schutzgasatmosphäre ermöglichen. Wir erwarten, dass erste "ready to use" Komponenten aus Edelstahl unter Mikrogravitation gefertigt werden.
Also eine "Evolution" von keramischem zu metallischem Pulver..?
Während wir uns in der ersten Flugkampagne auf keramische Pulver konzentriert haben, liegt nun der Fokus auf den metallischen Werkstoffen. In diesem Zusammenhang kann auf die Expertise von Kollegen aus dem Fachbereich Versuchsanlagen und Prüftechnik zurückgegriffen werden. Der Prozess ist grundsätzlich gleich für keramische und metallische Werkstoffe, jedoch ist das Schmelzverhalten metallischer Werkstoffe deutlich verschieden zu keramischen. Eine im Idealfall vollständige Verdichtung des Pulvers zu einem "ready to use" Bauteil ist nur mit metallischen Werkstoffen im Laserstrahlprozess möglich. Da wir mit einem kontinuierlichen Gasstrom das Pulverbett stabilisieren, ist beim Aufbau auch von Prozessseite einiges neu.
Werden wir ein erstes gedrucktes Metall-Werkzeug sehen können?
Wir haben für unsere zweite Kampagne eine völlig überarbeitete Schichtauftragstechnologie ins Rennen geschickt. Diese muss erst mal zeigen, dass sie für das Auftragen von Schichten unter Bedingungen der Schwerelosigkeit geeignet ist. Dann sollen das erste Mal mit dieser Technologie metallische Werkstoffe verarbeitet werden und zu guter Letzt hoffe ich natürlich, dass ein brauchbares Bauteil gefertigt werden kann. Wir möchten ein Werkzeug, einen kleinen Maulschlüssel, aus der Kampagne mitnehmen.