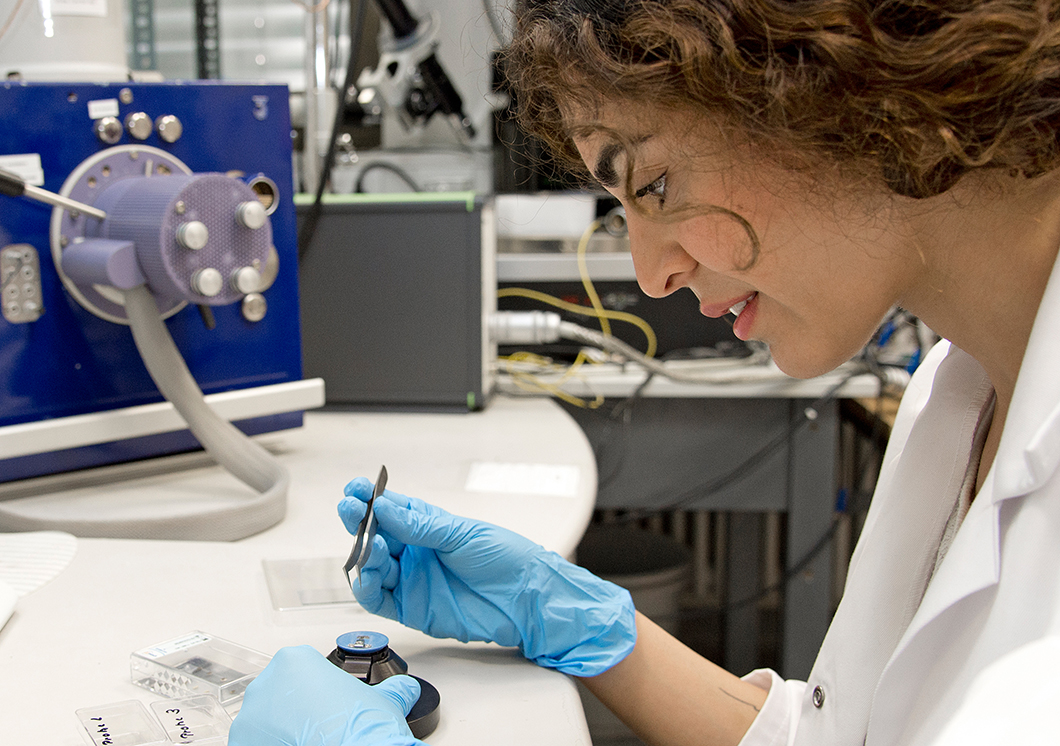
Doktorandin Media Ghasem Zadeh Khorasani bei der Analyse von Nanokompositen mittels Rasterkraftmikroskopie
Quelle: BAM
Kohlefaserverstärkte Kunststoffe sind leichte und stabile Werkstoffe. Sie finden besonders im Schiffsbau, bei Flugzeugkonstruktionen und in der Automobilindustrie Anwendung, da sie Sicherheit gewährleisten und gleichzeitig das Transportgewicht minimieren. Forscherinnen und Forscher an der BAM wollen Faser-Kunststoff-Verbunde (FKV) durch den Zusatz von Nanopartikeln weiter verbessern. Ziel ist es, einen neuartigen Kunststoff zu entwickeln und zur Marktreife zu führen.
Präzisere Messverfahren für Kunststoffverbunde
„Wir entwickeln eine Art Baukastensystem, mit dem wir die Eigenschaften des Kunststoffverbunds durch speziell ausgewählte Nanopartikel vorhersagbar verändern können, um auf diesem Weg eine neue Klasse von Kunststoffen zu entwickeln“, erklärt Dr. Dorothee Silbernagl. Sie leitet als führende Wissenschaftlerin ein Projekt der Deutschen Forschungsgemeinschaft (DFG) zu FKV-Werkstoffen der Zukunft. Die BAM hat dafür mehrere neue Messverfahren entwickelt, mit denen das komplexe Innenleben der FKV bis zu einer Auflösung von zehn Nanometern studiert werden kann, also mit einer erheblich höheren Datendichte als bisher. Das ermöglicht einen präzisen Blick in das Material.
„Wir untersuchen aber nicht nur den Aufbau des Kunststoffverbundes sondern messen, wie die Struktur in diesem winzigen Abschnitt zum Beispiel auf äußere Kräfte reagiert“, sagt Prof. Dr. Heinz Sturm, der ebenfalls am Projekt beteiligt ist. Diese Informationen sind wichtig, wenn man die Eigenschaften eines Werkstoffs verstehen will, um ihn gezielt verändern zu können.
Denn kohlefaserverstärkte Kunststoffe sind ein komplexes System. Sie bestehen aus zwei Komponenten: den Kohlefasern und der Matrix, in der die Fasern eingebettet sind, beispielsweise ein Epoxidharz. Beide Bestandteile sind wichtig. Die Kohlefaser sorgt für eine hohe Zugfestigkeit, aber erst das Epoxidharz lässt die einzelnen Fasern wie ein Netzwerk gemeinsam auf eine äußere Kraft reagieren. Während der Kunststoffherstellung wird aus den Fasern meistens die Form gebildet und dann das flüssige Epoxidharz hinzugefügt. Das Harz härtet aus und verklebt dabei die Fasern als Matrix miteinander. „Es hat jahrzehntelang sehr starke und auch erfolgreiche Bemühungen gegeben, die Haftung zwischen der Kohlefaser und der Matrix, dem Epoxidharz, zu optimieren“, bilanziert Sturm, „man hat früh erkannt, dass dort die Schwachstelle des Werkstoffs liegt. Jetzt arbeiten wir an der Optimierung der Matrix.“ Denn wenn das Harz zu stark aushärtet, wird es spröde. Reagiert es zu wenig, erreicht es nicht die Steifigkeit, für die das Bauteil ausgelegt ist. Es wird zunehmend komplexer, diesen Prozess zu kontrollieren, weil gleichzeitig auch die Anbindung der Faser an die Matrix berücksichtigt werden muss.
Nanopartikel verändern mechanische Eigenschaften
Das DFG-Projekt untersucht, wie Nanopartikel die mechanischen Eigenschaften der Matrix beeinflussen. Bislang glaubte man, dass zur Erhöhung der Steifigkeit von FKVs nur Nanopartikel geeignet sind, die steifer sind als die Kunststoff-Matrix, in die sie eingerührt werden. Das konnten die Forscherinnen und Forscher anhand von Böhmit-Partikeln widerlegen. Böhmit ist eine besondere Form des Aluminiumhydroxids. Das Mineral kommt in der Natur vor, aber es entsteht als Nebenprodukt auch bei der Herstellung von Aluminium. „Wir haben Böhmit ausgewählt, weil wir nicht nur das reine Mineral verwenden können, sondern zusätzlich die Oberfläche der Partikel durch chemische Methoden optimieren können“, erklärt Sturm.
Analyse von Wirkprinzipien nanoskaliger Matrixadditive für den Faserverbundleichtbau Quelle: BAM
So nutzten die Forscherteams gleich zwei Effekte: Zum einen verändert die Anwesenheit der Nanopartikel den Aushärtungsprozess des Epoxidharzes. Zum anderen variieren sie die Oberfläche des Böhmits. Dadurch entstehen zusätzliche Anker für Bindungen innerhalb der Matrix oder zu den Kohlefasern. „Wenn wir Partikel verwenden, deren Oberfläche mit Essigsäure verändert wurde, wird das Produkt spröder, verwenden wir zur Modifikation Taurin, passiert das Gegenteil“, berichtet Silbernagl über erste Ergebnisse der Forschung. „So gelingt es, die Eigenschaften des FKV nur dadurch zu verändern, dass die Matrix angepasst wird, während der Beitrag der Kohlefasern unverändert bleibt.“
Mit diesem Wissen lassen sich gezielt die Steifigkeit oder die Schadenstoleranz des Materials verbessern. „Verbesserungen eines Werkstoffes können wir heute viel gezielter umsetzten, denn wir schauen genau hin, was auf der Nanoebene passiert“, sagt Silbernagl. Die BAM kann messen, wie sich die Eigenschaften des Kunststoffverbunds quantitativ verändern. „Wir können den elastischen Teil der Oberfläche berechnen und den Anteil, der die Energie von außen wie ein Stoßdämpfer aufnimmt“, erklärt Sturm. Wenn man dieses Verhältnis gezielt verändern kann, besitzt man ein wichtiges Hilfsmittel zum Design neuer Werkstoffe. „Das eröffnet neue Anwendungen im Leichtbau des Flugzeug- und Automobilbaus und wird nach Übertragung in die Produktionsprozesse auch den Bau leistungsfähigerer und preiswerter Windmühlenflügel ermöglichen“, erklärt Sturm.
Werkstoff der Zukunft soll individuell reagieren
Doch die Pläne der DFG-Forschergruppe gehen noch weiter. Sie wollen verschiedene Typen von Nanopartikeln mit ganz unterschiedlichen Oberflächen einsetzen. „Unsere Vision geht dahin, dass wir sehr viel mehr Additive hinzufügen, die je nach thermischer, chemischer oder mechanischer Belastung des Werkstoffs ganz individuell reagieren“, erklärt Sturm. Durch das Baukastenprinzip erhält der Werkstoff dann die vorher definierten Eigenschaften.