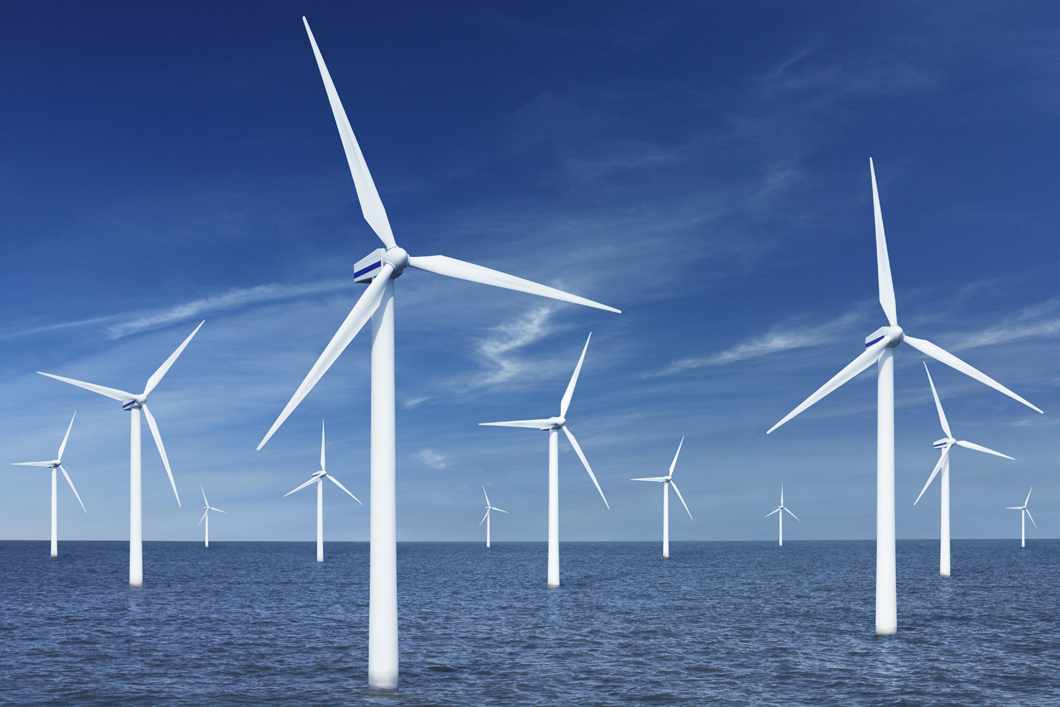
Off shore wind turbines (Digital Composite)
Source: Michael Betts/DigitalVision/Getty Images
Thanks to its more profitable location, offshore wind turbines operate more efficiently than wind turbines on land. However, they are also exposed to greater wind pressure at sea. In addition, high waves and aggressive salt water erode them. BAM is investigating these damage sources and is working on technical solutions and evaluating existing repair concepts.
The construction of offshore wind farms is an important strategic pillar of Germany's energy transition. At the beginning of 2018, 19 wind farms in the North and Baltic Seas were in operation. "The more offshore wind farms that come on stream, the more the focus must be put on their smooth operation," says Dr.-Ing. Matthias Baeßler from BAM’s Buildings and Structures division. He heads the project "Service life extension and service loading fatigue of wind turbines" (LeBeWind), which aims to ensure the economic operation of the installations and minimise the cost of maintenance and repair. Baeßler and his team concentrate on three aspects in particular: grout connections, rotor blades and corrosion protection.
Special mortar against foundation cracks
Grout connections are the joints between the foundation structures, i.e. steel piles or foundations and the components of the wind turbine built on them. The gap between these two components is usually filled with a special mineral mortar, called grout. "This connection is exposed to high mechanical stress due to both static and dynamic loads," explains Baeßler. But even these special mortars do not always withstand the gruelling stress during operation and as a consequence deterioration can occur. BAM therefore developed a crack filler based on a very fine mineral cement. The result is convincing: "The carrying capacity of a repaired grout connection is comparable to an undamaged connection," says Baeßler. However, since previous investigations were performed on dry and not moistened grout compounds, BAM wants to continue the tests in an aqueous environment in the laboratory.
In search of the best repair concept
The over 60 metres long rotor blades are exposed to heavy winds, gale-force gusts and the salty sea air. But despite these extreme natural loads, BAM engineers find that between 70 to 80 percent of the damage to the rotor blades is the result of production faults diverging from the ideal design form. It often happens that damage is seen in the rotor blades long before the theoretically predicted service life of 20 years. The consequences are downtime, costly and expensive repairs on the high seas or even a rotor blade replacement. Since there are currently no uniform repair specifications, BAM is investigating the effects of the concepts used so far and compares them with each other. Finally, the best possible repair concept should be derived from these comparison values. In doing so, BAM scientists use methods and techniques such as thermography, which enable them to efficiently determine the rotor blades’ maintenance and repair requirements.
Research with a view: testing corrosion protection under real conditions
The LeBeWind project also looks into issues of corrosion. "Most affected are steel structures above the waterline," says project head Martin Babutzka. Coatings are therefore the first choice for protection. These are applied early because corrosion-prone components are not only exposed to harmful environmental conditions during operation at sea but also during assembly on land – with the risk that they may be damaged during transport or assembly. In such cases, the duration of protection is dramatically shortened and the coating must be repaired. BAM is therefore working to develop suitable test methods for corrosion protection coatings with a focus on the durability of a repair coating.
The research team is also interested in the under-surface part of offshore wind turbines. Here, microbiological activities or marine growth such as algae and barnacles can influence corrosion. A good way to protect steel underwater is cathodic corrosion protection. In this electrochemical principle, steel materials in the water are protected against corrosion by being connected to a less noble metal such as zinc or cathodically polarised by an external current source. As a result, the less noble metal gradually dissolves i.e. it is ‘sacrificed’ to protect the steel structure.
BAM is planning laboratory tests under real conditions. Martin Babutzka says: "We want to understand the interaction between cathodic corrosion protection and marine growth. Our goal is to ensure permanent corrosion protection for those parts of a wind turbine that are constantly underwater." For this challenging applied research, Babutzka and his team will set up a test laboratory in a container with a seawater supply bypass and move from Berlin to Norderney, a North Sea island. This is research with a view: you can see an offshore wind farm with the naked eye from the northern beach of the island if the weather is nice.