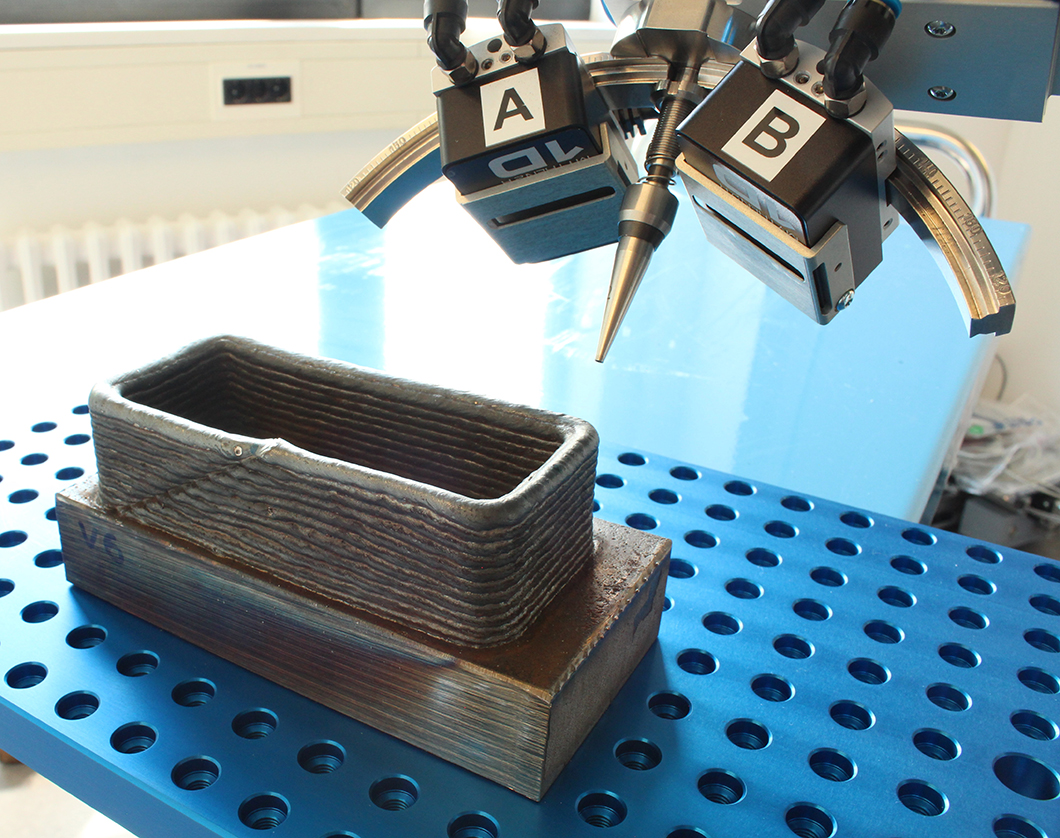
Residual stress analysis on a generatively welded component sample made of high-strength steel
Source: BAM
Project period
01/05/2020 - 30/07/2022
Project type
Collaborative research project
Project status
Ongoing
Description
The aim of the KaRAt project is to enable steel processing users to additive manufacture and modify components and semi-finished products made of high-strength steel in a way that is crack-proof and suitable for stresses.
Location
Bundesanstalt für Materialforschung und -prüfung
Unter den Eichen 87
12205 Berlin
Karsten Wandtke preparing the X-ray diffractometer for the determination of residual stresses Source: BAM
Source: BAM
The aim of the project is to develop processing recommendations and a practicable cold crack test for additive MSG welding of high-strength steels. This enables manufacturing companies, especially SMEs, to carry out highly economical, crack-resistant and stress-resistant additive manufacturing and modification of high-strength components. The associated increase in resource efficiency and realisation of lightweight structures is of social relevance.
Source: BAM
The focus of the investigations is on high-strength welding consumables whose alloy compositions have been optimised for additive MSG welding. In welding experiments, component samples with defined geometries are produced. Analyses of the microstructure, mechanical-technological properties and residual stress state as a function of the welding parameters, heat conduction, design, post-treatment and post-processing allow boundary conditions to be derived in a targeted manner.
Source: BAM
Project partners
The KaRGenf project is a research cooperation between BAM and the Chemnitz University of Technology, Chair of Welding Technology.
Funding
The IGF project IGF No. 21162 BG (P 1380) of the Forschungsvereinigung Stahlanwendung e. V. is funded by the Federal Ministry of Economics and Climate Action (BMWK) via AiF within the framework of the programme for the promotion of joint industrial research (IGF) on the basis of a resolution of the German Bundestag.
Additive welding of high-strength steel structures
One of the major climate goals is to reduce greenhouse gases. Lightweight construction contributes to achieving this goal.
Structural steels with high strength offer the possibility of achieving considerable reductions in weight and processing costs by reducing wall thickness. Process emissions can be reduced through lower consumption of energy, materials and raw materials. However, this causes lightweight parts and structures to become more complex. Additive manufacturing steps offer great potential for resource-saving and efficient production and modification of these structures. In addition, the production of near-net-shape components can save on costly machining production steps.
In conventional manufacturing, the most important welding joining process is metal shielded arc welding (MSG welding). Based on this, the shaping process Wire Arc Additive Manufacturing (WAAM) has been developed in recent years. Based on high-strength filler materials for joint welding, special welding wires for the production of high-strength components using WAAM are already available on the market.
Scientific-technical and economic problem definition
However, a broad economic application in industry is still hindered by the lack of quantitative statements on the production-related stresses (residual stresses) and the component safety during production and operation. This applies in particular to the influences of the manufacturing process, the design, the post-treatment and the machining. For users, the design and manufacture of constructions made of high-strength materials is often complicated by a narrow working window for heat conduction. High tensile residual stresses, combined with reduced mechanical properties, can have a significant negative impact on crack resistance during production and on load-bearing capacity in service. Currently, the only way for these components to be approved is through time-consuming and cost-intensive quality testing and proof of compliance with the relevant standards.
Crack safety and stress optimisation for WAAM components
The aim of the KaRAt project is to enable steel processing users to additive manufacture and modify components and semi-finished products made of high-strength steel in a way that is crack-proof and suitable for the stresses involved. To this end, knowledge of the complex interactions between the welding process and heat guidance as well as the influence of the design on the resulting residual stresses is being developed. At the same time, the influences on the mechanical-technological properties are systematically analysed. In addition, the effects of separating processes are to be clarified, as these directly influence the residual stress state and trigger significant distortion of the components. Finally, a special self-stressing cold crack test for additive welding will be developed and processing recommendations and standard specifications will be worked out.
Project coordination
BAM Bundesanstalt für Materialforschung und -prüfung (BAM)
Division Weld Mechanics
Division Testing Devices and Equipment
Project partner
The KaRGenf project is a research cooperation between the Bundesanstalt für Materialforschung und -prüfung (BAM) and the Chemnitz University of Technology, Chair of Welding Technology.
Funding
The IGF project IGF No. 21162 BG (P 1380) of the Forschungsvereinigung Stahlanwendung e. V. is funded by the Federal Ministry of Economics and Climate Action (BMWK) via AiF within the framework of the programme for the promotion of joint industrial research (IGF) on the basis of a resolution of the German Bundestag.

Source: AiF and BMWK