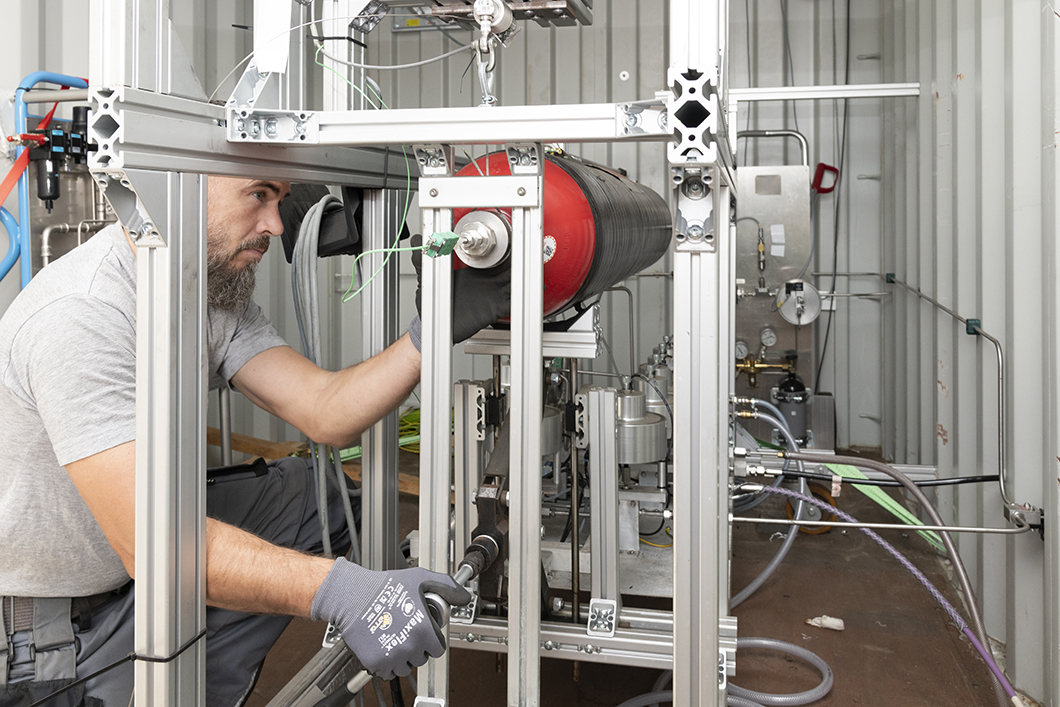
Anlage zum Befüllen der Wasserstoffspeicher
Quelle: BAM
Wasserstoff ist auch im Individualverkehr ein Antriebsmittel der Zukunft. Noch sind nur wenige Fahrzeuge mit dem Energieträger unterwegs. Die BAM forscht mit an der Entwicklung leichterer Tanks, die den Durchbruch beschleunigen könnten.
Elektro-Autos lassen sich nicht nur mit Lithium-Batterien, sondern auf umweltschonende und geräuscharme Weise auch mit Wasserstoff betreiben: Brennstoffzellen wandeln die chemische Energie des Gases in Strom um. Dabei entstehen keinerlei Stickoxide oder CO2, sondern lediglich Wasserdampf. Ein weiterer Vorteil dieser Antriebsvariante: Der Wasserstoff lässt sich, um Platz zu sparen, extrem verdichten: Ein Kilogramm des Gases enthält dann fast dreimal so viel Energie wie ein Kilogramm Erdöl. So erzielen Fahrzeuge, die heute auf dem Markt sind, bereits Reichweiten von etwa 500 Kilometern.
Ein Druck wie am Grund des Marianengrabens
Wasserstoff ist also ein vielversprechender Energieträger bei der Ablösung von Verbrennungsmotoren durch modernere Aggregate. Dennoch sind auf Deutschlands Straßen erst etwa 600 Wasserstoffautos unterwegs. Das liegt zum einen am noch spärlich ausgebauten Versorgungsnetz, das jedoch kontinuierlich wächst. Aktuell existieren im Bundesgebiet rund 80 entsprechend ausgerüstete Tankstellen – und damit mehr als in jedem anderen Land in Europa. Zum anderen sind die Fahrzeuge aber noch relativ teuer.
Ein wesentlicher Kostenfaktor sind die Behälter, die den Wasserstoff aufnehmen. Die Autohersteller verteilen sie zumeist auf zwei oder drei Gasspeicher mit einem Fassungsvermögen von insgesamt etwa 150 Litern und verbauen sie zwischen Vorder- und Hinterachse. Die Tanks müssen besonders hohe Sicherheitsanforderungen erfüllen, denn sie werden bis auf 875 bar befüllt. Das entspricht etwa dem Druck, der am Grund des pazifischen Marianengrabens herrscht, der mit rund 11.000 Metern tiefsten Stelle der Weltmeere. Zudem ist Wasserstoff entzündlich. „Bei einem Unfall muss gewährleistet sein, dass die Gasspeicher den mechanischen Kräften standhalten, die auf sie einwirken, und möglichst kein Gas austritt“, sagt Georg Mair. Der promovierte Ingenieur koordiniert die Beteiligung der BAM am Forschungsvorhaben DELFIN. Unter diesem Namen haben sich Kooperationspartner aus der Auto- und Zuliefererindustrie, Hersteller von Karbonfasern, Unternehmen der kunststoffverarbeitenden Industrie sowie wissenschaftliche Einrichtungen zusammengeschlossen. „Wir forschen im Rahmen eines Programms der Bundesregierung gemeinsam an neuen Wasserstofftanks, die natürlich alle gesetzlichen Sicherheitsanforderungen erfüllen, aber zugleich leichter und damit kostengünstiger zu produzieren sind“, so Mair.
Gemeinsam wollen die Partner in einem mehrstufigen Prozess den Prototypen eines Gasspeichers entwickeln. Bisher sind die Tanks knapp einen Meter lang und bestehen aus einem Innenbehälter aus Kunststoff, dem sogenannten Liner, der den Wasserstoff dicht einschließen soll. Umwickelt ist er mit kilometerlangen Strängen, die sich wiederum aus abertausenden nur wenige tausendstel Millimeter dünnen Fasern aus Kohlenstoff zusammensetzen und die dem Tank erst seine Festigkeit verleihen. „Bei der Herstellung der Speicher sind die Karbonfasern ein entscheidender Punkt“, erklärt Mair. „Sie machen etwa ein Drittel der Kosten aus.“ Der neue Prototyp soll möglichst um ein Zehntel günstiger zu produzieren sein und bis zu 15 Prozent an Gewicht einsparen – ohne Einbußen bei der Sicherheit.
Die Grenzen des Materials austesten: verschiedene Szenarien
„Zunächst testen wir an einem Referenzbehälter – also an einem schon existierenden Speicher – die Grenzen des Materials aus“, sagt Georg Mair. „Damit verschaffen wir uns eine Vergleichsgrundlage, die es in dieser Art noch nicht gibt. In einem zweiten Schritt werden wir verbesserte Speicher prüfen. Aus diesen soll in einem dritten Schritt ein Prototyp hervorgehen.“
Auf Gasspeicher wirken große Kräfte von innen und von außen ein. Zum einen müssen sie dem enormen Druck der komprimierten Tankfüllung standhalten. Dazu werden an mehreren Exemplaren des Referenzbehälters eine Reihe von speziellen Berstprüfungen durchgeführt: In die bereits mit Wasser vorgefüllten Tanks werden über mehrere Stunden zusätzlich einige Liter der Flüssigkeit gepresst. Auf diese Weise wird langsam, aber kontinuierlich und mit hoher Präzision der Innendruck erhöht. „Wir blasen die Speicher praktisch wie einen Luftballon auf – nur mit Wasser. Das machen wir so lange, bis sie bersten“, so Mair. Bei dem Test sind die Gasspeicher in einen stählernen Schutzbehälter eingeschlossen. Der wiederum ist von einem Container umgeben, sodass beim Bersten keine Gefahr für das Prüfteam besteht. Die bisherigen Prüfungen haben gezeigt, dass die Referenzbehälter einen Innendruck von rund 2000 bar aushalten.
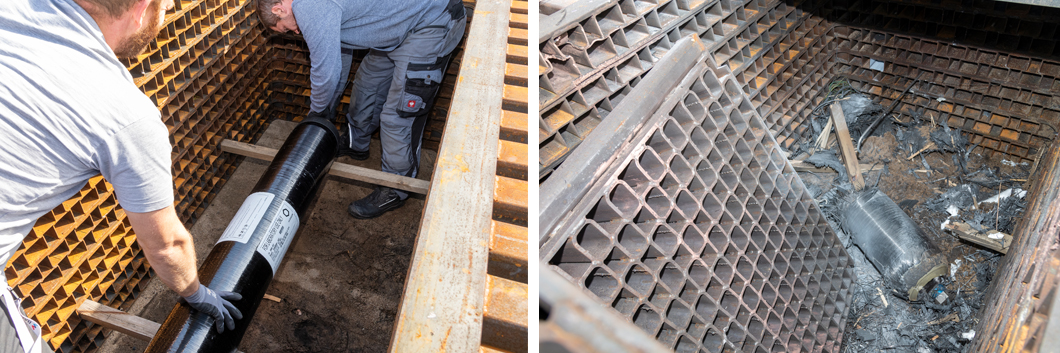
Links: Umgeben von einem stählernen Splitterschutz wird der Speicher zum Bersten gebracht. Rechts: Reste des geborstenen Wasserstoffspeichers
Quelle: BAM
Um ihre Lebensdauer zu prüfen, werden die Tanks einem weiteren Test ausgesetzt: Alle 15 Sekunden wird der Innendruck des mit Wasser gefüllten Speichers auf 875 bar erhöht – und sofort wieder entlastet. 50.000 dieser schnellen Wechsel führt das Team binnen einer Woche durch. So simulieren sie die Belastung beim Tanken, der das Material über viele Jahre ausgesetzt wäre. Die Testreihe gibt ihnen zusätzlichen Aufschluss über die Festigkeit der Speicher.
Jeder Wasserstofftank muss zudem beweisen, dass er auch äußeren mechanischen Belastungen standhalten kann, wie sie etwa bei einem Auffahrunfall entstehen können. Bei diesen Szenarien darf ebenfalls kein Gas aus den Speichern austreten.
Von einem selbstkonzipierten Fallturm will das BAM-Team eine stählerne Halbkugel an einem bis zu 200 Kilogramm schweren Gewicht auf Prüfexemplare des leeren, teil- oder vollbetankten Referenzbehälters stürzen lassen. Sie werden anschließend den Kunststoff des Liners und die Wickelstränge der Karbonfasern im Computertomografen auf feine Risse untersuchen – Veränderungen, die mit dem bloßen Auge nicht zu erkennen wären. Danach werden sie die so vorgeschädigten Speicher erneut mithilfe von Berstprüfungen auf ihre Restfestigkeit testen. Erst dann lässt sich beurteilen, wie sicher die Prüfmuster unter diesen Extrembedingungen sind, und abschätzen, ob auch ein leichterer Speicher den Zulassungsprozess bestehen würde.
Georg Mair ist da zuversichtlich: „Wenn man die Entwicklungen rund um Wasserstoff weltweit betrachtet, dann wird der Energieträger in nicht allzu ferner Zukunft Pkw mit hoher Reichweite und Lkw, auch Züge und Schiffe CO2-neutral und geräuscharm antreiben. Um diese Entwicklungen in Deutschland aktiv mitgestalten zu können, brauchen wir leichte, günstige und sichere Speicher, die in großer Stückzahl hergestellt werden.“