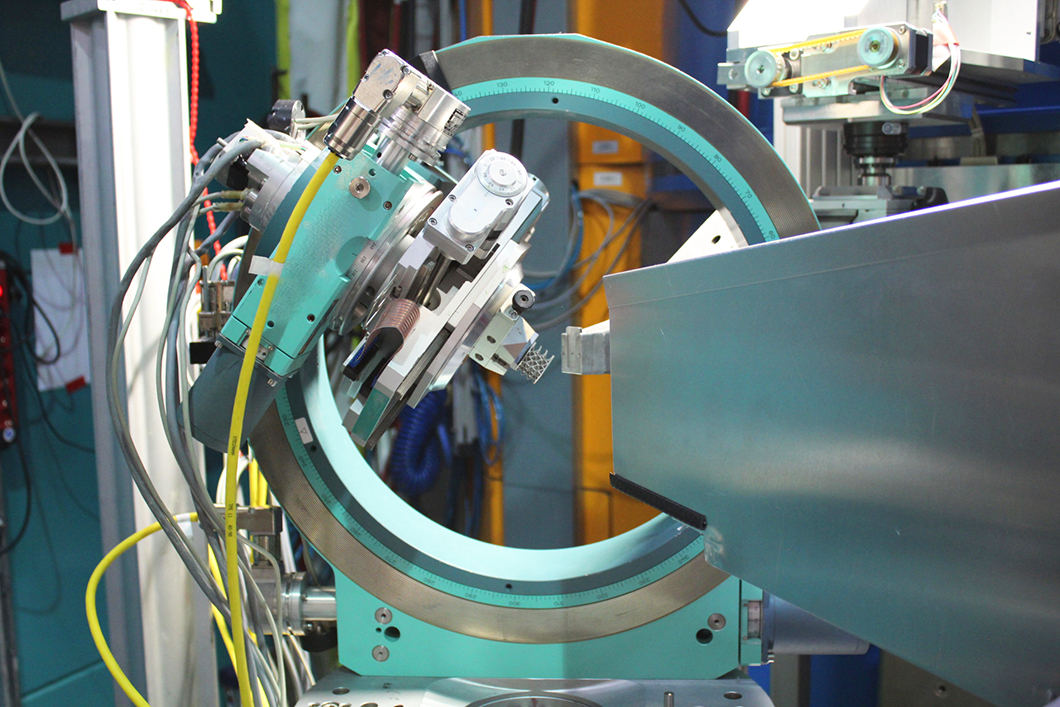
Experimental setup in the neutron source at TU München
Source: BAM
3D printing opens up completely new possibilities, for example in the production of turbine blades. However, the components produced in this way often contain stresses that can later lead to cracks. A team at BAM has now succeeded in measuring these internal stresses non-destructively on complex components - a key to improving production processes.
Gas turbine blades have to withstand harsh environments: In addition to high pressure and enormous centrifugal forces, they are exposed to high temperatures. To further increase the energy yield, they should tolerate temperatures that are actually already above the melting point of the material. This can be achieved with hollow turbine blades that are cooled by an air-flow from within.
Such blades can only be manufactured using Additive Manufacturing: In this process, the component is built up layer by layer from powdery feedstock material by selective melting with a laser. Based on the natural role model of bird bones, filigree lattice structures inside the hollow turbine blades provide the necessary stability.
"Complex components with such filigree structures would be impossible to produce using conventional manufacturing methods such as casting and milling," says Tobias Fritsch, a physicist at the Bundesanstalt für Materialforschung und -prüfung (BAM).
However, the local heat input of the laser and the rapid cooling also create stresses in the material. Until now, the manufacturing companies have eliminated these by subsequent heat treatment. But this costs time and money.
The stresses can be detected by X-rays. But they do not penetrate deep into the component. And they reach their limits with filigree hollow structures due to the geometric complexity.
The team at BAM, which focuses on research into additive manufacturing, had an idea: they decided to bombard objects from the 3D printer with a neutron beam. The beam penetrates deeper and is diffracted by the lattice structure of the atoms in a characteristic way at stressful points.
The BAM team was supported by two important cooperation partners: It was able to use the research neutron source of the Heinz Maier-Leibnitz Centre (FRM II) of the Technical University of Munich for its experiments. And the gas turbine manufacturer Siemens Energy provided an additively manufactured component: a grid structure only a few millimeters in size, printed from a nickel-chromium alloy.
"It was crucial to locate the measuring points as precisely as possible using computed tomography," says Fritsch. "We were able to locate them exactly under bombardment with neutrons and thus also the stresses."
But of course not every company that produces gas turbines has a neutron source. In a next step, the researchers* now want to find out which parameters can lead to stresses during 3D printing. "It will probably be crucial to distribute the heat as evenly as possible during printing," says Tobias Fritsch. The BAM team hopes to soon be able to provide industry with more valuable information on how to improve the quality of energy-efficient gas turbines from the 3D printer.