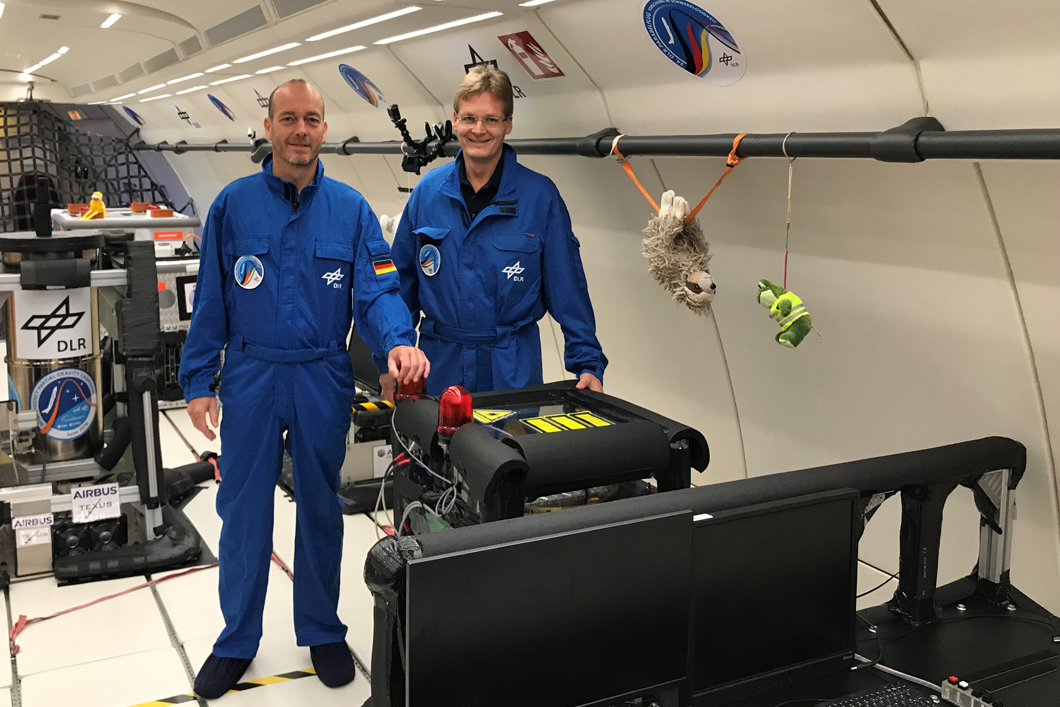
Prof. Dr. Jens Günster, Head of the Ceramic Processing and Biomaterials Division at BAM (left) and Prof. Dr. Andreas Meyer, Head of Institute of Materials Physics in Space at DLR (right)
Source: BAM, Division Ceramic Processing and Biomaterials
Research in zero gravity: Prof. Dr Jens Günster, Head of the Ceramic Processing and Biomaterials Division and Professor for high-performance ceramics at TU Clausthal carried out experiments on additive manufacturing in microgravity conditions. The goal is to enable the manufacture of components – such as tools – in space. Over the last three years, the team has taken part in the DLR’s (German Space Center) parabolic flights with the project ‘Powder-based additive manufacturing in zero gravity’ in an effort to test the devices and methods developed under real conditions. Investigations are currently underway for a test run in a research rocket. For this purpose, a completely new system must be developed based on the experience of previous experiments in parabolic flights.
Additive manufacturing, also known as 3D printing, offers numerous possibilities to produce components from liquid, powdered and filamentary source material. As a result, materials from all classes such as metals, plastics and ceramics, but also composite materials, are available. In summary, a multitude of components or tools can be produced very flexibly and swiftly from the same source material using additive manufacturing, but most importantly: they can be produced directly at the respective location. Thus, applications in space travel – in Earth orbit or beyond, e.g. bases on the moon or Mars or during flights thereto – will also be of great interest in the future.
The adaptation of such manufacturing methods for use in reduced gravity is by no means trivial, even if they have been well tested on earth and are ready to be placed on the market. Firstly, there are radically different requirements for the hardware of the corresponding production machines, and secondly, the materials used in space travel are often more sophisticated.
The subject of the research project is the SLS (Selective Laser Sintering) process, in which the desired component is formed layer by layer from individual layers of metallic powder using a focused laser beam. The spectrum of possible materials in this process is very broad. One of the biggest challenges of this zero-gravity process is the handling of the metal powder and the targeted application of a densely packed powder layer with uniform thickness. These parameters dictate the quality and material properties of the finished component. In addition, this layer must remain stable on the printing bed until the laser process is completed and the next layer is applied. In order to achieve this goal, a gas flow is activated, and the individual powder particles are sucked into the pressure bed. This process of stabilising the powder in the pressure range has already been tested in various variations on parabolic flights and has shown a high degree of reliability.
A completely new system is to be tested in the current parabolic flight which will be based on the proven principle. The new system has been designed as a payload of a research rocket and is to be deployed for the first time on a MAPHEUS rocket in 2020. The newly developed manufacturing unit is fully automated, has an independent power supply, is robust when subjected to the loads that occur during a rocket launch and is also lightweight. The manufacturing process can be monitored from the ground via a telemetry link. In addition to testing the hardware in zero gravity for the first time, the aim is also to optimise system parameters for diverse and demanding materials, such as solid metallic glass.